The chemical looping process refers to the use of a metal oxide material to take oxygen from air (and water, and/or CO2), and supply that oxygen to a fossil fuel and/or biomass. Using the chemical looping concept, one can make many products such as electricity, liquid fuels,
From Fossil Fuel To Electricity Without CO2: Ohio State University Makes It Possible
L.-S. Fan | Ohio State University
How did your research originate?
I have been working on efficient, clean fossil fuel conversion processes for the last 40 years. The chemical looping technology work evolved from our development of the calcium-based sorbent technology in the 1980’s for removal of pollutants from the coal combustion flue gas stream, such as sulfur and heavy metals like selenium and arsenic. The work on calcium-based sorbent technology then extended to include the capture of CO2, establishing the calcium looping technology. The calcium looping technology further expanded to incorporate the use of a more elaborate metal-oxide materials that could perform reduction and oxidation reactions and be applied to many different fossil fuel conversion systems. This extension led to our current focused work on the iron-based chemical looping platform technology.
Could you elaborate on this “chemical looping” process?
The chemical looping process refers to the use of a metal oxide material to take oxygen from air (and water, and/or CO2), and supply that oxygen to a fossil fuel and/or biomass. Using the chemical looping concept, one can make many products such as electricity, liquid fuels, and other chemicals. When applied to the coal to electricity process, chemical looping can produce electricity while efficiently capturing the majority of the CO2 produced, resulting in low electricity costs, making it one of the most advanced approaches to clean coal. Chemical looping can also be applied to make chemicals from shale gas or biomass in a highly efficient manner. High efficiency means more of the carbon present in the fossil fuel or biomass is transformed to a chemical product, reducing the amount of carbon that is emitted as a pollutant.
The OSU chemical looping process can be designed to be so efficient that it can take CO2 emitted from other sources and transform it to a desired or salable chemical product. Operating the system in this manner results in a CO2 negative process system. Another major development of the technology at OSU includes the creation of a chemical looping particle capable of sustaining thousands of cycles without loss in reactivity and strength. This major success in the sustainable metal oxide particle development renders the chemical looping technology commercially realizable.
Are there plans to partner with more companies?
We are already in collaboration with Linde Group and Babcock & Wilcox for different chemical looping process applications. Collaboration with other firms in producing valuable products is also in progress.
After this recent breakthrough, what’s next?
The recent breakthrough has made it clear that sustaining reactivity and strengths of metal oxide materials under commercially relevant reaction conditions and timescales are feasible. The use of metal oxides for providing oxygen offers several economic advantages over conventional systems by eliminating the need for cryogenic air separation unit. The gaseous feedstock based chemical looping technology is well on its way to commercialization. Future focus will be on coal based technology which will require continued development.
Can you predict a timeline for the future development of this process?
There will be no technology challenges anticipated for syngas and hydrogen production from gaseous feedstock at the present time. It will take however more years (10-15 years) to commercialize coal based chemical looping technology.
About L.-S. Fan
L.-S. Fan is Distinguished University Professor and C. John Easton Professor in Engineering in the Department of Chemical and Biomolecular Engineering at The Ohio State University. He has been on the faculty of Chemical Engineering at Ohio State since 1978 and served as Department Chair from 1994 – 2003. Professor Fan received his B.S. (1970) from National Taiwan University, and his M.S. (1973) and Ph.D. (1975) from West Virginia University, all in Chemical Engineering. In addition, he earned an M.S. (1978) in Statistics from Kansas State University.
Professor Fan’s expertise is in fluidization and multiphase flow, powder technology and energy and environmental reaction engineering. He is an inventor of 7 industrially viable clean fossil conversion processes: OSCAR, CARBONOX, PH Swing, CCR, Calcium Looping, Syngas and Coal-Direct Chemical Looping Processes. These processes control sulfur, nitrogen oxide and carbon dioxide emissions and convert carbonaceous fuels to hydrogen, electricity or liquid fuels. He also invented the electrical capacitance volume tomography for 3-dimensional, real time multiphase flow imaging that is currently being used in academia and industry. Professor Fan is the Editor-in-Chief of Powder Technology and has served as a consulting editor of ten other journals and book series, including the AIChE Journal, I&EC Research, and the International Journal of Multiphase Flow. He has authored or co-authored five books, 420 journal papers, and 55 patents.
Professor Fan has received a number of awards in recognition of his research and teaching including the ACS E. V. Murphree Award, the AIChE Alpha Chi Sigma, R. H. Wilhelm, and 67th Institute Lectureship Awards, the ASEE Dow Lectureship, the CCR Malcolm Pruitt Award, the R&D 100 Award, International Fluidization Achievement Award, and The Ohio State University Charles E. MacQuigg Award for Outstanding Teaching and Joseph Sullivant Medal for Distinguished Teaching, Research and Service. He is a Fellow of the American Association for the Advancement of Science (AAAS) and the AIChE, as well as a Member of the U. S. National Academy of Engineering, the Chinese Academy of Engineering, the Australia Academy of Technology Science and Engineering (ATSE), the Mexican Academy of Sciences, and the Academia Sinica. Professor Fan was named in 2008 as one of the “One Hundred Engineers of the Modern Era” by the AIChE.
The content & opinions in this article are the author’s and do not necessarily represent the views of AltEnergyMag
Comments (0)
This post does not have any comments. Be the first to leave a comment below.
Featured Product
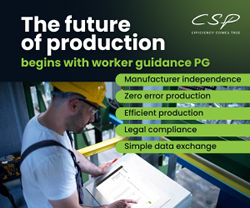