Researchers at the National Renewable Energy Laboratory are using multiphysics simulation to better understand and optimize the conversion process for plant-derived biofuels.
Making Biofuel a Cost-Effective, Renewable Source of Energy
Jennifer Segui | COMSOL
Biofuels could potentially replace fossil fuels for many applications, offering an alternative source of energy to heat buildings, generate electricity, and keep the transportation industry moving.
There are many benefits to producing biofuels from plant-based materials, generally referred to as biomass. Such fuels are renewable, clean-burning, and carbon-neutral, producing no more carbon dioxide than is sequestered by its original plant source. However, biofuel availability is still fairly limited for its most common use—in vehicles. As of 2014, the U.S. Energy Information Administration reports that only 2% of retail fueling stations were offering the ethanol-based fuel E85.
The production process itself poses an important economic barrier to the widespread use of biofuels. Research at the National Renewable Energy Laboratory (NREL), supported by the Computational Pyrolysis Consortium, is directed toward gaining a better understanding of the physical processes behind biofuel conversion by developing computational models that feature the most accurate representation of biomass particle geometry to date. Such a model could then be used to improve reactor design and operation as required for the mass production of biofuel.
This work can ultimately make biofuel use more cost-effective and competitive with traditional nonrenewable fuels, some of which will be depleted in mere decades.
Producing Fuel from Plants
Thermochemical processes such as pyrolysis, which is shown in Figure 1, use exposure to high temperatures to break down and convert biomass particles to liquid biofuels that can support many everyday life activities. Improving fast pyrolysis, a pre-commercial thermochemical conversion route often used for woody biomass, is one objective of the research program at NREL, and is described in more detail in the sidebar below.

Figure 1. In preparation for pyrolysis, the woody biomass shown at left has been milled and may also undergo additional chemical treatment. Several physical processes including heat transfer, mass transfer, chemical reactions, and phase change must be taken into account to develop a complete model of pyrolysis, shown at right. The flask in the photo collects the condensed bio-oil vapors resulting from pyrolysis in a pre-commercial reactor. Photo credits: Warren Gretz, NREL 05756 (left) and Phil Shepherd, NREL 03677 (right).
Peter Ciesielski, a research scientist at NREL, and his colleagues are using multiphysics simulation to gain insight into the fundamental processes behind biomass conversion via pyrolysis, starting with investigating heat and mass transfer.
Efficient heat and mass transfer through biomass particles minimizes char formation and accelerates favorable reactions by facilitating the penetration of conversion catalysts and the escape of desired products. Ciesielski’s work considers the effect of size, shape, and internal microstructure of biomass particles, which is determined by the species of wood and by the milling process used prior to pyrolysis.
An Accurate Model of Biomass
Computational studies designed to understand and optimize the biofuel conversion process have always used simplified biomass particle geometry that ignored internal microstructure.
Ciesielski’s research aims to provide insight into the heat and mass transfer in biomass by developing a model in the COMSOL Multiphysics® software that takes internal microstructure into account. “Since COMSOL has the geometry tools, physics, meshing, and solvers already implemented, we can spend more time making the biomass model geometry really accurate,” explains Ciesielski.
In order to generate 3D models of biomass for use in COMSOL simulations, a confluence of imaging methods was used to characterize the external morphology and size distribution as well as the internal microstructure of each type of biomass. Examples of images that were acquired for this study are shown in Figure 2.
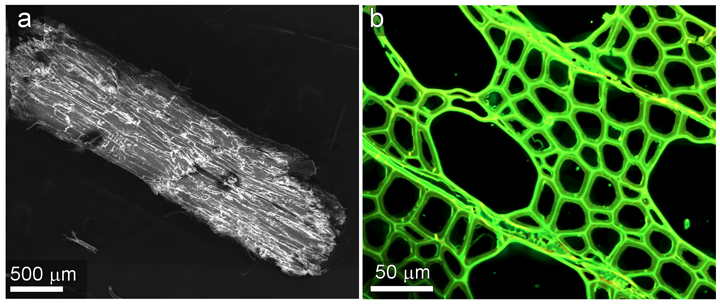
Figure 2. Left: A scanning electron micrograph confirms the shape and structure of a hardwood biomass particle. Right: A confocal scanning laser micrograph of a particle cross section shows the microstructure.
