Researchers in the industry are working to develop better turbine technology, such as higher efficiency generators and more reliable blades to minimize energy and manufacturing costs.
Trending Developments in Wind Turbine Technology and the Future of Wind Energy
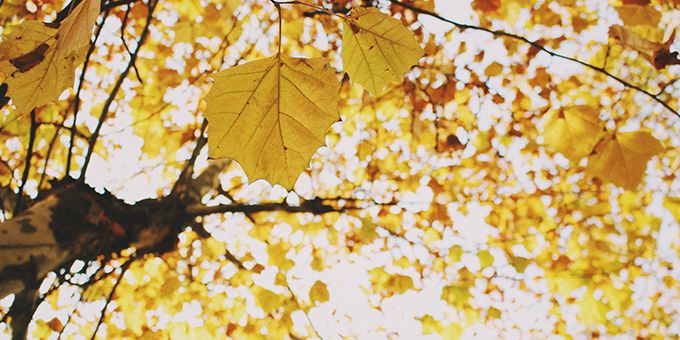
Dr. Raj Shah, Mr. Stanley Zhang, Mr. Andrew Kim | Koehler Instrument Company
Wind power is an essential source of electricity and accounts for about 8% of domestic energy in the US [1]. Modern wind turbines typically last for 20-25 years of operation. Depending on environmental conditions, the size of the turbine, and the wind speeds, a turbine can produce up to 6 million kWh in a year [2]. Wind turbines generate electricity from wind that passes through the turbine’s blades. The wind’s kinetic energy is then captured by the blades through rotation and is converted into mechanical power. The blade’s rotation causes the internal shaft, which is connected to the gearbox, to turn 100 times quicker, producing electricity [3]. Over the past decades, wind turbines have evolved in many aspects to become more relevant in today’s energy sector and are now considered a top renewable energy source that can help decrease coal-fired gas emissions. Although wind turbines have their advantages, they also have disadvantages, including high costs, suboptimal durability, and constant maintenance requirements in harsh weather conditions, which is especially true for offshore wind turbines. These problems need to be minimized for wind power to become a dominant source of renewable energy and aptly compete against conventional fossil fuels.
Currently, researchers in the industry are working to develop better turbine technology, such as higher efficiency generators and more reliable blades to minimize energy and manufacturing costs [3]. Wind energy industrial workers recently have also developed differently shaped and configured blades to improve the robustness and rotational speed [4]. Additionally, offshore wind power technology has been researched further, and this research brought about advantages and ways to minimize the disadvantages of these floating designs. In deep waters, studies found that although they required more dynamic cabling and were prone to more extreme weather and mooring costs, these offshore wind turbines could lower transportation, installation, and assembly costs when compared to onshore turbines. In addition, efforts have been made to lower building/repairing costs of offshore wind turbines, so platforms, like catenary moored semi-submersible platforms (CMSSP), tension leg platforms (TLPs), and the spar buoy, were heavily studied upon and developed. Several offshore turbines have been developed in Europe already, with similar developments likely to follow in the US and Japan due to their long coastlines and steeply shelving seabed bathymetries. It is expected that these countries will be the first to experience technical advances in floating wind power. Although maximizing the durability and efficiency of wind turbines are key priorities to consolidate wind energy as a premier source of renewable energy, considerations regarding costs and allocations, whether it be more installations in coastal areas or on mountains, are essential for evaluating the overall feasibility. This article will highlight the recent advancements in wind turbine technology, a comparison between onshore and offshore turbines, and future developments in store for wind energy.
New Upgrades for Wind Turbines
CMSSP
Regarding offshore wind turbines, the CMSSP is a platform designed to serve as the foundation of offshore wind turbines and is rapidly undergoing developments to allow these floating turbines to be durable and operate in deep waters [5]. These platforms are composed of a series of connections between columns and steel braces. These steel braces are attached to mooring lines, which are embedded in the seabed, as shown in Figure 1.
Figure 1. The layout of semi-submersible floating platforms for wind turbines [5].
As the depth of water increases, the manufacturing/repairing costs increase, but there are many benefits as well. Benefits include lower costs than the fixed-bottom configurations in deep waters, easier installation, effortless part removal, and a broader range of installation sites. Additionally, these foundations have several advantages over other widely used foundations because they can be installed on dock and transported to the sea, unlike TLPs or spar buoys. Other advantages include lower installation costs of the mooring system compared to other foundations and better hydrodynamic behaviors due to longer drafts and less wave exciting forces acting on it.
