Scotch Whisky Goes Green
Permission Granted for Rothes Renewable Energy Project - An award-winning scheme which will reduce the carbon footprint of the whisky industry on Speyside has moved a step closer after being granted planning permission by Moray Council.
An award-winning scheme which will reduce the carbon footprint of the whisky industry on Speyside has moved a step closer after being granted planning permission by Moray Council.
The project is a joint development between Helius Energy plc and The Combination of Rothes Distillers Limited (CoRD) and will see the installation of a GreenSwitch' biomass-fuelled combined heat and power (CHP) plant to the rear of the CoRD's existing site to the north of Rothes.
The CHP unit will use a combination of distillery co-products and wood chip from sustainable sources to generate 7.2 megawatts of electricity, enough for 9,000 homes, which can be used onsite or exported to the National Grid.
As part of the project, a new GreenFields' plant will be built alongside the GreenSwitch' CHP unit and will turn the liquid co-product of whisky production, known as Pot Ale, into a concentrated organic fertiliser for use by local farmers.
The project was awarded the 'Best Environmental Initiative Award' at the Scottish Green Energy Awards 2008 in December.
Frank Burns, General Manager of CoRD, said:
"This is exciting news and allows us to proceed with this innovative project. Not only will it generate renewable heat and power, but it secures additional markets for our distillery co-products and helps to ensure the sustainability of malt whisky distilling on Speyside."
John Seed, Managing Director of Helius Energy, said:
"This is a major milestone in the development of CoRD's GreenSwitch' project, and in Helius Energy's wider plans for a pipeline of similar schemes. We look forward to working with CoRD to realise our vision for GreenSwitch' and making Rothes a showcase for innovation and environmental responsibility within the Scottish whisky industry."
The plant, which represents an investment of around £35 million, is expected to take 18 to 24 months to construct and will be the first such project to use draff and pot ale as a biomass fuel alongside wood.
- ENDS -
Notes for Editors
• The Helius Group was established to develop, install and operate biomass fired renewable electricity generation plants. These will help meet the growing need for reliable power from renewable fuels that help to overcome the issues of climate change associated with fossil fuels like coal and oil.
• Helius possesses a significant combination of knowledge of renewable energy markets, biomass energy technologies, biomass fuel sources, project development, implementation and operation of power generation plants.
• The Combination of Rothes Distillers was founded in 1904 to process the Pot Ale produced by the whisky distilleries in the Rothes area. It is owned by a combination of distilling companies - comprising The Edrington Group, Chivas Brothers, Glen Grant Distillery Ltd, Inver House Distillers, Diageo and Benriach Distillery Co. - and employs 21 people.
• Rothes is the first 5-8 MWe GreenSwitch' project. These are modular biomass power stations which are capable of utilising wet biomass and which will be located alongside existing industries which produce suitable co-products, such as distilleries and breweries.
• The solid grain product removed from the mash tun, prior to fermentation of the liquor, is known as draff. Pot Ale is a high-protein co-product removed prior to final distillation of the spirit.
• The GreenFields' process takes the co-products from distillery operations (including process water, pot ale and draff) and turns them into value inputs such as biomass fuel, liquid soil conditioner and animal feed.
Featured Product
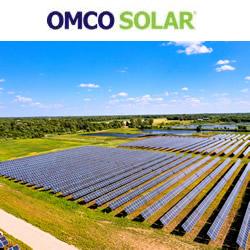
OMCO Origin® Factory-Direct Trackers
A One-In-Portrait (1P) solution for a wide range of solar projects within utility scale, distributed generation (DG), and community solar markets manufactured and factory preassembled in the USA at OMCO Solar with full-scale support, and design for quick, easy and safe installation, and fewer trackers per MW. OMCO makes all structural components with domestic steel and this balanced design allows for more accurate targeting and reduced energy consumption. OMCO Origin® Factory-Direct Trackers include universal module mounts with options for all commercially available modules, labor-saving bearings with 6 adjustable ways to compensate for posts and terrain issues, and foundation solutions for every terrain including OMCO C Piles.