This Printer Spits Out 10 Meters of Solar Panel Every Minute
The printer system was developed by VICOSC, the Victorian Organic Solar Cell Consortium—a collaboration between the University of Melbourne, CSIRO Molecular and Health Technologies, and Monash University—and utilizes only existing printer technology to embed polymer solar cells (also known as organic or plastic solar cells) in thin sheets of plastic or steel at a rate of ten meters per minute. "We're using the same techniques that you would use if you were screen printing an image on to a T-Shirt," project coordinator and University of Melbourne researcher Dr David Jones said in a press release.
Organic solar cells rely on organic electronics, hydrocarbon molecules specifically, to generate a photovoltaic effect and convert the Sun's rays into usable DC current. The primary benefit to using organic cells is that these sheets can be printed in bulk for very little and the optical absorption coefficient of of the hydrocarbon molecules is so high that even small amounts of material can suck up a lot of light. On the other hand, organic cells are less efficient than their inorganic alternatives and tend to break down faster due to the chemical changes occurring within.
Currently, these organic sheets are able to produce up to 80W in the lab and between 10 and 50W under real world conditions. These cells aren't meant to replace conventional, inorganic panels, quite the opposite in fact. "The different types of cells capture light from different parts of the solar spectrum. So rather than being competing technologies, they are actually very complementary," said CSIRO materials scientist Dr Scott Watkins.
This printing technique could soon lead to buildings with PV laminated windows and exteriors and homes covered in solar shingles.
Comments (0)
This post does not have any comments. Be the first to leave a comment below.
Featured Product
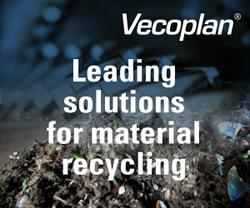