Techniques have been developed to simulate wind-fields, such as using the EllipSys3D with FLEX5, which is a three-dimensional flow solver that estimates the wind velocities in blade-section coordinates [5]. The in-rotor flow of the turbines shows little effect of instabilities, proving the model accurate for flow of wind on blades. The model is able to capture all important changes in the vertical axis wind turbines with good quantitative evaluation of the flowfield, acquire the radial expansion deformation of the wake, and rapidly calculate the aerodynamic performance of wind turbines under axial steady conditions [6].
TLPs
TLPs are often used for deep water oil/gas developments due to their favorable motion characteristics but are more expensive than spar buoys and catenary moored platforms. However, when TLPs are used as platforms for wind turbines, their displacement, tensile strength, and steel mass can be lowered. This is due to their overall weight being much lighter than when used for oil/gas platforms, allowing wave and wind forces to decrease when encountering the TLPs [7]. TLPs are experiencing greater popularity, as their conceptual design is an active area of research and industrial workers are starting to get more interested in using these platforms for deep water wind turbines. Most TLP’s structures consist of a single column and three to four pontoons which allow for substantial buoyancy. The hull is made up of a steel cylinder and a protruding cylinder to support the tension legs. It is desirable for the tendons to have negligible weight.
Figure 2. (a) shows a general TLP attached to a wind turbine and the possible wind directions. (b) shows the same TLP but shows the parameters to it (h1, D1, and D2 represent the hull, rp, hp, and wp show the pontoons, and the vertical bottom lines are the tension legs).
(c) is a different design which has hollow circular pontoons and tendons [7].
The primary objective of the hull in TLP wind turbines is to decrease electricity costs through maximizing power conversion efficiency, while minimizing operational, manufacturing and maintenance costs. To minimize manufacturing costs, steel mass, tensile strength, and overall size should be minimized. Limiting operation and maintenance fees requires the reduction of nacelle, tendon, tower, and blade loads. Optimizing the structure and design of the TLP is crucial to its effectiveness and lowering maintenance costs. In an experiment to determine which configuration would optimize the power conversion efficiency, lower the costs, and remain the most stable during harsh weather conditions, four different TLPs were designed for a comparative analysis. The first design had the heaviest hull, most stability, and shortest installation time of these designs and had similar maintenance and operational costs as the others; however, it was the most expensive to manufacture. The second design had 60% of the first design’s displacement but was unstable for towing-out because only 30% of the displacement was on the 3-legged pontoons [7]. The third and fourth designs were made after discovering the problems with the first and second designs. They both had 70% of the displacement on the pontoons, optimizing the distribution of the total weight of the TLP so that the other 30% from the hull could hold the wind turbines [7]. Although having less displacement than the other two designs made it more prone to damage, the costs were significantly less and the small column in the hull made the turbine more transparent to waves.
Spar buoys
Spar buoys are another commonly used platform for wind turbines, and similarly to TLPs, they are commonly used in offshore oil and gas industries. This spar concept has been deployed in the south-west coast of Norway and will be deployed in other coastal areas once the basic requirements of sufficient vertical, roll, and pitch stability are met. The spar-buoy is made from six sections all contributing to the stability of the wind turbine. Table 1 shows the six sections with their role.
Table 1. Different sections of the spar buoy listed with their intended functions and purpose [8].
Section |
Functionality |
Water plane area |
Water plane area, measuring vertical stiffness |
Transition |
Connects the water line with the buoyancy section |
Main buoyancy |
Voluminous section providing the main buoyancy |
Ballast (Heavy) |
A ballast is a heavy material, in this case made of iron, placed low in a vessel to provide stability |
Footing (most bottom section) |
Bottom plate which can also be used to increase vertical drag force and added mass |
Fairlead (Used for measuring tension) |
As the ballast increases the weight, the tension of the spar-buoy itself increases making it more prone to corrosion and cracks |
Pitch Bearings
Besides platforms, there are new upgrades to pitch bearings, which can be installed in both onshore and offshore wind turbines. Pitch bearings are what connect the spinner to the blades and can adjust the blades to a certain angle to optimize capturing wind. The downsides to typical pitch bearings are that they cannot rotate more than 90 degrees, have <5 degrees of an oscillation angle, are held stationary for long periods, and are subject to constant vibrating when the turbine is running. This puts a lot of stress on the pitch bearing components and can cause lubricant degradation and adhesive wear [10]. Additionally, these bearings are observed either bi-annually or annually because of the isolated locations of most wind turbines. The primary causes of bearing failure are poor lubrication and grease degradation, which can cause corrosion, vibratory wear, and debris denting [10]. Due to this, proper lubricant/grease selection and continuous-feed lubrication machines are important to ensure maximum efficiency and minimal maintenance. The wind turbine components that experience friction and wearing, and require lubrication are the pitch bearings, main shaft bearings, gearbox, Yaw drive, and generator bearing [11].
