Carbon footprint verification demonstrates WINAICO as one of the cleanest solar module producer in the world
Bureau Veritas Certification's recent carbon footprint verification on WINAICO's WST-P6 shows WINAICO's manufacturing processes only contribute to 3.86% of the products' total Greenhouse Gas emission, proving WINAICO as one of the cleanest solar module producer in the world
WINAICO, Taiwans largest PV module brand, receives the carbon footprint verification on the WST-P6 module production by Bureau Veritas Certification. In order to determine Greenhouse Gas (GHG) emission of WINAICOs WST-P6 product series, assessments were conducted across all WINAICO facilities and suppliers in accordance to ISO/TS 14067:2013. The result positions WINAICO as one of the cleanest manufacturers in the industry.
The contribution of raw materials is shown as Resource Extraction and found to be responsible for 94.16% of all GHG emission. The manufacturing operations and facilities have been assessed to contribute only 3.86%. This positions WINAICO as one of the cleanest manufacturer in the module manufacturing industry. To put it into perspective, the total energy payback period to offset 100% of GHG emission measured is <1.5 years for modules installed in most places across Australia (based on emission factors of grid electricity from 2008). Similarly, energy payback period is approximately 1-3 years across other major solar markets of the world (based on emission factor data from 2011).
"It is WINAICOs mission to deliver the cleanest form of energy to the market", said Davis Chen, Chairman and CEO of WINAICO. "The carbon footprint assessment shows WINAICOs manufacturing processes only contribute to 3.86% of WST-P6 modules Greenhouse Gas emission volume. It is further proof that WINAICO is one of the cleanest solar module manufacturers in the world."
Featured Product
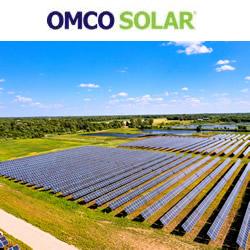