A solid geometry was generated using the external and internal dimensions of biomass particles, determined from the images, as input to a series of Boolean geometry operations in COMSOL. The complete geometry consists of two domains, as shown in Figure 3.
Figure 3. Left: COMSOL® software model geometry featuring a fluid domain surrounding a hardwood biomass particle. Right: The temperature distribution from a transient simulation of conjugate heat transfer is shown.
Simulating Pyrolysis: Heat and Mass Transfer
Biomass decomposition via fast pyrolysis starts with the application of high temperatures (about 500oC) to an oxygen-free reaction vessel for a few seconds. Applying these conditions, the Conjugate Heat Transfer interface in COMSOL was used to simulate heat transfer between the outer fluid domain shown in Figure 3a, consisting of nitrogen gas, and the biomass particle. Heat transfer in the fluid domain is predominately by convection, whereas at the interface and through the biomass particle, heat transfer is by conduction only.
The simulations were run on a high-performance computing (HPC) cluster using one or two compute nodes each consisting of 24 Intel® Xeon® Ivy Bridge processors with 64 GB of RAM. The results in Figure 3b show the temperature distribution in a hardwood biomass particle 0.5 seconds into a transient simulation of conjugate heat transfer. For a given particle size, shape, and microstructure, it is possible to determine the amount of time required for the entire particle, particularly the center, to reach optimal temperatures for decomposition.
In a separate simulation, the diffusion of sulfuric acid, a chemical used to pretreat biomass prior to its conversion to biofuel, was evaluated. The Transport of Diluted Species interface was used for transient simulations of mass transport in the microstructure and solid particle geometries where the surrounding fluid in this case was water.
The results from both the heat and mass transfer studies indicate that a solid model, particularly a spherical one, may not offer sufficient accuracy to evaluate and optimize biofuel conversion processes and that the use of a microstructured model is justified.
Input for Large-Scale Reactor Design
While the present study focuses on heat and mass transfer in biomass, rapid phase transitions and chemical reactions are critical to fully understand and optimize biofuel production via fast pyrolysis. Ciesielski’s ongoing work involves adding these to his simulations, the ability to do so being an important reason why COMSOL was chosen.
Ultimately, however, the team has bigger plans for the computational model. By performing simulations to gain a fundamental understanding of transport in biomass, effective correlations for low-order models can be determined for a range of process parameters and biomass feedstocks. These correlations can be used to optimize the design and operation of large-scale reactors for mass production of biofuel, making the process more efficient and cost-effective.
Computational Pyrolysis Consortium
Ciesielski’s work, supported by the Computational Pyrolysis Consortium and funded by the U.S. Department of Energy, is a collaborative effort between researchers at NREL, Oakridge National Laboratory (ORNL), and the National Institute of Standards and Technology (NIST). The collaboration brings together experts in computational modeling, biomass conversion, reactor design, and materials characterization to optimize biofuel production via pyrolysis.
To appreciate the significance of pyrolysis—first think about a fire, but take away the flame. Pyrolysis is a thermochemical conversion route that causes decomposition of biomass via exposure to high temperatures and in the absence of oxygen. Without oxygen, there is no combustion or flame. The result of pyrolysis is char, a liquid product often referred to as bio-oil, and gaseous products of the chemical reaction. Biofuels are produced from further refinement of the bio-oil.
Fast pyrolysis research at NREL takes the process one step further by using an extremely high rate of heat transfer to break down biomass, where internal temperatures reach upwards of 500˚C within 1 second.
Peter Ciesielski, a research scientist at NREL, is pictured next to the scanning electron microscope used to acquire images of wood biomass for his work published in Energy & Fuels1.
References:
1 P. N. Ciesielski, et. al., Energy Fuels, 2015, 29(1), pp 242-254.
The content & opinions in this article are the author’s and do not necessarily represent the views of AltEnergyMag
Comments (0)
This post does not have any comments. Be the first to leave a comment below.
Featured Product
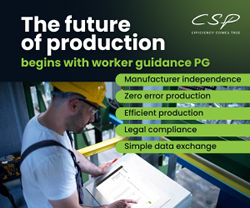
Quality assurance in the manufacturing industry
Efficiency and precision with CSP software. In the highly competitive world of manufacturing, quality assurance is a critical factor for success. CSP offers you state-of-the-art software solutions specifically designed to ensure the highest standards of quality assurance in the manufacturing industry.