This report serves as an overview of gasification technologies processing municipal solid waste (MSW) that includes non-recycled plastic.
Residential And Commercial Refuse-Derived Fuel Waste To Energy
Dr S. Roy and Mr Richard H. Stone | Environmental Energy & Finance Corporation Ltd
EEFC develops Renewable Energy Projects by partnering companies with the funding and technology resources necessary to see their projects through to completion and beyond.
In much of the world, a massive infrastructure deficit exists including in the electric power sector. As a result, in many parts of the world today energy is extremely expensive and unreliable, and in many cases access is non-existent.
We look to develop businesses that offer the proverbial “win-win” solutions for customers that range from manufacturing and industrial users, to entire countries. We seek to develop businesses that simultaneously lower a consumer’s energy costs while increasing the quality and reliability of the energy supplied. In most of the markets where we are active, we also substantially improve the environmental profile (including CO2 emissions) of the country’s energy use. Our projects increase reliability and efficiency, use local resources and/or utilize innovative clean technologies.
Our strategic focus is upon high-growth, under-served markets and innovative niches within developed markets around the world. Our experienced team works closely with clients, governments, regulators, and financial institutions to develop pioneer projects that improve the businesses and communities that we serve. Our engineering team boasts experience in a variety of generation technologies.
Suryachakra Global Enviro Power Limited, a wholly owned subsidiary of Suryachakra, seized an opportunity in the renewable energy source to establish a 9.8 MW biomass fuel based power plant on a 30 acres site near Madwa village in the Champa-Janjgir district of Chhattisgarh State in May’2008. The project is under operation through long term power purchase agreement with the Chhattisgarh State Power Distribution Company Limited (CSPDCL). The project has been registered with the UNFCCC for receiving of CERs.
INTRODUCTION
Municipal solid waste (MSW) is a domestic energy resource with the potential to provide a significant amount of energy to meet Electrical Energy and/or liquid fuel requirements. MSW is defined as household waste, commercial solid waste, non-hazardous sludge, conditionally exempt, small quantity hazardous waste, and industrial solid waste. It includes food waste, residential rubbish, commercial and industrial wastes, and construction and demolition debris. It has an average higher heating value (HHV) of approximately 5100 btu/lb (as arrived basis).
MSW is a heterogeneous feedstock containing materials with widely varying sizes and shapes and composition. This can be difficult to feed into many Gasifier and can lead to variable gasification behaviour if used in an as received condition. It is expected that some minimal size reduction and sorting will need to be performed to make MSW suitable as a feedstock for MSW Gasifier.
The United States, alone, creates over 250 million tons of waste each year. Landfills are exceeding their capacities all over the world. Not only that, they are major emitters of greenhouse gases and sources of harmful environment contamination. No one has found a way to cleanly and profitably convert all of this waste. FastOx leverages the centuries-old blast furnace, as an efficient and scalable means to convert nearly any form of waste into renewable energy. This technology has several advantages:
- Massive Size and Scalability
- FastOx can scale from 5 to well over 10,000 tons per day in a single unit.
- Simple Design
- The straightforward design of the blast furnace provides FastOx gasifiers with several maintenance and operation advantages, including the lack of moving or complicated parts and minimal maintenance or down-time.
- Waste Flexibility
- Because FastOx gasifiers can be utilized in multiple settings using multiple types of feedstock, Sierra Energy can target complex segments of the waste market. These markets include hazardous waste, MSW, industrial waste, medical waste, and construction and demolition (C&D) waste.
- Thorough Waste Conversion
- FastOx gasifiers thoroughly convert waste without creating toxic products requiring disposal.
- Retrofit Opportunities
- Sierra Energy plans to convert existing, idled blast furnaces into a commercially-viable FastOx gasifier, saving millions in initial capital investment.
- Global Support
- FastOx gasifiers can leverage the global support industry that already exists to service blast furnaces.
Feedstock Flexibility
Potential feedstocks for conversion process include:
Woody biomass
- Pulp logs
- Logging residue such as tops and limbs of trees
- Urban wood waste such as wood from tree cover
Agricultural residues
- Feed residues left in field after harvest (e.g., stalks, stems, leaves)
- Process residues left over from processing crop into usable product (e.g., bagasse, husks)
- Energy crops
- Crops grown expressly for biofuels (e.g. switchgrass, sorghum)
Refuse derived fuel (RDF) is defined as the product of a mixed waste processing system in which certain recyclable and non-combustible materials are removed with the remaining combustible material converted for use as a fuel to create energy.
