This presentation focuses on systematically highlighting the ways to optimize waste-to-energy plants in terms of their energy efficiency as an indicator of the positive effect with regard to climate control. Potentials for increasing energy efficiency are identified and grouped into categories.
India Sustainable Communities Proposal
Dr. S. Roy and Dr H. Guevara for | NuEnergy Technologies
India represents a unique environment and culture ready to rise as leaders for economic growth from in the Renewable Energy sector. This presentation is a proposal from NuEnergy technologies, world leaders in Renewable Energy Technologies. We will present Sustainable Renewable Energy Solutions for impoverished Indian Communities looking for an increase in sustainable energy and natural resources, such as clean water. In the past few decades, energy needs have increased dramatically. NuEnergy would like to show India how to stand as Global leaders for Sustainable Communities and Environmentally Sound Renewable Energy Solutions. This presentation focuses on systematically highlighting the ways to optimize waste-to-energy plants in terms of their energy efficiency as an indicator of the positive effect with regard to climate control. Potentials for increasing energy efficiency are identified and grouped into categories.
The description is based on a model that comprises all relevant processes from the collection and transportation up to the thermal treatment of waste.
Organic waste deposited in a landfill will decompose over times and release a mixture of gasses into the atmosphere. In addition to the environmental blight of a landfill, the release of these gasses provides no benefit to anyone and some gasses such as methane and carbon dioxide, are greenhouse gasses considered harmful to the environment.
NuEnergy Technologies
The NuEnergy Technology Alliance offers Sustainable, Pollution Free Fuel Processing Solutions that will have a profound, life changing affect on how future renewable bio-energy will be generated, harvested, processed managed and distributed by Agribusiness Worldwide.
The financial and environmental costs associated with the traditional waste management process of collecting waste for deposit in a landfill are significant. Hauling waste to a landfill is expensive, produces vehicle emissions that degrade air quality and contributes to traffic congestion.
Once at the landfill, the waste decomposes, releasing greenhouse gases. Utilizing available and proven technology to recover energy from organic waste avoids many of these costs. Processed properly, organic waste becomes a resource and a waste-to-energy (WTE) power plant becomes a clean, reliable source of renewable energy.
A WTE project is more than forcing a “one-size-fits-all” technology onto a community. There are considerations beyond the technology that are equally important; these projects often represent a dramatic shift in city or regional waste management and energy planning. NuEnergy’s first step in project development is coordinating with the local community and conducting a feasibility study to identify local conditions, including waste stream characteristics, other available renewable energy resources and unique local issues that need to be addressed. The result will be a project that delivers the best value to the community.
All technologies put the waste into a chamber that is essentially an organic waste pressure cooker. While gasifiers are all different in some way, using multiple chambers or processing waste at differing combinations of time, temperature and pressure, all essentially perform the same function – the conversion of organic waste into syngas. Gasification is not incineration; the oxygen content is controlled during the process to ensure that the waste is never combusted or burned.
Understanding Gassification
Gassification is a process where the natural conditions of decompositions are controlled and accelerated, with gasses being captured and put to a beneficial use. Waste processing technologies are applied worldwide to generate steam, power, fuels, and chemicals. Mass burn and refuse-derived fuel combustion are the most commonly applied thermal technologies for conversion of waste materials. Gasification and pyrolysis, while considered established technologies with respect to feedstock other than MSW, are considered emerging technologies with respect to MSW.
In the U.S., there are 147 companies offering gasification technologies in different stages of development worldwide, most of which market in the U.S. through licensees. In the U.S., currently 21 companies have more than 21 total pilot and demonstration facilities.1
These technologies are sometimes are known as Advanced Thermal Technologies or Alternative Conversion Technologies. They typically rely on carbon-based waste such as paper, petroleum-based wastes like plastics, and organic materials such as food scraps. The waste is broken down to create gas, solid and liquid residues. The gases can then be combusted in a secondary process. The pyrolysis process thermally degrades waste in the absence of air (and oxygen). Gasification is a process in which materials are exposed to some oxygen, but not enough to allow combustion to occur. The high BTU value of non-recycled MSW makes them attractive feedstock components for gasification processes. Gasification is attractive because of the versatility of its final marketable products such as steam, electricity, ethanol and other chemicals. The use of solid waste as a feedstock and close association with mass burn technologies have led to gasification plants being regulated as waste-to-energy facilities. Facility development is challenged by public acceptance, perceived risk.
