BESS systems undergo rigorous testing during the development process to ensure they operate safely and reliably. One of the most important steps of this pre-deployment protocol is Factory Acceptance Testing (FAT).
Guide to Factory Acceptance Tests (FAT) for BESS
Dr. Georg Angenendt | ACCURE Battery Intelligence
This blog will detail the various steps involved in successful FAT, their significance in confirming the BESS’ ability to operate safely and reliably and explore how data insights from predictive analytics can improve the preparation and execution of this process. Before we do that, however, we need to briefly review the phases of BESS development that come before and after FAT.
The Phases of BESS Development: Before and After FAT
BESS development is segmented into three distinct phases, with FAT sandwiched in the middle.
1. Pre-FAT
The pre-FAT phase encompasses three stages: requirements analysis and specification development, design and development, and production and assembly. First, a comprehensive needs assessment is conducted to identify the specific requirements of the system, followed by the creation of its technical specifications (based on the needs assessment) and contract finalizations. Then, the design phase commences, focusing on system design, prototyping, and design verification to ensure it meets with the technical specifications outlined beforehand. Finally, the production and assembly phase gets underway, involving manufacturing and procuring components to build the complete BESS, while carrying out in-house testing and quality controls.
The goal of the pre-FAT phase is to both identify and outline the system’s required specifications, and to ensure that it is fully operational before moving on to Factory Acceptance Testing (FAT).
2. Factory Acceptance Testing (FAT)
We’ll review Factory Acceptance Testing (FAT) in detail below, but for now know that the goal of FAT is to verify that the BESS meets the design requirements determined during the pre-FAT phase, and functions as it should in a controlled environment before it leaves the manufacturer's facility. As such, it occurs before shipping and installation and involves a series of tests to serve as a comprehensive evaluation of the system’s performance, safety, and compliance with pre-determined specs. It ensures that any defects or issues are identified and addressed before the system is delivered to the installation site, ultimately saving time and avoiding issues during Site Acceptance Testing (SAT) and deployment that follows.
3. Site Acceptance Testing
The purpose of Site Acceptance Testing (SAT) is to confirm that the system meets specified performance and safety criteria in its actual operational environment (this is the key difference between FAT and SAT). SAT involves conducting acceptance tests in accordance with pre-determined protocol, including performance testing under real-world conditions. The process encompasses functional testing of all operational modes and control systems, safety tests to ensure the system can handle faults, and integration testing to confirm smooth operation within the broader energy infrastructure. Once these tests are completed successfully, the BESS owner formally accepts the system, typically by signing an acceptance certificate.
Now that we’ve oriented ourselves on where FAT falls in the phases of BESS development, we can begin to unravel its significance in ensuring the long-term performance, safety, and reliability of the operational system.
What is Factory Acceptance Testing (FAT)?
As highlighted above, Factory Acceptance Testing (FAT) is a phase of BESS development that precedes Site Acceptance Testing (SAT) and follows the pre-FAT phase. The goal of FAT is to confirm that the BESS is ready for installation. Think of it as the dress rehearsal before the big show; this is the final check in a controlled environment to ensure the system’s performance, safety, and compliance with regulatory standards before it leaves the factory for the installation site. Given its importance, it’s understandably an extensive process. FAT is carried out in 7 distinct steps.
1. Document Review
The FAT process begins with a thorough review of all relevant documents. This includes affirming technical specs align with both contractual obligations and regulatory requirements, confirming the test plans meet standards, and verifying that the manufacturing process followed quality guidelines. The purpose of this step is to ensure the system was built correctly, and all contractual and regulatory obligations are met before testing begins.
2. Hardware Inspection
Following the document review, the hardware of the BESS undergoes a thorough inspection to confirm that it’s defect-free and assembled according to design. This starts with a visual inspection, where all physical components are examined for visible defects, damage, or deviations from the design specifications. Then, dimensional checks are conducted to verify that the components’ measurements match the design specs and schematic drawings.
3. Functional Testing
The purpose of functional testing is to verify that the system's components are properly connected and can safely power up. It begins with an integrity test to confirm that all components work together without issues. Next, a communication test is performed to ensure that all communication interfaces and protocols function correctly, so the BESS can interact properly with control systems. This phase makes sure that the system's core functionalities are intact and operational.
4. Performance Testing
Next, the BESS undergoes performance testing to evaluate how well it operates. This includes charge and discharge tests to check if the performs at specified rates and capacities. Cycle efficiency tests, which involve multiple charge-discharge cycles, assess the system's stability and efficiency over time. Additionally, temperature performance tests are carried out under various conditions to ensure the BESS can operate reliably in different environments. This phase is essential to confirm that the system can meet its performance requirements.
5. Safety Testing
Safety testing is a critical part of FAT, making sure the system can handle faults and operate safely. Short circuit tests are conducted to confirm the system's ability to manage short circuits without damage, while overcharge tests check its response to overcharging situations, preventing possible hazards. Insulation resistance tests are also performed to measure the insulation resistance between different parts of the system, ensuring that electrical safety standards are met. These tests are essential to guarantee the safety and reliability of the BESS in various operating conditions.
6. System Integration Testing
System integration testing verifies that the BESS works smoothly with other systems and components, like inverters and energy management systems (EMS). This phase is comprised of compatibility tests to confirm that the BESS can integrate seamlessly with other parts of the energy infrastructure, and operational simulations to mimic real-world scenarios, making sure the system responds as expected. This phase ensures that the BESS can function effectively as part of a larger energy system.
