Varian Receives D.O.E. Grant to Develop Advanced Solar Cell Processing Technology
Varian Semiconductor Equipment Associates, Inc. recently secured a $4.8 million dollar grant from the D.O.E. under the Obama administration's "SunShot" program to develop U.S solar technologies. The goal of this project is to reduce the cost of manufacturing interdigitated back contact cells.
GLOUCESTER, MA, February 9, 2011 - Varian Semiconductor Equipment Associates, Inc. ("Varian") (NASDAQ: VSEA) has recently secured a $4.8 million dollar grant from the Department of Energy under the Obama administration's "SunShot" program to develop U.S solar technologies. The goal of this project is to reduce the cost of manufacturing interdigitated back contact cells - the most efficient silicon solar cells on the market.
Traditional solar cells have metal collectors on the front surface which lower their efficiency by blocking sunlight. Interdigitated Backside Contact (IBC) solar cells use metallic conductors on the back of the cell to collect the electricity generated by sunlight, which strikes the fully exposed front side of the cell.
IBC solar cells create more power per unit area because of their higher efficiency. These higher efficiency cells lower the module cost and the balance of system costs for the same power requirement. Also, higher efficiency cells increase the amount of power that can be generated within a fixed footprint, critical for applications where space is limited such as rooftops. Using traditional manufacturing processes, IBC cells are more expensive to manufacture. The higher cost of IBC cells, using traditional manufacturing processes, has slowed their implementation. Varian's proposed ion implant process enables cell makers to significantly reduce the cost of IBC cell manufacturing by reducing the number of process steps by 30% to 40%. This ion implant process will also reduce manufacturing variability, cell handling, cell breakage and manufacturing cycle time while increasing yield. IBC solar cells manufactured with ion implant will have much higher efficiencies and will cost less per watt than today's front-side contact technology.
Dr. Paul Sullivan, Varian's Vice President of Business Development stated, "We are pleased to be the recipient of this SunShot grant and to receive the only award focused on silicon cell technology and manufacturing. This award will support our development of technology to enable the manufacture of advanced high efficiency IBC cell structures with dramatically simplified processes that will ultimately enable the lowest manufacturing costs of solar panels."
Varian has pioneered the use of ion implant in cell manufacture. Solar revenues for 2011 are currently projected to be in the $20-30 million dollar range with strong upside potential. As has been reported this week, Varian's lead customer, Georgia-based Suniva, has manufactured 19% efficiency solar cells using implant.
Varian will have a booth at the upcoming 5th annual SNEC solar tradeshow in Shanghai, China. In conjunction with SNEC, Varian will present its third vTech Solar technical seminar at the Kerry Pudong Hotel in Shanghai.
About Varian Semiconductor
Varian Semiconductor Equipment Associates is the leading supplier of ion implant equipment to semiconductor manufacturers, enabling them to pack more, higher performing transistors into computer chips that are revolutionizing the electronics industry. Varian Semiconductor's products are used by chip manufacturers worldwide to produce high-performance semiconductor devices. Customers have made Varian Semiconductor the market leader in ion implant because of its architecturally superior products that lower their costs and improve their productivity. Varian Semiconductor operates globally and is headquartered in Gloucester, Massachusetts. More information can be found on Varian Semiconductor's web site at www.vsea.com.
Featured Product
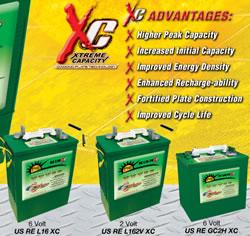