Typical RDF processing includes ferrous material removal, shredding, screening, crushing, and even eddy-current separation or air classification for aluminium recovery. Some operations further grind/shred, and mix material to generate a homogeneous fuel. It is also common for processors to press and extrude the material into pellets. On average, 75%–85% of the weight of MSW is converted into RDF and approximately 80%–90% of the BTU value is retained. This leaves RDF with a higher heating value of 4,800–6,400 Btu/lb, which is approximately half of the Btu value of the same weight of coal.
The main benefits of converting MSW to RDF are a higher heating value, more homogeneous physical and chemical compositions, lower pollutant emissions, reduced excess air requirement during combustion, and finally, easier storage, handling, and transportation.
Refuse derived fuel (RDF) is a processed form of MSW where significant size reduction, screening, sorting, and, in some cases, palletisation is performed to improve the handling characteristics and composition of the material to be fed to a Gasifier. The trade-off between the increased costs of producing RDF from MSW and potential cost reductions in Gasifier design and operation are explored. The chemical make-up of MSW includes significant quantities of chemical constituents that can create problems in downstream processes. While the concentrations of these contaminants are greater than that found in conventional biomass feedstocks, they are roughly comparable to those found in coal.
Refuse Derived Fuel (RDF) Bales for Export
According to the United States Environmental Protection Agency (EPA), the annual national MSW production in 2006 totaled more than 251 MM short tons, which equates to greater than 4.5 lbs/person/day. Of this total, about 45% is recovered via recycling, composting, and energy production. This leaves approximately 138 MM short tons of unutilized MSW, which has about 1.4 x 1015 Btu (1.4 quadrillion Btu) fuel value associated with it.
MSW has potential as a Gasifier feedstock because it has a HHV (dry basis) that is nearly as high as most conventional biomass feedstocks. What makes it appealing as a potential feedstock is that it is readily available in the near-term having a pre-existing collection/transportation infrastructure and fee provided by the supplier that does not exist for conventional biomass resources.
This report investigated the potential of using MSW to make synthesis gas (syngas) suitable for production Electricity. This also highlights the legal and environmental issues that must be considered.
- MSW physical and chemical properties affecting its suitability as a gasifier feedstock and for liquid fuels synthesis
- expected process scale required for favourable economics
- the availability of MSW in quantities sufficient to meet process scale requirements
- Industrial Emission Directive
- Renewables Obligation
- the state-of-the-art of MSW gasification technology.
- Technologies that provides Environmental Protection and passes USA and European Union strict emissions controls
- Main components of the synthesis gas
- Emission of Specific synthesis gas compared with emission of natural gas for running gas turbo engines.
Government’s main focus is on preventing waste in the first place or where it does arise ensuring it is viewed as a valuable resource, ideally reusing or recycling it. It is also Government policy that efficiently recovering energy from residual waste has a valuable role to play in both diverting waste from landfill and energy generation.
In the 2011 Waste Review one of the guiding principles, now enshrined in law, for European and UK waste management has been the concept of a hierarchy of waste management options, where the most desirable option is not to produce the waste in the first place (waste prevention) and the least desirable option is to dispose of the waste to landfill with no recovery of either materials and/or energy. Between these two extremes there are a wide variety of waste treatment options that may be used as part of a waste management strategy to recover materials (for example furniture reuse, glass recycling or organic waste composting) or generate energy from the wastes (for example through incineration, or digesting biodegradable wastes to produce usable gases).
Waste Disposal has been a problem for centuries. Now that it is an essential and not an option in any country in the world, this problem however ties in nicely with a problem of diminishing natural fuel supply stock of the world. Generating energy from waste is a win-win situation.
The second problem is described as below.
Fossil fuel consumption has increased over the past century, becoming a primary source of energy for many countries around the world and accounting for over 85% of the global energy produced. In combination with a rise in energy demands, this dependence on fossil fuels is leading to high carbon emissions resulting in climate change problems. In addition, because fossil fuels are a finite source of energy, energy prices are continuing to rise due to the depletion of fossil fuel reserves. One of the guiding principles, now enshrined in law, for European and UK waste management has been the concept of a hierarchy of waste management options, where the most desirable option is not to produce the waste in the first place (waste prevention) and the least desirable option is to dispose of the waste to landfill with no recovery of either materials and/or energy. Between these two extremes there are a wide variety of waste treatment options that may be used as part of a waste management strategy to recover materials (for example furniture reuse, glass recycling or organic waste composting) or generate energy from the wastes (for example through incineration, or digesting biodegradable wastes to produce usable gases).