7. Documentation and Reporting
The FAT process concludes with thorough documentation and reporting. Detailed reports are compiled for all tests, including the results and any discrepancies found. Quality assurance documentation is also provided to confirm that the BESS meets all required quality and regulatory standards. This documentation is essential for tracking compliance and serves as proof that the system is ready for installation of the system’s readiness for installation.
Why is FAT Important?
FAT is the cornerstone of pre-deployment testing because it ensures that the BESS meets all specified requirements and standards before leaving the factory. By catching potential issues in a controlled setting, FAT allows for corrections to be made before the system is installed, minimizing the risk of failures during installation and initial operation. When FATs are poorly planned or executed, avoidable errors often go unnoticed, leading to unnecessary long-term issues later.
For example, consider these two common commissioning challenges, and understand how they can be avoided with properly executed FATs:
HVAC Issues
First, think about the role of HVAC systems within BESS deployments. Poor HVAC installations can impede the commissioning process and create long-term operational challenges. Faulty HVAC systems can cause battery cells to overheat, resulting in poor performance, safety risks, and even voided warranties in some cases. Mis-calibrated HVAC systems can also lead to significant energy losses, reducing the overall efficiency of the BESS.
Faulty Battery Cells
Faulty battery cells present another major challenge. Because battery cells are connected serially, a single defective cell can negatively impact the entire string, much like a weak link in a chain. This can lead to underperformance across the entire system.
Both HVAC issues and issues arising from faulty battery cells are observable, and therefore avoidable, through FAT testing based on analysis of temperature and electrical signals.
To come to the point, FAT serves as the first line of defense against operational issues and delays. It lays the foundation for smooth commissioning and profitable long-term operation. As BESS deployments continue to grow, rigorous FAT protocols remain non-negotiable for safeguarding against potential pitfalls and setting the stage for long-term success.
How to ensure a smooth FAT process?
Achieving a smooth Factory Acceptance Testing (FAT) process starts with careful planning and clear agreements with suppliers regarding what should be tested and how these tests should be carried out. Setting these expectations upfront helps avoid misunderstandings and ensures all parties are on the same page.
Beyond solid planning, using data-driven predictive analytics can significantly improve the FAT process. Detailed data insights enable FAT consultants to prepare thoroughly and adapt testing to specific requirements, ensuring a comprehensive system audit. This proactive approach allows for early detection of potential issues and provides actionable insights to address them before they escalate. The most notable advantages of incorporating data-driven predictive analytics into the FAT phase include:
- Pre-Test Review of FAT Requirements: Data analysis before testing helps identify any discrepancies or areas that need attention, ensuring the system meets all specifications.
- Early Detection of Weak Battery Cells and Equipment: Analyzing FAT data allows for the early identification of weak cells or faulty equipment, preventing larger long-term issues.
- Faster Acceptance Process: Early detection of non-compliant batteries can eliminate the need to ship faulty units, speeding up the acceptance process and reducing delays.
- Enhanced Battery Performance and Longevity: Identifying and removing weak cells before integration enhances the overall performance and lifespan of the system.
Figure 1 depicts an example in which data analytics revealed a significant spread in battery capacities during FAT, with a total deviation of almost 2%. While the internal resistance spread is in an acceptable range (lower 5%) for most of the cells, this capacity spread is wide and exceeded the agreed-upon limits of 0.5% per batch and 1% overall. Thanks to FAT analysis, non-complimenting battery cells were identified early, preventing imbalances in the serial-connected batteries that would have reduced system performance.
.png)
Figure 1: The capacity and internal resistance of the batteries were evaluated using data analytics following the FAT, revealing a capacity deviation of nearly 2%. This deviation exceeded the specified agreement, which required it to remain below 1%.
Conclusion
Factory Acceptance Tests (FAT) are a big milestone for customers to confirm that their assets meet the quality standards agreed upon during the pre-FAT phase of BESS development. Catching errors during this phase can lead to significant cost savings during the commissioning and operational phases to follow. However, if FATs are poorly planned or sloppily executed, avoidable errors may slip through the cracks, causing larger long-term problems down the line.
Integrating data-driven predictive analytics into the FAT process can significantly improve the quality of the audit. By improving preparation and tailoring check-ups to specific requirements, predictive analytics enable the early detection of potential problems, allowing for timely fixes. This approach not only accelerates the acceptance process, but also boosts the performance and lifespan of the BESS by identifying and removing weak cells before they’re integrated into the system.
Dr. Georg Angenendt is a scientist and entrepreneur with expertise in mobility and utility-scale battery energy storage systems (BESS). His research on testing, modeling, commissioning, and optimization of battery storage systems has been published in international journals and at conferences. Since 2020, he is the Chief Technology Officer at ACCURE Battery Intelligence, developing advanced analytics software to help companies assess battery risk, ensure safety, and maximize asset value. His personal passion is Martial Arts: mixed martial arts, luta livre, grappling, boxing and Brazilian jiu-jitsu.
The content & opinions in this article are the author’s and do not necessarily represent the views of AltEnergyMag
Comments (0)
This post does not have any comments. Be the first to leave a comment below.
Featured Product
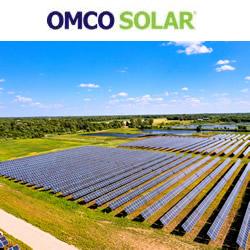