BTU International Receives Multiple-Unit Order for Tritan Metallization Firing System
Enhanced productivity and lower cost per watt from dual-lane Tritan systems
NORTH BILLERICA, Mass — Aug 24, 2010 — BTU International, a leading supplier of advanced thermal processing equipment for the alternative energy and electronics manufacturing markets, today announced the receipt of an order from a customer in Asia for multiple Tritan™ metallization firing systems. All of the units are scheduled to be shipped in the second half of this year.
"These dual-lane Tritan systems will greatly enhance our customers' productivity, allowing them to lower their cost per watt," said Jan-Paul van Maaren, Ph.D., vice president of marketing at BTU.
The Tritan metallization firing system, featuring BTU's exclusive TriSpeed™ technology, allows users to take advantage of superior ramp rates ― up to 200şC per second ― while not compromising the drying and cooling sections of the profile. The three-belt, three-speed system provides revolutionary control of profile development. In trials, Tritan has consistently shown an improvement in fill factor resulting in increased efficiency. This, combined with Tritan's low cost of ownership, enables our customers to achieve the lowest cost per watt.
About BTU International
BTU International (Nasdaq: BTUI) is a market-leading, global supplier of advanced thermal processing equipment to the alternative energy and electronics assembly markets. BTU's equipment and expertise are used in the manufacturing of solar cells and nuclear fuel as well as the production of printed circuit board assemblies and semiconductor packaging. BTU has design and manufacturing operations in North Billerica, Massachusetts and Shanghai, China with direct sales and service worldwide. Information about BTU International is available at www.btu.com.
###
Company Contact:
Jan-Paul van Maaren
Vice President Marketing
BTU International, Inc.
Phone: (978) 667-4111
Media Contact:
Megan Wendling
MW Associates
Phone: (239) 537-6001
Source: BTU International
Featured Product
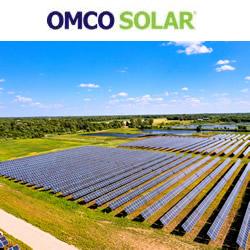
OMCO Origin® Factory-Direct Trackers
A One-In-Portrait (1P) solution for a wide range of solar projects within utility scale, distributed generation (DG), and community solar markets manufactured and factory preassembled in the USA at OMCO Solar with full-scale support, and design for quick, easy and safe installation, and fewer trackers per MW. OMCO makes all structural components with domestic steel and this balanced design allows for more accurate targeting and reduced energy consumption. OMCO Origin® Factory-Direct Trackers include universal module mounts with options for all commercially available modules, labor-saving bearings with 6 adjustable ways to compensate for posts and terrain issues, and foundation solutions for every terrain including OMCO C Piles.