Soteria Forms Consortium to Promote New Architecture for Mass Production of Safe Lithium Ion Batteries
Soteria Battery Innovation Group is forming a consortium to make its new lithium battery architecture available to every battery manufacturer worldwide. By eliminating excess metal and thermally unstable components of the battery, the new architecture virtually eliminates the possibility of the self-ignition that has plagued lithium ion batteries in applications such as hoverboards, smart phones, electric vehicles and airplane battery systems.
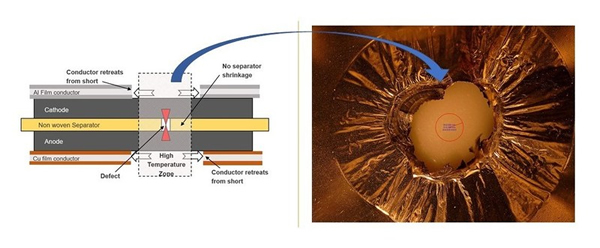
"This technology is too important for us to keep to ourselves and rely on our own capabilities to bring to market. Instead, we will allow broad access through the normal lithium ion and automotive supply chain," said Brian Morin, co-Founder and CEO of Soteria. The company is going to make the technology available through FRAND licenses to the best global advanced materials companies and promote the acceptance of the architecture through standards that cannot be met with legacy battery architectures.
Batteries made with this technology will be able to pass much more aggressive safety tests than legacy technology. In addition to surviving in more aggressive test conditions, the cells continue to function after damage. This can be especially important in transportation, where the minivan might need to get out of the intersection, the plane to the ground, or the boat to shore ahead of a storm. In addition, the technology can be adopted in existing lithium ion battery plants without significant capital expense.
The technology has two components, each of which will provide reduced weight, improved safety and reduced manufacturing cost. The first is a current collector made from metallized film, eliminating over 90% of the metal in the battery. The lower metal content reduces cost and weight and is unable to carry large current densities associated with ignition events due to internal short circuits, acting like an internal fuse. The second component, a thermally stable separator, is lighter, less expensive to manufacture and much more stable than existing ceramic coated separators. Because these separators never melt or shrink, it becomes impossible for a small manufacturing defect to grow into a large internal short.
Founding members of the consortium include some of the world's foremost advanced material, equipment, lithium ion battery, automotive and electronics companies. The consortium has an open membership policy, and free memberships are available to lithium ion battery manufacturers and to companies that manufacture devices using lithium ion batteries.
About Soteria Battery Innovation Group Inc
Soteria Battery Innovation Group Inc is an advanced technology development and licensing company that has formed a consortium to promote a light, safe and cost-effective architecture for lithium ion batteries. Soteria BIG was founded in 2017 by Brian Morin and Carl Hu, and is headquartered in Greenville, SC. For more information contact Vik Pearce at (864) 609-4165 or Vik.Pearce@SoteriaBIG.com or visit our website at www.soteriabig.com.
Comments (0)
This post does not have any comments. Be the first to leave a comment below.
Featured Product
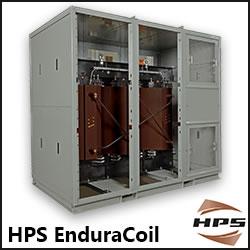