Temperatures are usually above 750oC. In some systems the pyrolysis phase is followed by a second gasification stage, in order that more of the energy carrying gases are liberated from the waste. The main product of gasification and pyrolysis is syngas, which is composed mainly of carbon monoxide and hydrogen (85 per cent), with smaller quantities of carbon dioxide, nitrogen, methane and various other hydrocarbon gases. Syngas has a calorific value, so it can be used as a fuel to generate electricity or steam or as a basic chemical feedstock in the petrochemical and refining industries. The calorific value of this syngas will depend upon the composition of the input waste to the gasifier.
Comparing Mass-Burn Incineration and Gasification
Gasification technology offers the important ability to take a wide range of feedstocks and process them into syngas. By using less oxygen, fewer air emissions may be produced. The plants are modular. They are made up of small units which can be added to. They are quicker to build. The processes are claimed to produce a more useful product than standard incineration – gases, oils and solid char can be used as a fuel, or purified and used as a feedstock for petro-chemicals and other applications.
The syngas may be used to generate energy more efficiently, if a gas engine is used whilst incineration can only generate energy less efficiently via steam turbines. The energy produced may be eligible for more Renewables Obligation Certificates (ROCs) than incineration, increasing the potential income from any power generated.2 3
Biomass Fuels
To reduce emissions of greenhouse gases such as carbon dioxide (CO2), boilers for heat and power production will be operated with increasingly high shares of biomass. Earlier, the size of the biomass fired plants has been limited for the locally available biomass fuel sources. Today the biomass market has changed from Local to Global. The green tariffs provided by most countries in the EU are making it possible to procure biomass globally using large biomass resources in America and Asia. This has created an interest for the large scale biomass fired units. To date, biomass combustion systems use mainly forest industry biomass resources such as wood and wood residues. As the demand for biomass fuels grows and the price for wood-based biomass fuels increases, there is a growing interest to utilize not only wood-based fuels but also agricultural biomass, biomass residues and biomass wastes as fuel. The quality of biomass fuels vary considerably due to fuel supply, preparation and processing, as well as local conditions such as soil chemistry, rainfall, and farming practices.
If biomass fuel is compared with fossil fuels, the most important differences can be found in the variability of fuel characteristics, low energy density, higher moisture contents and low nitrogen and Sulphur contents of biomass fuels. Ash content is low but ash has a low melting temperature. The main constituents of ash are alkali and earth alkali elements and additionally Phosphorous in agro biomass. The moisture content of biomass has a large influence on the combustion process and on the resulting efficiencies.
Agricultural and field crop residues including straw, shells and hulls are identified as the most problematic fuels having the strongest potential to create operational difficulties, such as agglomeration of fluidized bed, fouling and corrosion of the convective heat surfaces. Such high potential is not only dependent on the ash content of fuels, since the ash in biomass fuels is frequently low. Agro biomasses contain elevated concentrations of alkali, phosphorous and chlorine compounds, which produce low melting eutectics during combustion. The concentrations of these elements tend to be at the upper range of typical fuel specifications for biomass fuels, and are higher than commonly used in wood-fired boilers. The unfavourable composition of the ash is the main reason why so far the utilization of novel biomass fuels has been limited in energy production. Most gasification and pyrolysis processes have four stages:
Preparation of Refused-Derived Fuel
Refuse-derived fuel (RDF) differs from mass burn because the incoming waste is processed before combustion to improve fuel performance. First, recyclable and non-combustible materials are removed from the MSW and the refuse material is shredded, dried and/or compacted into pellets or cubes, to produce a more homogenous fuel. RDF can be used as a fuel in either a dedicated or an existing boiler, alone or with other fuels. Depending on the degree of processing, RDF is considered a manufactured fuel. The feedstock may be in the form of a refuse derived fuel, produced by a Mechanical Biological Treatment plant or an autoclave. Alternatively, the plant may take mixed waste and process it first through some sort of materials recycling facility, to remove some recyclables and materials that have no calorific value.