THERMAL TREATMENT- INCINERATION
Incineration of MSW in the UK always involves some form of energy recovery, either in the form of electricity generation and/or heat recovery. As such it is also commonly termed Energy from Waste. Incineration usually involves the combustion of unprepared (raw or residual) MSW. To allow the combustion to take place a sufficient quantity of oxygen is required to fully oxidise the fuel (waste). Typically, incineration plant combustion temperatures are in excess of 850C and the waste is converted into carbon dioxide and water.
Any non-combustible materials (e.g. metals, glass) remain as a solid, known as Bottom Ash which contains a small amount of residual carbon.
ADVANCED THERMAL TREATMENT
Advanced Thermal Treatment technologies are primarily those that employ pyrolysis and/or gasification to process municipal solid waste (MSW). The gasification and pyrolysis of solid materials is not a new concept. It has been used extensively to produce fuels such as charcoal, coke and town or producer gas.
Charcoal and coke are produced by pyrolysing wood and coal respectively and producer gas is a combustible gas produced by the gasification of coke in the presence of air and steam. It is only in relatively recent years that such pyrolysis and gasification have been commercially applied to the treatment of MSW. The development of pyrolysis and gasification technologies for commercial and prepared municipal waste is becoming established for some technologies in the UK, whereas other technology configurations are still at the pilot / early development stages. Other large scale ATT plants have been built and are in operation in North America, Europe and Japan.
DIFFERENCE BETWEEN GASSIFICATION AND PYROLYSIS
New technologies for dealing with residual municipal waste are now becoming more popular with local councils. Most of these variations of incineration involve a combination of two advanced thermal processes: pyrolysis and gasification. These processes use high temperatures to break down any waste containing carbon. Pyrolysis degrades waste, producing char or ash, synthetic gas and pyrolysis oil. Gasification uses a controlled amount of oxygen to break down the hydrocarbons left into a synthetic gas. There are economies of scale for all thermal treatment plant. Smaller scale solutions can provide for more local / integrated waste management needs and potentially make it easier to find local markets for energy generated from the facility.
GASSIFICATION
Energy recovery via gasification of municipal solid waste (MSW) is an emerging conversion technology drawing increasing interest across the globe. Gasification technology potentially offers feedstock flexibility and customization for generating a range of desirable products. Gasification’s main product is synthesis gas (syngas) that is further processed into electricity, ethanol, diesel, or other chemicals. There are 147 companies offering gasification technologies in different stages of development worldwide, most of which market in the U.S. through licensees. Gasification is one of a growing number of exciting new technologies under development that may one day harness the potential of waste as an abundant source of domestic energy.
Plastics are a valuable resource, and we need to recycle them whenever it makes sense to do so,” urged Steve Russell, vice president of plastics for the American Chemistry Council. “But not all plastics can be recycled in a way that’s economically and environmentally efficient. Emerging technologies that can convert waste into electricity, higher value fuels and chemicals can help us capture plastics’ high-energy value and put it to work to help power communities across America,” he added. The report, ‘Gasification of Non-Recycled Plastics from Municipal Solid Waste in the United States’ offers an overview of gasification technologies, feedstock flexibility, outputs and economics, licensing companies, experience with gasification technologies, opportunities and barriers to commercialization, and the potential role of gasification in integrated waste management systems.
Gasification is the process of converting carbon based products such as coal, biomass, fat oil and grease. This basic process takes place in a Gasifier which is a chamber where the air flow, fuel flow, and temperature can be controlled. Furthermore steam can be added to control the gasification process. Once gas has been produced in the Gasifier it can for example be used for power production through a traditional combustion process. The oxygen free decomposition of raw organic materials into gas due to an elevated temperature is known as pyrolysis. In the gasification process pyrolysis occurs converting raw materials containing carbon into a combustible gas containing mainly carbon monoxide, methane, hydrogen, and tars. This is done by causing a chemical reaction between the product and an amount of oxygen in a Gasifier to produces a gas mixture known as synthetic gas, or syngas. Gasification is a highly efficient method for obtaining energy from organic materials, and can be used as a method for disposing of waste. Syngas is more efficient than the original organic material, as more of the energy in the fuel is extracted. . Syngas from gasification burns cleanly and without any harmful emissions. In fact, the only emissions from gasification are water vapour and carbon dioxide.The high BTU value of non-recycled plastics makes them attractive feedstock components for gasification processes. Gasification is a mature technology and is proven for applications such as in the petrochemical industry. Gasification is attractive because of the versatility of its final marketable products such as steam, electricity, ethanol and other chemicals.
