A New HVAC “Force” Cuts Energy, Boosts Efficiency
When it comes to building a sustainable energy future, there are two sides to the equation: generation and demand. While most of the attention has been placed on producing more clean power, there’s an equally powerful opportunity in reducing consumption—particularly in HVAC systems, which remain among the largest energy consumers on the planet.
Globally, HVAC systems consume approximately 14,000 terawatt-hours (TWh) of energy per year, accounting for 12% of worldwide final energy use. In the United States, HVACs’ share climbs even higher, to more than 13%, according to the U.S. Energy Information Administration (EIA). The climate impact is just as substantial: HVAC is responsible for an estimated 5 gigatons of CO₂ emissions annually, or more than 10% of global energy-related emissions.
With rising energy costs, growing grid volatility, and mounting pressure to meet aggressive sustainability goals, building operators are increasingly reevaluating the efficiency of their mechanical systems. While traditional upgrades have helped reduce energy use at the margins, a new wave of innovation is shifting the focus from “How can we use less power to operate cooling systems?” to a more fundamental question: “Is there a better way to cool altogether?”
A new approach to HVAC efficiency
One emerging technology may offer a compelling alternative. Developed by David Sattler, a mechanical engineer with more than 30 years of experience in thermodynamics and heat transfer, this green cooling system takes a fundamentally different approach. It eliminates many of the most energy-intensive components found in conventional HVAC systems and replaces them with a solution that operates using virtually no electricity.
Instead of relying on conventional condensers or chillers, the system applies a directed electromagnetic field—what Sattler refers to as a “force field”—to a pipe or plate within the HVAC system. This field facilitates heat transfer much like refrigerants in an air conditioner or water in a cooling tower, but at a significantly higher, even exponential rate.
“Right now, our goal is to make existing air conditioners dramatically more efficient by targeting their most wasteful components,” Sattler says.
In testing, the green A/C system achieved a Coefficient of Performance (COP) up to 10 times higher than conventional systems. For reference, a typical commercial air conditioning system might operate with a COP of 3 or 4. A COP of 40 represents a game-changing jump in efficiency.
A cool retrofit
Importantly, this is not a “rip-and-replace” solution. The system is designed to retrofit into existing HVAC infrastructure, providing a complementary cooling step that relieves pressure on compressors and improves overall system efficiency.
“We can replace the condenser altogether or simply add our system upstream to offload some of the thermal load,” Sattler explains. “Either way, it significantly reduces energy demands and lowers operating costs.”
The potential savings are substantial, especially for facility operators facing escalating utility bills. According to Sattler, integrating the system into an existing HVAC setup could reduce energy consumption by 50% or more, with a projected payback period of just three to five years.
For large commercial campuses or facilities where chillers and cooling towers dominate the energy profile – such as hospitals, universities, and data centers – the potential value is even greater. In hospitals, for example, where recirculated air is restricted in surgical suites, chilled water systems often run continuously. Reducing the load on those systems could mean millions of dollars in savings over the lifetime of the equipment.
At the macro level, the implications are hard to ignore. A 50% reduction in HVAC energy use in the U.S. alone would eliminate an estimated 1,350 TWh of annual demand – roughly equivalent to the power consumption of more than 100 million American homes. Globally, a similar reduction could free up around 7,000 TWh and cut CO₂ emissions by 2 to 3 gigatons per year—more than the entire annual carbon footprint of India.
“It is not just for cooling,” adds Sattler. “By reversing the polarity on our system, we can generate heat. So, you don’t need two machines. You just turn the switch, and you have a heat pump.”
No refrigerants. No pumps. No emissions
Another key benefit of the green HVAC system under development by Marstecs is that it requires no refrigerants. As the HVAC industry continues its decades-long shift away from harmful substances like R-22 and HFCs, refrigerant management remains both costly and complex. This technology bypasses that entirely.
“Refrigerants leak. Compressors fail. Fans draw power. These are all points of inefficiency and failure,” Sattler says. “By focusing on pure thermal transfer – no pumps, no pressure cycles – we eliminate many of the headaches facility teams deal with every day.”
The system operates using only milliwatts of energy to activate the heat transfer process, and because it does not rely on a closed electrical circuit or conventional mechanical systems, its electrical load is virtually undetectable. This feature further enhances building-wide energy efficiency and simplifies the path to meeting sustainability targets.
Cooling without compromise
While the current focus is squarely on retrofit applications, Sattler isn’t shy about the long-term potential. With further refinement, the same technology could eventually replace entire HVAC systems, eliminating compressors, condensers, and refrigerants altogether.
The team is currently building a new, full-scale system in New York with plans for independent third-party testing at institutions such as Texas A&M and other national laboratories. If the data holds, the implications could be significant: not just for green building design, but for how cooling is approached across the planet… and potentially beyond.
Sattler even hints at space-based applications, noting the system’s suitability for spacecraft, lunar habitats, or Martian colonies where power is limited and thermal control is mission-critical.
“The next great green energy revolution may not come from generating more power,” Sattler concludes. “It may come from requiring less of it in the first place.”
Greg Rankin is a Houston-based freelance writer with more than 20 years of experience writing for the HVACR, processing and mechanical engineering industries.
Comments (0)
This post does not have any comments. Be the first to leave a comment below.
Featured Product
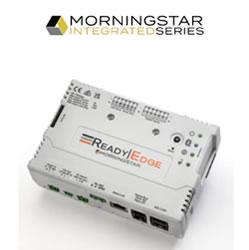