SRF Bail
World Gasification Capacity and Planned Growth by Feedstock 4
The U.S. Department of Energy’s (DOE) 2010 Worldwide Gasification Database shows that the current gasification capacity has grown to 70,817 megawatts thermal (MWth) of syngas output at 144 operating plants with a total of 412 gasifiers. The database also shows that 11 plants, with 17 gasifiers, are presently under construction, and an additional 37 plants, with 76 gasifiers, are in the planning stages to become operational between 2011 and 2016. The majority of these plants—40 of 48—will use coal as the feedstock . The additional planned capacity from all new 2011–2016 plants is 51,288 MWth, an increase of more than 72%. If this growth is realized, worldwide capacity by 2016 will be 122,106 MWth of syngas capacity, from 192 plants and 505 gasifiers regional Distribution.
Gasification plants are now operating in 29 countries. The Asia/Australia region has 37% of the total operating capacity. The Africa/ Middle East region has strengthened its second position, due to the rapid growth in Qatar. Of the 10,857 MWth syngas capacity that is presently under construction, 65% is being built in the Asia/Australia region, 18% in Europe, and 17% in North America. With 63% of total planned capacity growth, North America has the potential to lead the world’s regional growth through 2016. Another 34% will originate from the Asia/Australia region, with China leading this increase.
World Gasification Capacity Planned Growth 5
Gasification
Syngas can be processed to chemicals such as methanol and hydrogen. Methanol can be further transformed to different fuels or chemicals including ethanol, acetic acid, formaldehyde, methyl acetate, commonly used in industrial and commercial processes. Figure 5 shows a variety of chemical pathways and outputs for processing of the syngas.
Simplified F-T Synthesis-Based Reduction Scheme
Catalysts
Catalysts play a pivotal role in syngas conversion reactions. The basic concept of a catalytic reaction is that reactants adsorb onto the catalyst surface, rearrange, and combine into products that then desorb from the catalyst surface.
It has been found that the breaking of the CO bond is the rate-determining step for relatively unreactive catalysts such as Ni and that this reaction step proceeds via bond-breaking of the C-OH intermediate yielding adsorbed C and OH on the surface. On the more reactive metals, like Fe, this reaction step becomes fast, and the surface becomes poisoned by adsorbed carbon and oxygen. A good methanation catalyst therefore has a compromise between low CO dissociation barriers and a high carbon (in terms of CH4) and oxygen (in terms of H2O) desorption rate.
Among these catalysts, it is generally known that:
-
Nickel (Ni) tends to promote methane formation, as in a methanation process; thus generally it is not desirable
-
Iron (Fe) is relatively low cost and has a higher water-gas-shift activity, and is therefore more suitable for a lower hydrogen/carbon monoxide ratio (H2/CO) syngas such as those derived from coal gasification
-
Cobalt (Co) is more active, and generally preferred over ruthenium (Ru) because of the prohibitively high cost of Ru
In comparison to iron, Co has much less water-gas-shift activity, and is much more costly.
Given these constraints, commercially available F-T catalysts are either cobalt or iron based. In addition to the active metal, the Fe catalysts at least typically contain a number of promoters, including potassium and copper, as well as high surface area binders/supports such as silica and/or alumina.
Only iron-based F-T catalysts are currently used commercially for converting coal-derived syngas into F-T liquids, given Fe catalyst's inherent water gas shift capability to increase the H2/CO ratio of coal-derived syngas, thereby improving hydrocarbon product yields in the F-T synthesis. Fe catalysts may be operated in both high-temperature regime (300-350°C) and low-temperature regime (220-270°C), whereas Co catalysts are only used in the low-temperature range. This is a consequence of higher temperatures causing more CH4 formation, which is worse for Co compared to Fe. 6
F-T Reactors
The Fischer-Tropsch reaction is highly exothermic; therefore heat removal is an important factor in the design of a commercial reactor. In general, three different types of reactor design might be used for F-T synthesis:
-
Fixed bed reactor
-
Fluidized bed reactor
-
Slurry bed reactor
All three types of reactors are in use commercially. The multi-tubular fixed-bed reactors, known as Arge reactors, were developed jointly by Lurgi and Ruhrchemie and commissioned in the 1955. They were used by Sasol to produce heavy F-T liquid hydrocarbons and waxes in Sasolburg, in what Sasol called it now their Low-Temperature F-T Synthesis Process, aiming for liquid fuels production. Most, if not all, of these types of Arge reactors are now be replaced by slurry-bed reactors, which is considered the state-of-the-art technology for low temperature F-T synthesis. Slurry-bed F-T reactors offer better temperature control and higher conversion. Slurry-bed F-T reactors are also being developed by other Fischer-Tropsch technology vendors, namely Exxon and Shell.
