EPRI Test Site Validates Early Thermal Runaway Indicator
Duke Energy safeguards Li-ion Battery Energy Storage Systems with off-gas detection minutes before thermal runaway, allowing action to deter potential cascading failure
As an independent, nonprofit organization, the Electric Power Research Institute (EPRI) collaborates with the electricity sector to make electric power safe, reliable, affordable, and environmentally responsible. As part of that mandate, EPRI conducts research, development, and demonstration projects for the benefit of the public in the United States and internationally. This often entails performing trials utilizing promising products and technologies, in cooperation with leading utilities.
In recent years, EPRI has focused attention on evaluating and testing technologies to increase the safety of Battery Energy Storage Systems (BESSs). Comprised of an interconnected series of Lithium-ion (Li-ion) batteries, BESSs help utilities provide reliable back-up power, avoid peak demand charges, and store energy generated by renewable power systems.
However, despite the significant benefits, BESSs are subject to thermal runaway conditions that occur when excess heat caused by defects or mechanical failures from damage or improper operation of the system creates a reaction that further increases the temperature. If left unchecked by built-in system protections or the Battery Management System (BMS), this process can continue to drive up temperature and pressure until the battery cell ruptures, which can cause fires in affected and adjacent cells.
For this reason, EPRI is conducting trial tests with multiple utilities of an advanced early warning system that can detect an off-gassing event as a precursor to thermal runaway up to 30 minutes prior to a cascading failure. This distinctive and recognizable early warning sign enables the problem to be mitigated or the system shut down before thermal runaway can even begin.
"Once a Li-ion BESS goes into thermal runaway you cannot stop it [in that cell] - your goal is to try to stop the propagation of heat and thermal runaway to adjoining cells," explains retired NYC firefighter Paul Rogers, a co-founder of Energy Storage Response Group (ESRG), a national fire safety consultancy with nearly 50 years of combined experience that specializes in the risk assessment, investigation, and safety testing of energy storage systems.
While still with the NYC Fire Department, Rogers oversaw the implementation of the department's first response protocols for how to deal with energy storage systems, and now he consults nationally on this as well as safety testing.
According to Rogers, while a Battery Management System (BMS) can provide data and shut the BESS down, depending on the safety integrity levels of the BMS component there are times when the BMS can miss critical indicators or malfunction. Because of this, Rogers recognizes the need for a separate, redundant system that can indicate the potential of thermal runaway before it occurs so the BESS can be shut down to prevent it.
"You need layers of protection to reduce your risk," says Rogers, who recommends incorporating an additional early warning system besides the BMS.
In looking to improve energy storage system safety in NYC, Rogers was introduced to a product called Li-ion Tamer that provides advanced warning before thermal runaway in lithium ion BESSs. To Rogers' knowledge, no other product accomplishes this in a way that Lion Tamer technology does.
The early detection of thermal runaway relies on four sequential stages of Li-ion battery failure, according to Steve Cummings, Director of the Sensors Business Unit at Nexceris, an Ohio-based developer of gas sensors and monitors. The company worked with the U.S. Navy a decade ago to develop an off-gassing detection technology for Li-ion BESSs that would later be commercialized into the Li-ion Tamer product, which is compatible with all Li-ion chemistries.
"A Li-ion battery cell first begins to fail when it is subjected to an abuse factor like heat, overvoltage, etc.," says Cummings. "The second step is off-gassing. The third step is smoke, and the fourth step is fire. But smoke and fire often occur almost simultaneously. So, by the time smoke is detected, thermal runaway has typically already begun."
Off-gassing usually occurs due to a breakdown of a Li-ion battery cell electrolyte, as a result of pressure buildup. Later, temperature increases, smoke is emitted and then fire breaks out.
To enable off-gassing detection at the earliest stage of a battery event after the initial abuse, the Li-ion Tamer system offers a battery off-gas monitor and sensor network designed specifically for lithium ion batteries.
Fortunately, EPRI is currently testing Li-ion Tamer at several test sites. This includes Duke Energy's Emerging Technology Innovation Center in North Carolina, which has validated the system's ability to detect even minute traces of off-gassing as a precursor to thermal runaway minutes before it occurs, allowing action to deter potential cascading failure. Based on this success, EPRI member Duke Energy is implementing the technology and making it a standard practice.