Figure 3. Mechanical components of a wind turbine [12].
Another area of concern is overloading, which happens when bearings are not firmly supported, leading to a fraction of the raceway carrying most of the load. Overloading can lead to contact truncation (probability can increase because of decreasing external support), raceway core crushing, and component fractures. However, with bearing upgrades, all these problems can be minimized or resolved entirely. Upgrades can include strengthening the races, edge loading, addressing separator wear, and working directly with a manufacturer who can offer advanced bearing solutions that can help save time and money. Additionally, with inducing separator rings, as shown in Figure 4, tensile and compressive load can be reduced. Alongside this, strict geometric dimensioning can create a near perfect form, resulting in less friction, skidding, and tight spots, which minimizes internal degradation and upgrades the pitch system response and efficiency. Pitch bearing seals play two crucial roles of preventing internal exposure and locking lubricants. Unfortunately, the old-fashioned seals are hydrogenated nitrile butadiene rubber, which degrades rapidly when exposed to UV, does not protect bearing internals and has a slow response to changes in wave frequencies. However, an upgraded seal called the “H-profile”, shown in Figure 4, is made from thermoplastic polyurethane significantly improving seal effectiveness [10]. It is highly responsive, works efficiently even when deformed, reduces grease leakage, and has a significantly lower wear rate than a rubber seal. These collective improvements help to enhance robustness and reduce maintenance costs.
Figure 4. Splitting the separator ring into segments allows limited individual freedom of movement, reducing the tensile and compressive load (top). The failed bearings (red) are rubber, while the upgraded bearings (blue) display the H-seal (bottom) [10].
Finally, proper storage packaging and handling is crucial to maintaining the clean slate of the bearings. Bearings should be packaged in volatile corrosion inhibitor paper and corrosion-preventative coatings for the prevention of contamination, degradation, and corrosion from hazards during transportation. It is also essential that prior to installing the bearings on the wind turbines, the bearing should still be wrapped because a little exposure to contaminants, especially dirt and water, can cause corrosion, hydrogen-induced fractures, static etching and fretting [10].
Onshore vs. Offshore Turbines
Offshore wind turbines are considered recent developments compared to conventional onshore wind turbines. Floating offshore wind turbines are harder to get to, are more prone to getting damaged, and are more expensive to install and operate. However, current technology advancements can strengthen the tower and provide more protection by handling forces of waves or ice flows. In addition, upgrading nacelles on these turbines can prevent corrosion from the sea water from damaging the electrical internal components. As the direction and speeds of winds are actually getting more and more predictable offshore than onshore with advancements in technology, investing in offshore wind energy will grow at a faster than normal rate and may serve as the top renewable energy source. The specific benefits and short comings that both kinds of wind turbines have been listed below in Table 2.
Table 2. The pros and cons of onshore and offshore wind turbines [13].
Onshore Turbines |
Offshore Turbines |
||
Pros |
Cons |
Pros |
Cons |
Considerably less expensive |
Limited efficiency due to unpredictable speed and direction of wind |
More efficient due to consistent wind speeds and directions |
Expensive technology associated with transferring energy from the turbines |
One of the cheapest forms of renewable energy |
Can endanger flying wildlife, such as birds and bats |
Less turbines required to produce an equal amount of electricity |
Increased operation and maintenance costs caused by increased wear from wind and waves |
Boost local economies |
Can cause noise pollution and negative visual impact |
No risk of visual impact and interference with land usage |
Longer wait times required to correct any potential problems due to more limited access |
Less emissions associated with the transportation of wind structures |
Inability to produce energy year-round due to reliance on optimal wind conditions |
Protects aquatic habitats by restricting access to certain waters |
Currently limited in its ability to benefit local economies |
Less voltage drops between windmill and the consumer |
No physical restrictions in these locations to block wind flow |
Future Developments
Rotor Size and Blade Shape
To reduce converting energy costs and optimizing energy production, researchers from the National Renewable Energy Laboratory (NREL) and Sandia National Laboratories (SNL) are working together to design 206-meter rotors for land-based turbines [14]. With larger blades, more kinetic energy from the wind can be harnessed and used to generate electricity. However, transportation and manufacturing costs will rise in response to increased material mass and demand. The NREL and SNL have also come up with a way to decrease the stiffness of the blades and for the turbine to hold more upcoming wind, regardless of speed [14]. The downward rotor configuration lowers the stiffness requirement because the wind pushes the blades away from the tower, which makes lighter blades and ensures tower safety/clearance. Figure 6 compares the traditional upward wind turbines with high blade stiffness requirements and the newly developed downward coned blades, which can track the wind using its cone mechanism. Carver’s Wind Blade Division and Sandia National Laboratories are developing a wind turbine blade which could potentially capture 12% more wind than regular turbines. The blade has a small, curved tip, unlike other turbines, that can optimize wind capture [14].