Fluidized-bed F-T reactors were developed for high temperature F-T synthesis to produce low molecular gaseous hydrocarbons and gasoline. It was originally developed in a circulating mode, e.g., Sasol's Synthol reactors, and they have since been replaced by a fixed fluidized bed type of design called Advanced Synthol reactors. These types of reactors have high throughputs. 7
This process is highly relevant to aviation fuels, where the high energy density requirements of efficient flight restrict the energy storage options available to aircraft. Weight is a major aircraft design consideration. As such, once natural petroleum reserves are exhausted, synthetic fuel will likely become the only viable aviation fuel due to its high energy density, unlike the automobile industry, which can use heavier battery technology as weight and energy density is not a crucial design factor.
The issue of Fischer-Tropsch sustainability comes into play when one envisions a world depleted of its natural petroleum reserves. In this world, electrical energy can still be generated via non-carbon based sources (e.g. nuclear, hydro, wind, solar, etc.) which can be used to power the Fischer-Tropsch plants as well as the gasification or steam reforming processes. The major consumable of the process then becomes the starting carbon sources, also known as feedstock. Therefore, provided that energy is available to power the process, the sustainability of synthetic fuel production through Fischer-Tropsch rests on the availability of feedstock.
Fixed Bed Reactors
A Continuous Feed Fixed Bed Reactor Uses Two Catalyst Bed
In a mixed-bed reactor the catalyst pellets are held in place and do not move with respect to a fixed reference frame. Material and energy balances are required for both the fluid, which occupies the interstitial region between catalyst particles, and the catalyst particles, in which the reactions occur.
Fixed-bed reactors have long been used in process industries. They contain catalyst, typically in pellet form, packed in a static bed. The syngas is then passed through the bed, where the reactions are induced as the gases contact the catalyst. Originally, fixed-bed reactors were the only commercially viable reactor type due to technological limitations. However, they also presented drawbacks mainly in the constraints existing in access to the catalyst material. Since the gas has to pass over the material the reaction is limited by the available surface area. This problem can be reduced by allowing more than one "bed" in the reactor for the gas to pass over, under, and/or through. The catalysts in fixed-bed reactors do not need to be as resilient, as they do not move in the bed. For the common situation encountered when a reaction process is exothermic, fixed-bed reactors demand cooling of the bed. If the excess heat is not dissipated from the reactor bed, it could eventually lead to deterioration and deactivation of the catalyst material. Fixed-bed reactors can be equipped with internal tubes where a heat transfer fluid, such as boiler feed water, can circulate inside the tubes to control the temperature rise in the reactor. 8
Fluidised Bed Reactors
In a fluidized-bed reactor, the substrate is passed upward through the immobilized enzyme bed at a high enough velocity to lift the particles. However, the velocity must not be so high that the enzymes are swept away from the reactor entirely
Fluidized-bed reactors solve some of the problems that are present in fixed-bed reactors. They allow for a better access to catalyst material since the catalyst particles are thoroughly mixed with the gas or fluid, allowing for the greatest possible surface area for reactions to take place. Heating issues are also helped due to the improved heat transfer resulting from the inherent characteristics of the fluidized state of the catalyst bed. This also includes reducing the potential for heat gradient build ups that can occur when the catalyst is immobile as in a fixed-bed. Fluidized-bed reactors can operate almost isothermally. They can also have internal tubes through which heat transfer fluids can be circulated to remove excess heat.
