SolarBOS Installs Utility Scale Storage Battery for Amperex Technology Ltd.
The storage battery has been deployed by a San Francisco Bay Area Fortune 500 company at one of their research and development centers.
LIVERMORE, California (May, 2015) - SolarBOS is pleased to support Amperex Technology Limited (ATL) in the construction of their first utility scale storage battery in North America.
The 500KWH storage battery was installed in a 40 sea container and paired with a 1MW grid interactive inverter. The storage battery has been deployed by a San Francisco Bay Area Fortune 500 company at one of their research and development centers.
Amperex Technology Limited is among the top 4 global suppliers of lithium-ion batteries. ATL lithium batteries are used for consumer electronics, transportation and grid connected energy storage from as small as 5KWH to multi-megawatt hour installations.
"We are proud to support (ATL) with the installation of their utility scale energy storage battery." says Daniel Sherwood, Director of Product Management for SolarBOS. "Our deep experience manufacturing high voltage DC equipment for the solar industry translates easily into the emerging energy storage industry. We are able to help our customers integrate batteries with inverters as well as supply the high voltage DC connection panels and switch gear if required."
About Amperex Technology Limited
Amperex Technology Limited (ATL) is one of the top 4 global suppliers of lithium-ion batteries. ATL lithium batteries are used for consumer electronics, transportation and grid connected energy storage from as small as smart watch battery to multi-megawatt hour installations. Founded in 1999, ATLs headquarters are in Hong Kong with multiple design and manufacturing locations throughout China.
To learn more about SolarBOS or submit a request for quote, please visit www.solarbos.com or contact us at 925.456.7744 or sales@solarbos.com.
Featured Product
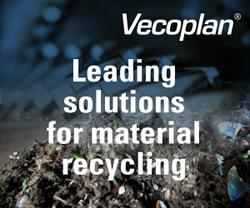
Vecoplan - Planning and implementation of complete processing plants in refuse derived fuel production
In order to reduce the costs involved in the energy-intensive production of cement, many manufacturers are turning to refuse-derived fuels (RDF), considerably reducing the proportion of expensive primary fuels they would normally use. Solid fuels are being increasingly used - these might be used tyres, waste wood or mixtures of plastics, paper, composite materials and textiles. Vecoplan provides operators of cement plants with proven and robust components for conveying the material and separating iron and impurities, efficient receiving stations, storage systems and, of course, efficient shredders for an output in various qualities.