Thin-film silicon uses about one-hundredth the amount of silicon used by crystalline silicon PV but now that the silicon shortage is over what will keep TF Si'c current 43% market share from dropping?
Robert Nolan | NanoMarkets, LC
How Improvements in Thin-Film Silicon PV Will Keep it Alive in the Marketplace
Thin-film silicon (TF Si) photovoltaics has been around for a long time, but went through boom times during a period when there wasn’t enough crystalline silicon to satisfy demand by the PV industry; TF Si uses about one-hundredth the amount of silicon used by crystalline silicon PV. The most mature of the TFPV technologies, TF Si currently accounts for about 43 percent of the TFPV market.
But now the silicon shortage is over leaving TF Si PV to compete on its own merits, at a time when other thin-film PV technologies, mainly CIGS and CdTe PV, offer stiff competition. Such technologies offer the same lightweight and small form factor as TF Si but with higher conversion efficiencies. CdTe has the lowest cost-per-megawatt of all TFPV technologies. CIGS PV, on the other hand, offers the highest efficiency of all TFPV technologies—20 percent for champion cells.
While there may be some niche applications in which TF Si offers some benefit over the other TFPV technologies, this will not help TF Si PV to retain its share of the solar market. Only cost and/or performance improvements will help it hold onto its market share. NanoMarkets suspects these improvements—if they come at all—will arrive through changes in the absorber layer. We believe that there are four specific technical directions from which these improvements might emerge: multi-junction cells, cells using micro-silicon materials, cells using nanocrystalline silicon and printed silicon.
Multi-Junction Cells: Today, most TF Si PV is based on amorphous silicon (a-Si). One reason for the low efficiency of a-Si PV is its bandgap, which is in the range of 1.7–1.9 eV—higher than ideal for a single-junction cell. But a-Si also suffers from the Staebler-Wronski (S-W) Effect, which causes significant degradation in the power output of the cell when exposed to the sun, on the order of 15 percent to 35 percent. While making the layers thinner can reduce the impact of the S-W Effect by increasing the electric field strength across the material, the result would also mean a reduction in light absorption and in the (already low) efficiency of the cell.
To counter these effects, several a-Si PV firms have started manufacturing multi-junction cells up to triple junction as a way to boost a-Si PV’s performance. Stacking thin layers on top of one another to form multi-junction cells improves performance on several counts. These layers are less susceptible to the S-W effect and the high bandgap of a-Si in the top cell lets a large proportion of light through to the next underlying cell, allowing the underlying cell, which typically uses a-SiGe to lower its bandgap, to generate significant current.
This approach represents a significant improvement over a simple a-Si cell, but there are also drawbacks. Specifically, the multi-junction approach adds costs in (at least) two ways. First there is the additional cost of the germanium for alloying. Then, more significantly, there is the increased complexity of the cell adding more cost and reducing yields.
Multi-junction cells of this kind can boost a-Si’s conversion efficiency to about 12 percent in champion cells or 10 percent for mass-produced, commercial cells. But there is diminishing marginal utility in this approach, not just in money terms but also in terms of performance, since each successive junction adds less to the overall performance of the cell.
Microcrystalline silicon: While a multi-junction TF Si PV structure using a-SiGe alloy for the underlying cells provides a much-needed performance boost, a similar boost can be obtained at lower cost by using microcrystalline silicon (µc-Si) as the lower absorber. The bandgap of µc-Si is about 1.1 eV, similar to that of bulk c-Si and a good complement as the bottom absorber to an a-Si top absorber. Using µc-Si combines the stable, higher efficiencies of c-Si technology with the simpler and cheaper large-area deposition technology associated with amorphous silicon. In addition, µc-Si uses very similar processing to a-Si and µc-Si cells can be fabricated on identical equipment to that used for a-Si.
This means that there would be no need for a major changeover in manufacturing infrastructure if a firm shifts from a conventional a-Si to a µc-Si product. And the likelihood is that cell makers may want to make that change since µc-Si may be more robust than a-Si cells and because—at least according to one company—µc-Si can offer an increase in power over conventional a-Si PV cells.
Of course, as usual, nothing comes without a cost. The key issues for µc-Si from a technology viewpoint are control of the morphology and size distribution of the deposited µc-Si. Any changes to the size distribution or the balance between crystalline and amorphous composition will change the properties of the film and hence the efficiency of the cell. Because this process window is very small, advanced manufacturing techniques and process control procedures borrowed from the semiconductor and display manufacturing industries are key to success with µc-Si cells and naturally this adds cost.
Nanocrystalline silicon: While multi-junction cells and µc-Si cells are fairly established technology, a more speculative approach to improving the performance of TF Si PV cells is to shrink the sizes of the silicon particles to the nano scale, a natural extension beyond µc-Si. Specifically, nanocrystalline silicon (nc-Si) holds potential for improvements beyond those achievable with µc-Si because below about 100 nm in diameter the properties of silicon crystals begin to change. At very small sizes—around 5 nm or so—nanoparticles become “quantum dots.”
Prepared properly, silicon quantum dots can generate more than one exciton upon absorption of a high-energy photon. Conventional absorbers only generate one exciton and any excess photon energy just creates heat. Multiple exciton generation (MEG) is the feature that could allow nanosilicon PV to reach remarkable efficiencies—50 percent is talked about as a reachable goal. Such efficiencies would fundamentally change the value proposition of PV, but no one expects them to appear in a commercial product for many years.
Printed silicon: Beyond nanocrystalline silicon are silicon inks for printing—a natural extension of using nc-Si, which can fairly easily be turned into inks.
What printing offers is a fabrication approach that is much less expensive than more conventional approaches. Current deposition methods such as CVD, laser deposition, and plasma methods, are expensive, requiring vacuum chambers, high energies and temperatures, and they are often inefficient in terms of material usage.
Printing of silicon aims to eliminate most or all of these issues, reducing costs as well as enabling a wider variety of substrates and applications. Another key advantage of the silicon inks—particularly the ones made with nanocrystals—is that it is possible to tailor the composition and size distribution of the nanocrystals in the ink to optimize the performance of the printed films. Varying the composition of ink particles may enable the cell to absorb a wider spectrum of light with a single film compared to the multiple junctions necessary with traditional high-performance a-Si PV cells.
But these advantages, while significant, are not yet the focus of printed silicon PV. For now, the goal is to obtain similar performance to conventionally deposited silicon while entering a new realm of scalability and cost reduction. And printed silicon PV has a long way to go. For one thing, functional printing of all kinds is harder to implement than the textbooks suggest.
Whether all this is enough to “save” thin film silicon in an era of silicon abundance remains to be seen. However, there is little doubt that silicon PV will still be a major part of the TF PV market for many years to come, although soon the average silicon cell will have structures and chemistries that look nothing like the a-Si cells of years past, such as those used in pocket calculators.
About NanoMarkets LC
NanoMarkets is a leading provider of market and technology research and industry analysis services for advanced materials and emerging energy and electronics related fields. The firm has published multiple reports and papers related to thin-film, organic and printable photovoltaics market and technology opportunities. Please visit www.nanomarkets.net to access NanoMarkets list of reports, articles and executive summaries available for downloading.
The content & opinions in this article are the author’s and do not necessarily represent the views of AltEnergyMag
Comments (0)
This post does not have any comments. Be the first to leave a comment below.
Featured Product
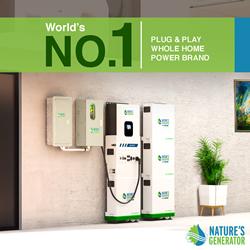