ENDURANCE TESTS - Fronius inverters meet demanding quality requirements
Every day of the week, a team of experts puts Fronius inverters through a series of exhaustive tests to ensure the Austrian company's demanding quality requirements are met.
Fronius test procedures exceed those required by national and international regulations. The tests cover various aspects of product performance, such as analysing electrical properties, response on the mains, measuring efficiency and checking mechanical strength, e.g. for transport purposes. The performance of the inverters under demanding conditions is tested to see how they respond to environmental influences such as water, dust, salt or extreme temperatures.
Other tests determine how long the devices are able to comply with the requirements. These endurance tests take place under extreme conditions. Everything is thrown at the devices to ensure they can cope with every conceivable situation.
For example, if a unit is intended for outdoor installation, it needs to be resistant to water spray from every direction and must be protected against the ingress of foreign bodies. Depending on the device and the region, it must also be able to safely withstand temperatures ranging from -25°C to +55°C. "National and international regulations form the basis for our endurance tests. On top of this, we test against our own internal Fronius quality requirements, which have evolved with our experience over the years. The main reason for going above and beyond the regulatory requirements is to ensure we meet the highest possible quality requirements," explains Fronius quality and safety expert Bernhard Doppelbauer.
Each type of inverter undergoes continual testing, at the development stage, in pre-production series manufacture and immediately after leaving the production line. Fronius experts also perform 'out-of-box' audits on a daily basis. In this quality test, inverters are selected at random and subjected to exhaustive testing.
Featured Product
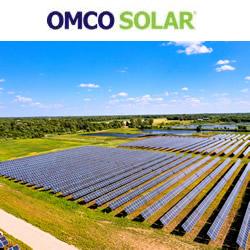