Fluidised-Bed Reactor
In fluidized-bed reactors, catalysts can be removed on line for regeneration or replacement without shutting down the reactor. A fixed-bed reactor must be shutdown to regenerate the catalyst or add new catalyst. Today fluidized bed reactors are used to produce gasoline and other fuels, along with many other chemicals. Circulating Fluidized Bed technology is an ideal technology to be used for large scale power generation with a broad variety of biomass fuels. The well-known benefits of CFB technology, such as the superior fuel flexibility, inherently low emissions and high availability can be fully utilized for this purpose. Today the biomass fired CFB technology offers a high efficiency boiler scale-up to 300MWe and fuel flexibility from clean biomass to RDF.
Slurry Bed Reactor
Slurry Bed Reactor
The diagram above shows the synthesis of methanol in a slurry batch reactor. Syngas enters at the bottom of the reactor into heated mineral oil. The gas then reacts with the assistance of suspended catalyst to form the methanol product. Unreacted gas and methanol vapour exit though the top of the reactor. Once out of the reactor, the methanol is condensed to a liquid.
Benefits of Slurry Bed Reactors
-
Good temperature control.
-
Good heat recovery.
-
Constant overall catalytic activity maintained easily by addition of small amount of catalyst.
-
Useful for catalysts that cannot be pelletized.
-
Large heat capacity of reactor acts as a safety feature against explosions.
The reacting feed gas (mixed with recycle) is introduced through spar gears. It bubbles through the column keeping the catalyst in suspension, aerating the liquid and supplying the agitation necessary for mass transfer as it reacts. Because the reaction in question is highly exothermic, cooling coils are provided in the reactor zone containing the liquid phase with cooling medium normally in the form of steam generation.
In a mixed-bed reactor the catalyst pellets are held in place and do not move with respect to a fixed reference frame. Material and energy balances are required for both the fluid, which occupies the interstitial region between catalyst particles, and the catalyst particles, in which the reactions occur.
Fixed-bed reactors have long been used in process industries. They contain catalyst, typically in pellet form, packed in a static bed. The syngas is then passed through the bed, where the reactions are induced as the gases contact the catalyst. Originally, fixed-bed reactors were the only commercially viable reactor type due to technological limitations. However, they also presented drawbacks mainly in the constraints existing in access to the catalyst material. Since the gas has to pass over the material the reaction is limited by the available surface area. This problem can be reduced by allowing more than one "bed" in the reactor for the gas to pass over, under, and/or through. The catalysts in fixed-bed reactors do not need to be as resilient, as they do not move in the bed. For the common situation encountered when a reaction process is exothermic, fixed-bed reactors demand cooling of the bed. If the excess heat is not dissipated from the reactor bed, it could eventually lead to deterioration and deactivation of the catalyst material. Fixed-bed reactors can be equipped with internal tubes where a heat transfer fluid, such as boiler feed water, can circulate inside the tubes to control the temperature rise in the reactor.
Slurry Bed Reactor
The diagram above shows the synthesis of methanol in a slurry batch reactor. Syngas enters at the bottom of the reactor into heated mineral oil. The gas then reacts with the assistance of suspended catalyst to form the methanol product. Unreacted gas and methanol vapour exit though the top of the reactor. Once out of the reactor, the methanol is condensed to a liquid. 8
- Benefits of Slurry Bed Reactors.
- Good temperature control.
- Good heat recovery.
- Constant overall catalytic activity maintained easily by addition of small amount of catalyst.
- Useful for catalysts that can't be pelletized.
- Large heat capacity of reactor acts as a safety feature against explosions.
The reacting feed gas (mixed with recycle) is introduced through spar gears. It bubbles through the column keeping the catalyst in suspension, aerating the liquid and supplying the agitation necessary for mass transfer as it reacts. Because the reaction in question is highly exothermic, cooling coils are provided in the reactor zone containing the liquid phase with cooling medium normally in the form of steam generation.
Over Generation
Organic waste deposited in a landfill decomposes over time, releasing a mixture of greenhouse gases into the atmosphere. Gasification controls and accelerates the natural decomposition process to create synthesis gas (syngas), which is used to generate power. This technology is not new; in the mid-1800’s many large cities used gasification to produce the gas used for street lighting.
All technologies that convert waste-to-energy involve the same basic steps.
WTE Plant
Waste pre-processing: Waste is delivered to the facility and processed for the delivery to the gasifier.
Conveyance: Systems will generally include some sort of conveyor to move the pre- processed waste to the gasifier.