Figure 5. Variable coning configuration (left) [15] and traditional rotor configuration (right) [16].
Changing the shape of traditional turbine blades permits lighter blades to be made. This approach allows for aeroelastic stability, but at the cost of increased complexity for manufacturing and control. Researchers from the NREL are currently working on designing lighter blades and optimizing spar cap placements on the blades without increasing the thickness. This would minimize blade mass and increase the strength. However, there are also transportation issues with moving these large, assembled blades. Due to this, wind turbine components are being manufactured in sections, which are subsequently transported to be assembled on-site [14].
Robotic Inspection
Originally, the primary method for identifying damage on wind turbines was through manual inspection, which involved the use of a camera and telephoto lens. However, due to human limitations, wind turbine damages are rarely detected before reaching critical states. SNL, International Climbing Machines, and Dolphitech are working together to develop an autonomous robot that can vertically attach to a wind turbine, move, and detect any external or internal problems with onboard cameras and its “phased-array ultrasonic imaging” autonomously [17]. The purpose of this development is to locate turbine damage hastily in order to minimize maintenance costs and turbine downtime, which can improve turbine lifespan and efficiency. Autonomous robot inspectors can be used for both onshore and offshore wind turbines and can detect any abnormalities on wind turbines from any size of blades.
SNL is also working on equipping the drones with infrared cameras to detect damages through thermal imaging. This process involves exposing the blades to the sunlight and then covering them in shades. When there is no sunlight shining on the blades, the heat on the blades diffuses inside without harming anything. However, damaged areas prevent heat from diffusing inward, which leaves the surface hot and these hotspots on the infrared camera show damage.
Figure 6. Robotic crawler performing inspection on an onshore wind turbine [17].
Cold Weather Functionality
In recent news, winter storms battered the state of Texas during late-February of 2021, leaving over four million Texans without electricity and heat during the peaks of the outages [18]. The main cause to these power outages was attributed to disruption of the state’s natural gas, coal, and nuclear power plants due to freezing conditions. In addition, the extreme cold temperatures caused wind turbines to freeze, significantly inducing further outages, as Texas
has nearly 15,000 wind turbines and wind energy accounted for 23% of the state’s electricity in 2020 [19]. Although fossil fuels are the primary source of electricity production in Texas, the loss of wind turbines substantially increased energy shortages during the weather crisis, as energy demands skyrocketed.
Figure 7. A breakdown of the primary sources of electricity in Texas and consequently the sectors most impacted by the winter storms [20].
The poor low temperature functionality and lack of cold weather packages are the main reasons for the freezing of Texas’ wind turbines. Typically, wind turbines employed in colder regions are equipped with de-icing devices and integrated heating to protect crucial turbines components, such as the pitch and yaw motors, gearbox, and battery, from extreme negative temperatures [21]. Specialized cold weather and anti-icing technologies are designed to prevent ice accumulation on turbines blades, as well as the detection and removal of ice in unavoidable circumstances. Ice build-up on the blades of wind turbines can severely hamper their performance, as it adds weight and changes the aerodynamics of the blades, which can throw the spinning blades out of balance or prevent blade rotation entirely [19].
However, due to Texas’ historically warm climate, the addition of anti-icing mechanisms is forgone in favor of saving costs. The recent winter storms may bring about advocacy for the implementation of cold weather technologies to improve the functionality of wind turbines under frigid temperatures, in order to prevent weather-induced crises in the future.
