In this article, we will examine four key innovations that are revolutionizing the manufacturing of lithium-ion batteries that will power the electric vehicles of the future.
4 Innovations in Lithium-Ion Battery Manufacturing
Stéphane Melançon | Consultant, Technical Expert, EV Battery & Propulsion Systems
The marketplace for lithium-ion battery manufacturing is undergoing a remarkable transformation. Technological innovations aimed at enhancing sustainability, energy density, and production efficiency are giving rise to new solutions.
In this article, we will examine four key innovations that are revolutionizing the manufacturing of lithium-ion batteries that will power the electric vehicles of the future.
1. Batteries Built with Sustainable Materials
Cathodes without Nickel and Cobalt
EV manufacturers like GM and Ford now consider nickel, manganese, cobalt (NMC) batteries to offer the best trade-off between energy, power, charging speed, and the number of lifecycles. Just last year, NMC batteries had about a 60% share of the EV market.
While there have been breakthroughs that may significantly increase battery life, cathodes in these batteries rely on nickel and cobalt. Mining and manufacturing these materials generate a significant amount of pollution.
Manufacturers are looking at alternative battery technologies that do not rely on cobalt and nickel. They are increasingly considering lithium-iron-phosphate (LFP) batteries, which offer advantages similar to NMC batteries. The cathode materials in these batteries include iron and phosphate instead of nickel and cobalt. These materials are not only cheaper, but they are also more abundant and much more ethically sourced. Iron and phosphate are also found in a large number of locations, reducing the carbon footprint from transportation due to shorter distances.
Silicon-Based Anodes
Silicon is another abundant element that is getting attention these days. Anodes in batteries are typically made of graphite, but silicon is being developed as an alternative to graphite. Silicon offers a higher energy density, which directly translates into fewer batteries needed in battery packs.
While there’s been considerable interest across the automotive sector, even some of the industry’s biggest proponents say it may take more than 10 years for silicon to replace graphite as the main ingredient in anode. There are still pressing production issues — like swelling during charging and discharging — that need to be solved.
Solid-State Batteries
Solid-state batteries eliminate liquid electrolytes from batteries, replacing them with solid electrolytes. This makes batteries more secure by reducing the risk of fires and explosions. This significantly reduces the need for separate components for safety, saving more space. Solid-state batteries have the potential to offer a higher energy density, meaning they can store more energy in the same volume, helping overcome range anxiety for drivers.
However, there are still challenges that need to be addressed, such as higher production costs and production challenges. Manufacturers still need to find materials for solid-state electrolytes that are both highly conductive and stable over time. Cracks that form in the solid electrolyte during charging and discharging also need to be addressed.
Manufacturers clearly see the benefits of solid-state batteries, but commercial use is still a ways off. Toyota reports it has made substantial breakthroughs with solid-state technology and hopes to bring it to market by 2027 or 2028. Volvo’s CEO Jim Rowan recently said the tech is still some years off.
2. Laser Material Processing
One of the challenges in lithium-ion battery manufacturing has been scaling up production while minimizing the environmental footprint. To achieve this, manufacturers have been focusing on advanced manufacturing techniques that are more eco-friendly.
One key technique is laser material processing. Laser welding, laser cleaning, laser texturing, and laser cutting are all being used for battery manufacturing to scale up production and meet green goals.
For example, laser welding has improved significantly in recent years, making it a viable solution to interconnect cells and busbars. As a highly repeatable, non-contact process, laser welding can handle battery packs that have thousands of connections. Metals joined by laser welding have excellent electrical conductivity, minimal resistance, and improved heat management.
This makes it an excellent solution for mass production of batteries. In fact, no other technologies can offer the precision, speed, and low environmental footprint that lasers offer.
3. High-Energy-Density Batteries
Space usage and weight are crucial factors in battery packs. Optimizing them helps reduce the number of cells needed and improves the energy density. This, in turn, helps limit the size of the battery. These technological innovations are essential to increase the EV battery range.
In the last 20 years, manufacturers have doubled the energy density of cylindrical cells, going from 2Ah to almost 4Ah. Researchers have recently made substantive gains in this area, developing a rechargeable pouch-type lithium battery with an energy density exceeding 700 Wh/kg — a record.
Here are some of the strategies that help create better energy density.
Structural Batteries
Structural batteries accomplish several goals at once in electric vehicles by combining energy storage and structural support, and by eliminating the need for redundant structural elements. This type of battery becomes an integral part of the vehicle's structure, offering improved energy density and strength.
Known as mass-less batteries, they are assembled using adhesive bonding instead of screws or other fasteners. While this requires additional surface preparation (such as laser texturing), structural batteries have the potential to reduce weight by 10% or more. Tesla’s Model Y battery pack uses a structural battery component, but not everyone is sold on the concept. If such batteries are damaged in an accident, it can be extremely challenging to repair them.
Blade Batteries
Blade batteries are similar to prismatic cells in shape, but require fewer connections, making the manufacturing process much simpler. The design resembles a blade with positive and negative terminals on each end. Individual cells are configured in an array within the battery pack, improving space utilization by as much as half, which dramatically increases energy density.
Using LFP as the cathode material, blade batteries offer robust stability even at extremely high temperatures, making them safer than conventional lithium-ion batteries.
Like structural batteries, blade batteries serve a dual purpose as both an energy storage unit and a structural component of the EV and are also assembled using adhesive bonding instead of screws or other fasteners. Tesla, Ford, Toyota, and Kia have unveiled blade battery technology on some vehicles, most notably those manufactured in China.
4. Fast-Charging
If EV manufacturers want to significantly accelerate EV adoption, three significant challenges must be overcome: lower pricing, longer driving ranges, and faster — and more available — charging infrastructures.
Prices are coming down. Driving ranges are increasing. However, the charging infrastructure still needs a rapid build-out to meet aggressive emission reduction targets around the world.
Even then, EV drivers don’t want to have to wait for hours to get their vehicles back up to a full charge. Battery designs have to adapt to be compatible with fast charging stations and must have the right connector.
Currently, multiple fast charging standards exist. This is a problem because standards are not compatible with one another. While there some adapters are available, they are clunky and not always reliable.
Recently, Tesla released a new standard: the North American Charging Standard (NACS). It is quickly being adopted by other manufacturers. Ford, GM and many others have partnered with Telsa to license NACS ports for their vehicles starting in 2025.
Fast charging will not take place at home, where fast charging connectors will not be available due to compatibility issues with local power grids.
Research and Innovation Continues
Manufacturers and automakers are spending significant resources to develop innovative solutions for electrification. Reuters reports that the world’s top automakers have committed nearly $1.2 trillion for development between now and 2030. The U.S. Department of Energy (DOE) is currently funding 26 new lab projects for advanced battery technology with $209 million in funding.
Today’s lithium-ion batteries are benefiting from massive innovations. While many of the changes are not quite market-ready, the future is promising.
About Stéphane Melançon
Technical expert and consultant in batteries and electrical propulsion systems, Stéphane holds a Physics degree with specializations in Photonics, Optics, Electronics, Robotics, and Acoustics. Invested in the EV transformation, he has designed industrial battery packs for electrical bikes. In his free time, he runs a YouTube channel on everything electrical.
The content & opinions in this article are the author’s and do not necessarily represent the views of AltEnergyMag
Comments (0)
This post does not have any comments. Be the first to leave a comment below.
Featured Product
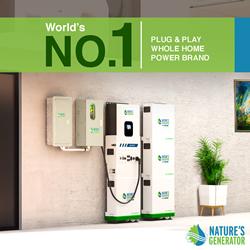