There are currently four types of commercial Gasifier available, counter current fixed bed, co- current fixed bed, fluidised bed and entrained flow. The Counter Current Fixed Bed (up draft) Gasifier has a fixed bed of carbon fuel such as coal or biomass, through which steam, oxygen or air flows through in a counter clockwise direction. The throughput of this method of gasification is quite low, but thermal efficiency is high. Tar and methane production is quite considerable at normal operating temperatures, meaning that the syngas must be cleaned before it can be used. The Co-current Fixed Bed (down draft) Gasifier is similar to the Counter Current Fixed Bed Gasifier, except that oxygen flows downwards. Gas produced by this method of gasification is at a higher temperature and has similar energy efficiency to the Counter Current method. Tar levels are much lower than Counter Current gasification.
This basic process takes place in a Gasifier which is a chamber where the air flow, fuel flow, and temperature can be controlled. Furthermore steam can be added to control the gasification process. In the Gasifier of pyrolysis takes place at a lower temperature than normal Gasifier. Once gas has been produced in the Gasifier it can for example be used for power production through a traditional combustion process.
PYROLYSIS OF MUNICIPALITY WASTE
Pyrolysis is the precursor to gasification, and takes place as part of both gasification and combustion. It consists of thermal decomposition de composition of organic material at elevated temperatures in the absence of oxygen . It involves the simultaneous change of chemical composition and physical phase, and is irreversible in the absence of oxygen. It is essentially based on a long established process, being the basis of charcoal burning. The product of pyrolysis includes gas, liquid and solid In general; pyrolysis of organic substances produces gas and liquid products and leaves a solid residue richer in carbon content
Pyrolysis plants are typically used to degrade carbon-rich organic materials such as biomass, household and commercial waste, residues from materials recycling, and more recently, municipal solid waste. Upon arriving on site, these organic materials must first be sorted and pre-treated. Organic matter is sterilized and inorganic materials, such as metal and ceramics, are removed, leaving behind the desired pyrolysis feedstock.. The remaining feedstock is shredded and the moisture content is lowered to ~1% to reduce any wasted energy (Gale, 2001). Rotary kilns, rotary hearth furnaces, and fluidized bed furnaces are commonly used as waste pyrolysis vessels. Material is supplied to these vessels which are then heated to temperatures as high as 500-800oC. Various proportions of char (ash), pyrolysis oil, and syngas are produced based on such factors as organic composition and reaction parameters, including temperature, pressure, and time (Veringa, 2005). Syngas is cleaned to remove particulates, hydrocarbons, and soluble matter, and then combusted to generate electricity (Friends of the Earth, 2002). In some cases, gas may further be sterilized by processes such as gasification. Pyrolysis oil may also be used as liquid fuel for diesel engines and gas turbines to generate electricity as well. The syngas is a mixture of gases (combustible constituents include carbon monoxide, hydrogen, methane and a broad range of other VOCs). A proportion of these can be condensed to produce oils, waxes and tars. The syngas typically has a net calorific value (NCV) of between 10 and 20MJ/Nm3. If required, the condensable fraction can be collected by cooling the syngas, potentially for use as a liquid fuel. One key issue for use of syngas in energy recovery at ATT facilities are the problems related to tarring. The deposition of tars can cause blockages and other operational challenges and has been associated with plant failures and inefficiencies at a number of pilot and commercial scale facilities. Tarring issues may be overcome by higher temperature secondary processing.
INDUSTRIAL EMISSION DIRECTIVE
Industrial Emissions Directive (IED) / Waste Incineration Directive (WID)
In the UK, all waste incineration plant and ATT plant must comply with the Waste Incineration Directive (WID)4 2000. The requirements of the Directive have been translated into the UK through The Waste Incineration (England and Wales) Regulations 20025 which came into force on 28 December 2002. The Industrial Emissions Directive (IED)6 is a recast of the WID alongside six other European Directives, which will be transposed into English legislation no later than 6th January 2013. The objectives of the IED are to “reduce emissions into air, soil, water and land and to prevent the generation of waste, in order to achieve a high level of protection of the environment taken as a whole”.
