Developing a predictable O&M strategy at the outset of a project will ensure the bankability and a robust ROI throughout the systems lifetime. Project owners and developers that thoroughly evaluate O&M considerations of their tracker investments will find that the higher energy performance, predictive analytics and long-term reliability of single-axis, self-powered trackers will provide a lower overall levelized cost of energy than fixed-tilt racking or conventional tracking systems.
Data Rules: Intelligent Solar Trackers Reduce Risk, Downtime and O&M Costs
Marty Rogers
Solar asset managers are data mining now more than ever. But just collecting data doesn’t reduce O&M costs. It’s how intelligent tracking systems and asset managers use that data that reduces truck rolls and increases long-term ROI. In this fourth and final installment of my “Best Practices for Solar Tracker O&M” blog series based on our new white paper and recent GTM webinar, we’ll take a deep dive into how smart single-axis trackers (SATs) enable asset managers to intelligently oversee their tracking systems based on real-time data analysis while also considering several key quality and reliability factors.
Apples to Apples: The Cost of Unlinked and Linked-Row Trackers Going Down
In my previous post in this series, I discussed SAT resiliency during severe weather events, but even in perfect weather, the unexpected can happen, such as a breakdown in a tracker motor. Intelligent tracker systems that communicate such failures to the asset or O&M manager reduce downtime, but there’s a significant difference between the loss in kilowatt-hour production of a linked-row system and an unlinked tracker system like NX Horizon solar tracker.
In an apples-to-apples comparison, a typical breakdown of critical components such as the motor, communication systems and gear will affect only one unlinked row (25 kW) as opposed to 700 kW for a linked-row tracker. On a yearly basis, the kilowatt-hour loss is approximately 150 kWh for NEXTracker’s system versus 8500 kWh for linked-row trackers—a considerable potential downtime cost for large utility-scale plants.
Avoiding the Truck Roll: Intelligent Corrective-Based Maintenance
Since O&M-related labor is the biggest cost factor when maintaining solar power plants, each truck roll avoided and man-hour saved translates directly to the bottom line, and that means asset managers require smart SAT monitoring and data analysis. Since tracking is critical to achieving the highest energy yields, having access to minute-by-minute tracker performance data helps system owners and their O&M partners understand when and where to place maintenance resources to manage assets effectively while keeping a low LCOE.
NEXTracker’s intelligent cloud-based Digital O&M™ software provides real-time and historical data analysis, monitoring of row-specific tracker angles, controller health and battery performance, and motor and slew gear performance, among other metrics. This powerful system, which is integrated into Flex’s Connected Intelligence™ cyber-secure network, provides a single map view where system operators can identify issues at a glance and drill down to individual rows.
Built to Last: Quality and Reliability Considerations
Beyond intelligent system design and comprehensive data acquisition and analysis, asset managers have to consider other factors for long-term profitability, such as bankability and experience.
When it comes to experience, NEXTracker was named the number-one solar tracker company by GTM Research for the second year in a row.[1] For asset or O&M managers, it’s important to know that their colleagues select NEXTracker for the best long-term ROI. Moreover, NEXTracker has contracted or installed 8 GW of projects worldwide, in every climate, region and soil type. As for bankability, with our parent company Flex’s 100 manufacturing sites in 30 countries, NEXTracker solutions are scalable and reliable for the long term.
Testing and Third-Party Validation
Asset managers must also be vigilant in evaluating a manufacturer’s quality, reliability and warranty programs. These programs should include internal as well as third-party testing and evaluation, such as accelerated life tests, outdoor tests, and factory acceptance testing of all system components and materials.
NEXTracker motors undergo all of these tests, including accelerated testing of more than 68.5 years, with no failing seals or significant signs of wear. NEXTracker’s Self-Powered Controller (SPC) has been evaluated for reliability according to Telcordia SR-332, a globally accepted standard for calculating the mean time between failure of electronic components. NEXTracker’s structural elements have been certified by independent third-party engineers, while all components are sourced from best-in-class, ISO 9001-certified vendors.
Training and Support
Ensuring that EPCs, installers and O&M providers have the training and techniques to correctly install, commission and maintain the system over time is fundamental to a project’s success. NEXTracker provides in-depth, hands-on installation training for the boots on the ground to properly install and maintain the NEXTracker Self-Powered Tracker – whether your installer teams are in Latin America, Australia, India or the US, we offer standard trainings or custom trainings depending on customer demand. Our PowerworX™ Academy installer training program is registered with the North American Board of Certified Energy Practitioners (NABCEP) for continuing education credits. Check out this video to get a sense of our program.
Customer support in multiple languages can often play an important role in tracking purchase decisions. As the leading provider of trackers around the world, we understand how important it is for asset managers and EPCs to have a direct contact with our global service and support team as well as our product managers and engineers to reduce downtime or project delays. Because we have a local presence in many regions, that support can be on the ground and in person, not just on the phone.
Conclusion
Developing a predictable O&M strategy at the outset of a project will ensure the bankability and a robust ROI throughout the system’s lifetime. Project owners and developers that thoroughly evaluate O&M considerations of their tracker investments will find that the higher energy performance, predictive analytics and long-term reliability of single-axis, self-powered trackers will provide a lower overall levelized cost of energy than fixed-tilt racking or conventional tracking systems.
(If you’re interested in reading the entire “Tracking Your Solar O&M Investment: Best Practices for Solar Tracker O&M” white paper, you can download it HERE, or watch the webinar with perspectives from several NEXTracker customers.)
[1] GTM Research, Global PV Tracker Landscape 2017. Data is in megawatts shipped in 2016.
The content & opinions in this article are the author’s and do not necessarily represent the views of AltEnergyMag
Comments (0)
This post does not have any comments. Be the first to leave a comment below.
Featured Product
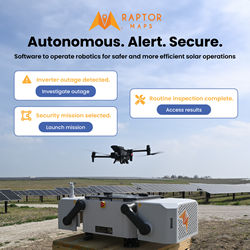