Natcore Technology Demonstrates First Flexible Solar Cell Made With Its Proprietary LPD Process
"This is a major step forward in our goal of creating a low cost flexible solar cell"
RED BANK, N.J., July 11, 2013 - Scientists of Natcore Technology Inc. (TSX-V: NXT; NTCXF.PK), in collaboration with researchers at Rice University have successfully fabricated the first inorganic flexible thin film solar cell by solution processes. The work was reported in a recent issue of the journal Physical Chemistry Chemical Physics published by the Royal Society of Chemistry, volume 15, pages 3930-3938.
Using its patented liquid phase deposition (LPD) process, a cadmium/selenium (CdSe) absorber layer has been grown on a single-walled carbon nanotube (SWNT)-derived back contact substrate. The CdSe/SWNT layers show appropriate photo response. LPD was also used to grow a copper/selenium (CuSe) window layer onto which silver contacts were deposited. The resulting photovoltaic device shows a characteristic IV curve that confirms the potential for this process to form a flexible solar cell. No high temperature semiconductor processing of any kind was used to make the device.
"This is a major step forward in our goal of creating a low cost flexible solar cell," says Rice Professor Andrew R. Barron, a Natcore co-founder. "These results demonstrate the feasibility of our approach. This is the first step in moving this towards a commercial cell."
"The use of carbon nanotubes was chosen to create a back contact that is imbedded into the absorber layer, and thus decrease the diffusion length to the back contact, which should result in a lower percentage of hole electron recombination, and hence higher efficiency," commented Natcore's CTO/co-founder Dennis Flood.
"This is a most important milestone along the way to a low-cost flexible solar cell," says Natcore's CEO/President Chuck Provini.
"First, we've demonstrated the concept. We've shown the feasibility of using LPD to grow a whole cell on a flexible substrate that remains flexible even with all of the layers.
"Second, if we can marry this development with our multi-junction tandem solar cell technology, we'll have a truly world-changing event.
"And third, this technology should be adaptable to the production of roll-to-roll solar cells. That has been in our plans since we established our R&D Center in proximity to a former Kodak roll-to-roll photo film plant.
"Thin film has been burdened with two problems: low efficiency and high manufacturing cost. By combining this success with our multi-junction tandem solar cell, we could overcome both of those problems."
"Our next step," adds Provini," is to improve the quality and efficiency of the cell. Now we'll move the work from Dr. Andy Barron's lab at Rice to our own lab in Rochester. If we had adequate funds and adequate manpower, we could have a commercial-quality cell within a year.
Featured Product
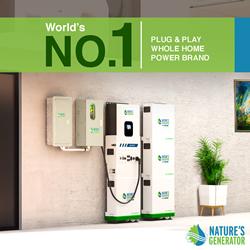
Nature's Generator MyGrid 10K
A 10,000W plug & play whole-home generator with a 10kWh LiFePO4 battery for reliable backup power. Features easy setup, flexible 120V/208-240V input, and solar/wind charging. Expandable with extra batteries or solar panels, and can pair two units for 20,000W for even larger energy needs. Powers your home during power outages, reduces electricity costs, and supports sustainable energy.