Specific emission limits for the release to atmosphere of the following:
- Sulphur Dioxide (SO2);
- Nitrogen Oxide and Nitrogen Dioxide (NO and NO2);
- Hydrogen Chloride (HCl);
- Hydrogen Fluoride (HF);
- Gaseous and vaporous organic substances expressed as Total Organic Carbon (TOC);
- Carbon Monoxide (CO);
- Dust;
- Heavy Metals; and
- Dioxins and furans;
RENEWABLE OBLIGATION
The Renewables Obligation (RO) was introduced in 2002 to promote the development of electricity generated from renewable sources of energy. The Obligation requires licensed electricity suppliers to source a specific and annually increasing percentage of the electricity they supply from renewable sources, demonstrated by Renewables Obligation Certificates (ROCs). The target is currently set at 15% by 2020. In essence, the RO provides a significant boost to the market price of renewable electricity generated in eligible technologies. The RO will close to new operators at the end of the 2016/17 financial year. Those already accredited under the RO will continue to receive their full lifetime of support until the scheme closes in 2037.
Electricity generated from the biomass (renewable) fraction of waste by advanced conversion technologies (including pyrolysis and gasification) is eligible for support under the RO. In the case of ATT, this applies to the electricity generated from the syngas. This can provide an important additional revenue stream for a proposed plant, as long as it meets the qualifying requirements. As the value of a ROC is not fixed, the long term value would need to be assessed in detail to determine its overall financial value to the project, in addition to other renewable energy incentives available. RHI can be retrieved from the following sources:
Renewables Obligation (RO) see the DECC website, Pursuant to Article 5(1) of the Directive Member States must set up a national strategy for the implementation of the reduction of biodegradable waste going to landfills not later than 16 July 2003 and notify the Commission of this strategy. The strategies should include measures to achieve the targets set out in Article 5(2) by means of in particular recycling, composting, biogas production or materials/energy recovery.
Article 5(2) requires the reduction of biodegradable municipal waste going to landfills to
- 75% by 16 July 2006
- 50% by 16 July 2009 and
- 35% by 16 July 2016
Calculated on the basis of the total amount of biodegradable municipal produced in 1995 or the latest year before 1995 for which standardised Eurostat data is available.
EMMISSION OF A SPECIFIC SYNTHESIS GAS
Table 1: Main components of the synthesis gas
Reference |
Concentration |
|
|
VOL % |
VOL % |
Hydrogen |
22 |
15 – 30 |
Carbon monoxide |
11 |
5 – 15 |
Carbon dioxide |
17 |
15 – 25 |
Methane |
21 |
15 – 25 |
Ethene / Ethane |
13 |
10 – 15 |
Propene / Propane |
12 |
8 – 15 |
Other Hydrocarbon |
2 |
1 – 2 |
Nitrogen |
2 |
0 – 6 |
Table 2: Maximum Contaminate Concentration in the Synthesis gas
Component |
Concentration in mg/Nm³ |
PM |
30 |
HCl |
60 |
HF |
5 |
SO2 |
100 |
Cd |
0.2 |
Hg |
0.2 |
Dr. R. Unger, Kunststoff- und Umwelttechnik GmbH Waldstrasse 12/13 D 03149
Environmental Energy & Finance Corporation (EEFC) is a Developer of Power Plants with qualified Renewable Energy and Traditional Power Plants and only uses the “Best in Class” Technologies that provides Environmental Protection and passes USA and European Union strict emissions controls.
EEFC has developed close working relationships with some of the Leading Construction and Engineering Companies of the World to give experience and excellent completed projects throughout the World.
Artist conception of WTE Plant
LIST OF EEFC PARTNER EPC COMPANIES:
-
AECOM / Tishman Construction Company
-
POSCO Engineering & Construction Company
-
Hyundai Engineering Company
-
RW Beck
-
International Applied Engineering Company
-
GE Energy
-
Siemens
-
Alstom Power Generation
-
Honeywell
Cross Section of Turbine
Defining a new era of flexible power generation, GE’s revolutionary LMS100® provides a single, economical solution for the dispatch needs of nearly every condition. With unparalleled efficiency, 10-minute start times, unmatched hot day performance, load following and cycling capabilities, the LMS100 is the ideal solution for power generation planners and developers.