Duke Energy (NYSE: DUK), a Fortune 150 company headquartered in Charlotte, N.C., is one of the largest energy holding companies in the U.S. The company provides electricity to 7.7 million retail electric customers in six states, serving an estimated 24 million people. It also provides natural gas to more than 1.6 million customers in five states, and operates wind and solar power facilities in 14 states.
According to Tom Fenimore, currently Duke Energy Business Development Manager assisting in deploying new leading-edge technologies, the company has tested energy storage for over a decade, and was approached by EPRI and Nexceris as a test site for this reason.
"We were educating ourselves in lithium ion energy storage, in deterring thermal runaway events, when we had the opportunity to work with Nexceris and install their off-gassing detection technology [in a BESS], which provides early detection of thermal runaway so it can be deterred," says Fenimore.
According to Fenimore, at the Mount Holly, North Carolina site, a pre-production version of Li-ion Tamer was initially tested in a BESS and improvements were later incorporated into a retrofitted production version. Today, Li-ion Tamer is utilized and continues to be tested in a BESS in a 20-foot container that is professionally developed and built for energy storage. The BESS is rated at 650 KWH, and can discharge roughly 350 KWH of energy. It has six racks of lithium ion batteries that are used daily in the operation of the micro grid that supports the Mount Holly Technology Innovation Center.
"We take a proactive approach to energy storage safety that involves implementing layers of protection," says Fenimore.
Fenimore states the first line of defense is the battery management system (BMS) because it is the system that manages the charging and discharging of the batteries. That is the first system that can sense whether an out of bounds condition exists within a battery cell. Since it monitors voltage and temperature, it has the first opportunity to put the battery into a safe state should an event occur.
"The next level of technology deployed inside our BESS systems is Nexceris Li-ion Tamer, which is deployed inside the container to sense whether a battery cell has gone into a condition where it off gases," says Fenimore. "That off gas event is a direct indication that the battery is in a compromised, abnormal condition. At that point, we take that signal and shut the battery down, disconnect the battery from the grid, ventilate and cool the battery, as well as alert people so proper maintenance can be done to address the problem."
Fenimore says that Duke Energy has participated in offsite disruptive testing by actively placing battery cells into a condition of thermal runaway under controlled conditions.
"We have seen from testing that we typically have early notification on the order of minutes that an event has occurred [before thermal runaway] when even seconds can make a difference," says Fenimore. "We want to take advantage of that capability wherever we can to protect the public and the capital asset we are deploying."
According to Fenimore, Duke Energy has projects built or planned across six states that use the technology.
"Nexceris Li-ion Tamer technology is standard in our BESS safety specifications and we are specifying it moving forward," says Fenimore. "The BESSs are typically deployed alongside solar, wind, or combinations of solar and traditional generators. The BESSs meet regulatory mandates for a Non-Wires Alternative because they do not require building additional distribution or transmission lines to get power to where it needs to go."
For utilities and other stake holders, when it comes to safely integrating new energy storage technology into municipal code, national safety consultant Paul Rogers of ESRG highlights the importance of adding adequate safeguards to avoid any incidents that could derail achieving more widespread support.
According to Rogers, back in the 1970s in NYC there was an explosion from a liquefied natural gas (LNG) facility that had nothing to do with LNG directly "Still, since then to this day, NYC has had a moratorium on LNG that prohibits new projects to be installed into the city without a variance because the fire department will not allow it," says Rogers.
The lesson, according to Rogers, is one that the battery energy storage industry should take to heart when it comes to rolling out lithium ion BESS technology: taking the time to fully test and implement safe equipment, methods and procedures always pays off in the end.
For more info, contact Nexceris: (614) 842-6606; visit https://nexceris.com; or write to Nexceris at 404 Enterprise Drive, Lewis Center, OH 43035, USA.
Featured Product
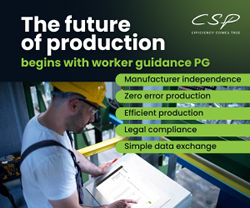