Cooling Computers Saves Green For KKR And He Knows IT!!
KKR put SunGard Data Systems Inc. in Wayne, Pennsylvania, on a plan to lower energy use at 60 data centers in North America and Europe. Computers in these buildings process trading and financial data for banks and brokerages that manage $25 trillion of assets. They also produce three-quarters of the company's greenhouse gas emissions, says Ryan Whisnant, SunGard's director of sustainability.
Bloomberg Markets magazine.
KKR put SunGard Data Systems Inc. in Wayne, Pennsylvania, on a plan to lower energy use at 60 data centers in North America and Europe.
Computers in these buildings process trading and financial data for banks and brokerages that manage $25 trillion of assets. They also produce three-quarters of the company's greenhouse gas emissions, says Ryan Whisnant, SunGard's director of sustainability.
"In addition to powering the servers, the biggest energy use is cooling the data centers," Whisnant says.
Engineers configured the server cabinets to separate cold air that cools the servers from hot air the computers discharge. SunGard's financial system unit is consolidating 25 centers into just 5, for net savings of $5 million over 5 years and an annual reduction of almost 1,000 metric tons of CO2, Whisnant says.
Despite the improvements, SunGard's greenhouse gas emissions rose 6 percent in 2009 from a year earlier as business grew. It avoided $3.8 million in operating costs it would have paid had it not made the changes, KKR says on its website.
Reporting costs that a company avoided or CO2 that it would have emitted isn't the same as making actual reductions, says Kim Sheehan, a University of Oregon advertising professor and a founder of Greenwashing Index, which evaluates environmental claims. KKR may be touting more than it's delivering, she says.
I kind of agree with that assessment. It's not green to have just savings through attrition or if it is real cost to the environment..that's the question.
Featured Product
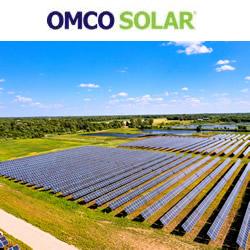
OMCO Origin® Factory-Direct Trackers
A One-In-Portrait (1P) solution for a wide range of solar projects within utility scale, distributed generation (DG), and community solar markets manufactured and factory preassembled in the USA at OMCO Solar with full-scale support, and design for quick, easy and safe installation, and fewer trackers per MW. OMCO makes all structural components with domestic steel and this balanced design allows for more accurate targeting and reduced energy consumption. OMCO Origin® Factory-Direct Trackers include universal module mounts with options for all commercially available modules, labor-saving bearings with 6 adjustable ways to compensate for posts and terrain issues, and foundation solutions for every terrain including OMCO C Piles.