Gasifier: All technologies put the waste into a chamber that is essentially an organic waste pressure cooker. While gasifiers are all different in some way, using multiple chambers or processing waste at differing combinations of time, temperature and pressure, all essentially perform the same function – the conversion of organic waste into syngas. Gasification is not incineration; the oxygen content is controlled during the process to ensure that the waste is never combusted or burned.
Steam & Power Creation: Syngas moves from the gasifier to a boiler where the syngas is combusted, with heat creating steam that powers turbines to generate power.
Treatment of Flue Gas: Any flue gas is treated so that system emissions meet all applicable air quality systems.
There is off the shelf, proven equipment to handle each of the steps described above. Because gasifier performance is dependent upon the facility feedstock, technology selection cannot be determined until a number of project parameters are established.
The facility design developed by the NuEnergy project team will incorporate the most appropriate, proven, cost effective technology solution available and capable of providing the maximum benefits to the local community and the global environment.
NuEnergy Technologies, as an Engineering Systems Integrator, can provide the optimized type of Waste to Energy (WTE) System needed at your facility. This could be a Biodiesel, Main Stream Waste (refuse), Industrial Waste, Coal Gasification, or any other type feedstock gasification system. Our integrated plasma systems are very hot plasma, essentially ionized gas, such as oxygen, under normal pressure created by an electrical arc. The power of plasma is the very high temperature it can reach, ranging from 2 to 6 thousand degrees Celsius. Required minimal dissociation temperature of organic molecules is in the range of 1500 degrees Celsius, which is close to melting temperature of metals. At these extremely high temperatures, all waste constituents, including metals, toxic materials, silicon, etc. are completely melted, forming non–toxic dross. Treating municipal waste with plasma or our other type of gasification systems does not produce foul odors or a harmful ash, something all too common in the traditional incinerating plant. Plastic, biological and chemical compounds, as well as toxic gases, decompose into simpler gases, while the regained metals from this process can be safely returned to metallurgic industry or combined in the Geopolymer formula, and can be used as an additive to road and construction materials. We have the technology and funding available for these technologies and the complete elimination of liquid waste such as certain oil based liquid waste, leachates, heavy sludge, municipal wastewater, and heavy manure via its recirculation through the arc chamber until all liquid molecules are separated into irrigation water, while the solids are converted into usable synthetic fuels, heat and carbon residues. 9
Gasification System
Conclusions
The NuEnergy Products Division develops and manufactures sustainable energy systems. We have an extensive portfolio of innovative and complementary renewable energy technologies that, either individually or collectively, provide a wide range of power solutions. Our Consulting Services Division provides a broad range of "green energy" consulting services, grant writing, and feasibility studies to business and government entities exploring the application of renewable energy technologies to their operations. Additionally, NuEnergy offers systems integration and value-added engineering services in a variety of situations.
The NuEnergy Project Management Division participates in project development from a complete "design, build, own and operate" mode to acting as the project manager for third-party developers. Project development is more than technology selection and engineering. It involves working closely with the local community to build a facility that achieves project goals in a way that is fair to the community. Activities include technology and site selection, coordination of all engineering activities, permitting, licensing, supply chain management, local community outreach, employee training and facility maintenance. Most projects are planned to include a reinvestment of a portion of project cash flow back into the local community.
References
-
www.foe.co.uk/resource/briefings/mchnical_biolo_treatmnt.pdf (Briefing Report sept2009
-
Defra (2007), Advanced thermal treatment of municipal solid waste www.defra.gov.uk/environment/waste/wip/newtech/pdf/att.pdf
-
Mark Crocker, ed., Thermochemical Conversion of Biomass to Fuels and Chemicals, (2010) Royal Society of Chemistry
-
Short history and present trends of Fischer–Tropsch synthesis in Applied Catalysis A: General (Vol. 186), Elsevier Publication
The content & opinions in this article are the author’s and do not necessarily represent the views of AltEnergyMag
Comments (0)
This post does not have any comments. Be the first to leave a comment below.
Featured Product
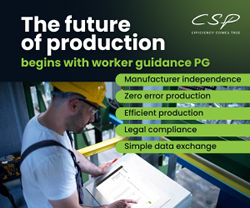