Sono-Tek Announces the Company’s 300th Ultrasonic Spray System sold for Fuel Cell and H2 Electrolyzer Coating Applications
Sono-Tek marks the recent sale of its 300th ultrasonic coating system for manufacturing fuel cells and electrolyzers. The machine sale was a large platform electrolyzer coating system, directed at converting environmentally harmful CO2 emissions into a useable fuel source. Back in 2008 when Sono-Tek first started tracking this industry, the market was just emerging, and its direction and growth potential were not well known. The Company quickly realized that the inherent benefits of its proprietary ultrasonic spray coatings provided significant advantages to fuel cell manufacturers in the development of Solid Oxide Fuel Cells ("SOFC"), Proton Exchange Membrane ("PEM") fuel cells, and electrolyzers.
Sono-Tek marks the recent sale of its 300th ultrasonic coating system for manufacturing fuel cells and electrolyzers. The machine sale was a large platform electrolyzer coating system, directed at converting environmentally harmful CO2 emissions into a useable fuel source.
Over the years, Sono-Tek's sales to this market have steadily increased, from new and repeat customers, as coating systems began to be developed for production scale manufacturing rather than primarily R&D.
The Company further leveraged its increasing knowledge and expertise with these coatings to further enhance their spray equipment capabilities specific to electrocatalyst spray applications, and expanded their offerings to what has become a full line of spray machines and configurations. Recent additions have been the ExactaCoat OP3 and VersiCoat conveyorized enclosure for continuous coating lines, with oversize options and expanded automation features. New features include Sono-Tek's DuraFlow pump for high flow continuous applications, PEM inverters, and active flow rate monitoring to help support the growing requirements for production fuel cell applications.
New developments to systems are identified from customer relationships, and developed developed in-house by the Company's highly skilled team of five applications engineers and 15 product engineers.
Sono-Tek's Director of Electronics and Advanced Energy division, Brian Booth, notes "It's been an exciting journey witnessing the transformation in the last 10+ years from working with mostly R&D systems, to the significantly more complex, high speed, and tailored solutions we see for both fuel cell and electrolyzers. Our technical team has excelled in satisfying customer challenges in scale up, and painting a bright picture for the future of Sono-Tek as a go-to in this industry."
"Although the pandemic has certainly had an impact across all industries, sales and innovation to the fuel cell/electrocatalyst industry have remained robust. We are proud to be part of the path to develop a growing hydrogen infrastructure where renewable energy from solar and wind can be converted into hydrogen fuel. Since our coating technology is used in both the supply and consumption of hydrogen, we are positioned to make a significant impact on a cleaner energy future. " says Bennett Bruntil, Sono-Tek's V.P. Sales and Marketing.
Featured Product
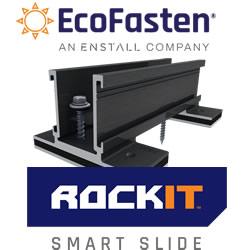