The Lac Alfred Wind Farm located near Amqui, Quebec, had previously experienced significant turbine downtime due to ice accumulation, resulting in their implementation of Wicetec Oy’s Ice Prevention System (WIPS) [22]. This system makes use of integrated, carbon-based electrical heaters to quickly heat the surface of turbine blades to a controlled temperature when ice is detected [23]. Caribou Wind Farm in New Brunswick, Canada, has been testing the WIPS technology but has not been able to justify its costly implementation to all of its wind turbine blades. The lack of significant icing conditions has resulted in Caribou Wind Farm turning to other de-icing options, such as electrically heated tiles, usage of black paint on blades to absorb UV energy, and helicopter-applied coatings [22]. Despite having a much warmer climate, Texas could adopt similar cold weather solutions that are optimal for areas that infrequently experience icing, as further developments are made to improve efficiency and economic feasibility of the aforementioned technologies.
Figure 8. A helicopter spraying anti-icing agents directly onto the blades of a wind turbine, as tested by Caribou Wind Farms [23].
Conclusion
Wind power is a growing alternative energy source and may replace conventional fossil fuels in the future, given adequate research and development. There are many recent advancements/developments to the field of wind energy, such as offshore platforms that can decrease electricity costs and easily be installed on surfaces of deep waters. Deep waters near the coastal areas have predictable wind speeds and directions, allowing for optimal electricity generation. Additionally, future developments, such as robotic crawlers, can inspect and detect problems on the large wind turbines, while new advancements in rotor size and blades allow optimal wind usage, along with minimal manufacturing costs. Also, further emphasis is likely to be placed on the cold weather functionality of wind turbines, as extreme low temperature conditions can cause turbines to freeze over and leave significant populations without electricity and heat, as highlighted by the recent winter storms that swept through Texas. By comparing both onshore and offshore wind turbines, the similarities and differences between the two are apparent. Onshore wind turbines cost less to manage and manufacture but cannot produce energy all year-round. In addition, the locations of their installation sites experience unpredictable wind speeds and direction. Offshore wind turbines are more costly to manufacture and maintain but with investments and technological advancements, they can provide a lot more energy than onshore wind turbines.
The US Department of Energy (DOE) predicts that the country will have 404 gigawatts of wind power capacity by 2050, enough to fulfill more than one-third of the nation’s electricity demands [24]. With growing consumer demand for clean, renewable energy, the wind industry is the second fastest renewable energy source to grow, according to the US Bureau of Labor [25]. However, there are some drawbacks, like high construction costs and the poor durability associated with wind turbines. A technological innovation developed and currently being upgraded is the spider float design. This floating substructure technology was developed to maximize power generation to reduce costs and improve the economic viability of offshore wind turbines. Another important innovation made in wind turbines are direct drive generators (DDGs), which have the ability to generate electricity at the speed of the rotor [26]. However, expensive magnets are needed to substitute the original magnets in order to reach a specific frequency, but with lightweight DDGs and superconductor generators, no expensive material is required to reach optimal performance [26]. The upcoming decades are likely going to bring along more enhancements to wind turbines components and configurations, further pushing wind energy technology into the limelight of renewable energy.
About Dr. Raj Shah
Dr. Raj Shah is a Director at Koehler Instrument Company in New York, where he has worked for the last 25 years. He is an elected Fellow by his peers at IChemE, CMI, STLE, AIC, NLGI, INSTMC, The Energy Institute and The Royal Society of Chemistry An ASTM Eagle award recipient, Dr. Shah recently coedited the bestseller, “Fuels and Lubricants handbook”,
details of which are available at https://www.astm.org/DIGITAL_LIBRARY/MNL/SOURCE_PAGES/MNL37-2ND_foreword.pdf
A Ph.D in Chemical Engineering from The Penn State University and a Fellow from The Chartered Management Institute, London, Dr. Shah is also a Chartered Scientist with the Science Council, a Chartered Petroleum Engineer with the Energy Institute and a Chartered Engineer with the Engineering council, UK. An adjunct professor at the Dept. of Material Science and Chemical Engineering at State University of New York, Stony Brook, Raj has over 330 publications and has been active in the petroleum field for 3 decades. More information on Raj can be found at https://www.petro-online.com/news/fuel-for-thought/13/koehler-instrument-company/dr-raj-shah-director-at-koehler-instrument-company-conferred-with-multifarious-accolades/53404
About Stanley Zhang and Andrew Kim
Stanley Zhang and Andrew Kim are students at State University of New York, Stony Brook, where Dr. Shah the chair of the external advisory Committee in the Dept. of Material Science and Chemical Engineering.