GE Energy - LMS100 Aeroderivative Gas Turbines
Internal Configuration of GE Gas Turbine
Features & Benefits
GE’s LMS100 provides an economical solution for the dispatch needs of nearly every condition. With 44% simple cycle efficiency, 10-minute starts, superior hot-day performance, load following and cycling capabilities and proven high reliability, the LMS100 is the ideal solution for power generation planners and developers.
Highlighted features are:
- Peaking power generation
- Load following power generation
- Mid-merit power generation
- Base load power generation
- Grid Stability
Emissions from the Combustion of Natural Gas - Natural gas is the cleanest of all the fossil fuels, as evidenced in the Environmental Protection Agency’s data comparisons in the chart below, which is still current as of 2010. Composed primarily of methane, the main products of the combustion of natural gas are carbon dioxide and water vapor, the same compounds we exhale when we breathe. Coal and oil are composed of much more complex molecules, with a higher carbon ratio and higher nitrogen and sulfur contents. This means that when combusted, coal and oil release higher levels of harmful emissions, including a higher ratio of carbon emissions, nitrogen oxides (NOx), and sulfur dioxide (SO2). Coal and fuel oil also release ash particles into the environment, substances that do not burn but instead are carried into the atmosphere and contribute to pollution. The combustion of natural gas, on the other hand, releases very small amounts of sulfur dioxide and nitrogen oxides, virtually no ash or particulate matter, and lower levels of carbon dioxide, carbon monoxide, and other reactive hydrocarbons.
Configured Power Plant
Heat recovery steam generators (HRSG) by Alstom are designed to deliver high performance and crucial efficiencies in gas power plants – all at a cost effective price.
The power generation market demands that combined cycle power plants increase capacity at a lower cost, operate efficiently and cycle more often to meet with strict environmental controls. Alstom’s automation and control solutions manage the energy dispatched by your gas power plant, from fuel supply and plant performance to emission monitoring and grid connections for maximum flexibility.
Control Room View
The ALSPA® Series 6 product line provides a consistent technology from low-level controls to high level asset management dashboard and optimization tools. This Alstom automation and control solution ensures data consistency and an ideal platform for power operators in plant and fleet management requiring remote feature centralization.
PRM Gasification Plant making Electricity for over 25 years with Rice Hulls
Fastox Waste Gasification
CONCLUSIONS:
-
This report serves as an overview of gasification technologies processing municipal solid waste (MSW) that includes non-recycled plastic, and an inventory of a company’s actively developing gasification technologies worldwide. Mass burn starved-air, two-stage combustion systems have a first stage gasification process. This (starved-air two-stage combustion) is a proven technology with several operating facilities in the U.S.
-
The high BTU value of non-recycled plastics makes them attractive feedstock components for gasification processes
-
Gasification is a mature technology and is proven for applications such as in the petrochemical industry
-
Gasification is attractive because of the versatility of its final marketable products such as steam, electricity, ethanol and other chemicals
-
This report also addresses challenges to developing gasification facilities in local communities and discusses potential solutions.
-
This presentation identified available MSW Gasifier that may be built as a package system to generate electricity as standalone or to complement local grid system.
-
Overall, this study concludes that MSW should be considered as a potentially viable Gasifier feedstock for generating electricity. A review of feedstock availability, composition, and handling characteristics, along with commercially available MSW specific Gasifier, did not identify any obvious insurmountable technical or economic barriers to commercialization.
References:
1. www.gov.uk/.../energy-from-waste-a-guide-to-the-debate
4. http://www.foe.co.uk/resource/briefings/zero_waste_wales.pdf
5. http://www.waste-management-world.com/recycling.html
6. www.decc.gov.uk/en/content/cms/meeting_energy/renewable_ener/renew_obs/reneobs/reneobs.aspx
7. nepis.epa.gov/Exe/ZyPURL.cgi?Dockey=10000VWJ.tx
8. www.nrel.gov/docs/legosti/old/4988A.pdf
9. www.biomass.uk.com/gasification.php
10. www.dongenergy.com/pyroneer/Gasification_Process/Pages/Gasification_theory.asp
The content & opinions in this article are the author’s and do not necessarily represent the views of AltEnergyMag
Comments (1)
Featured Product
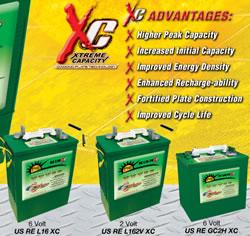