References
[1] “Wind turbines provide 8% of U.S. generating capacity, more than any other renewable source.” EIA, 2 May 2017
[2] “How Long Do Wind Turbines Last? Can Their Lifetime Be Extended?” TWI, TWI
[3] “Basics of Wind Energy.” AWEA, AWEA
[4] “Next-Generation Wind Technology.” Energy.gov, Energy Efficiency and Renewable Energy
[5] Liu, Yichao, et al. “Developments in Semi-Submersible Floating Foundations Supporting Wind Turbines: A Comprehensive Review.” Renewable and Sustainable Energy Reviews, Pergamon, 6 Feb. 2016
[6] Tescione, G., et al. “Analysis of a Free Vortex Wake Model for the Study of the Rotor and near Wake Flow of a Vertical Axis Wind Turbine.” Renewable Energy, Pergamon, 10 Nov. 2015
[7] Bachynski, Erin E., and Torgeir Moan. “Design Considerations for Tension Leg Platform Wind Turbines.” Marine Structures, Elsevier, 3 Nov. 2012
[8] Cheng, Zhengshun, et al. “A Comparative Study on Dynamic Responses of Spar‐Type Floating Horizontal and Vertical Axis Wind Turbines.” Wiley Online Library, John Wiley & Sons, Ltd, 7 July 2016
[9] Fylling, Ivar & Berthelsen, Petter. WINDOPT: “An Optimization Tool for Floating Support Structures for Deep Water Wind Turbines. Proceedings of the International Conference on Offshore Mechanics and Arctic Engineering”, 2011
[10] Bayles, Corey. “Extending Wind Turbine Life with Pitch Bearing Upgrades.” Windpower Engineering & Development, Windpower Engineering, 3 Feb. 2020
[11] McGuire, By: Nancy. “Lubrication Challenges in the Wind Turbine Industry.” Energy Central, Tribology and Lubrication Technology, 18 Sept. 2019
[12] Saurabhjain. “Industrial Wind Turbine Components.” Mechanical Engineering, Invision Community, 21 Nov. 2015
[13] Cuffari, Benedette. “Offshore vs. Onshore Wind Farms.” AZoCleantech.com, AZO Cleantech, 11 Dec. 2019
[14] “Bigger Equals Better When It Comes to Wind Energy Potential.” Energy.gov, 21 Oct. 2019
[15] By. “FCPS.” Lanier's Hybrid Wind Turbine and Solar Panel Are in the News! | Lanier Middle School, Spotlight, 14 Nov. 2017
[16] Bortolotti, Pietro, et al. “Comparison between Upwind and Downwind Designs of a 10 MW Wind Turbine Rotor.” Wind Energy Science, Copernicus GmbH, 31 Jan. 2019
[17] Dormehl, Luke. “Crawler Robots And Imaging Drones Monitor Wind Turbines For Damage.” Digital Trends, Digital Trends, 27 June 2019
[18] Bogel-Burroughs, Nicholas, et al. “Texas Winter Storm: What to Know.” The New York Times. 20 Feb. 2021.
[19] Moriarty, Rick. “Why wind turbines in New York keep working in bitter cold weather unlike the ones in Texas.” Syracuse.com. 19 Feb. 2021.
[20] Browne, Ed. “Why Did Wind Turbines Freeze in Texas When They Work in the Arctic?” Newsweek. 18 Feb. 2021.
[21] Carpenter, Scott. “Why Wind Turbines In Cold Climates Don’t Freeze: De-Icing And Carbon Fiber.” Forbes. 16 Feb. 2021.
[22] Froese, Michelle. “The cold, hard truth about ice on turbine blades.” Windpower Engineering & Development. 25 Oct. 2018.
[23] “How to prevent Wind Turbine Icing? – The WIPS Technology.” Wicetec Oy. 2019.
[24] Marketing, GME. “What You Need to Know about the Future of Wind Energy: Green Mountain Energy.” Green Mountain Energy Company, Green Mountain Energy Company, 18 Dec. 2018
[25] Torpey, Elka. “Green Growth: Employment Projections in Environmentally Focused Occupations : Career Outlook.” U.S. Bureau of Labor Statistics, U.S. Bureau of Labor Statistics, Apr. 2018
[26] Osmanbasic, E. (n.d.). “The Future of of Wind Turbines: Comparing Direct Drive and Gearbox.” August 13, 2020
The content & opinions in this article are the author’s and do not necessarily represent the views of AltEnergyMag
Comments (0)
This post does not have any comments. Be the first to leave a comment below.
Featured Product
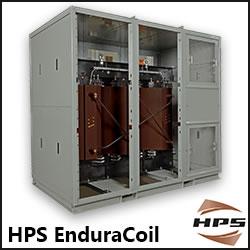