Assessing the LCPV versus HCPV tussle
Comparison of high concentration and low concentration Photovolatics
"The world is blessed to have more than one option"
CPVToday.com Special
There are several aspects of the CPV technology which makes this burgeoning sector to be an intriguing one as of today.
And one of them is surely the LCPV versus HCPV tussle.
In order to have a viewpoint of various professionals from the industry, CPVToday.com recently spoke to executives from Sol3g and a scientist from National Renewable Energy Laboratory (NREL), who are all scheduled to speak during CPV Summit USA 2009 (scheduled to take place on February 3-4 in San Diego), about the same. Here is what they had to say:
Sarah Kurtz, Principal Scientist, PhD, NREL:
The debate about which technology will come out on top is, of course, very important to the investors, but may not be so important to the success of a company.
You may have a similar debate about battery technologies, but there are many, successful battery technologies. Similarly, there will be many successful PV technologies, and the potential size of the solar industry will provide opportunities for many players. The world is blessed to have more than one option.
Perhaps the more relevant question is to identify how the markets for these two products may differ. The HCPV approach has the potential to deliver the highest efficiency.
If >30 percent system efficiency is achieved, this may be a useful driver for some applications. On the other hand, the LCPV has the potential to use more of the diffuse solar resource, so it may be applicable in a wider range of climates.
Ricard Pardell, president and R&D director, Sol3g:
I am sorry for the low concentration defenders, but for us there is really no question.
Multi-junction cells have very high efficiencies but their unit cost requires high concentration (we have 476 suns in our modules) in order to have a competitive solution. Lets say that low concentration has the worst of two worlds, instead of being the best compromise, as some people may think.
For instance, if we would use low concentration ratios using the same kind of materials we use (commodity PMMA and aluminum sheet), the material and assembly module costs would be more or less the same, except for the cells, but those don't contribute very much as their size is so small.
To give an idea, presently the cell cost is just 18 percent of our module cost. I am quite sure a low concentration silicium cell based approach would yield a similar cost module but with much lower efficiency. This is what I can say after my knowledge on the application.
Other than these three professionals quoted above, Steven D. White, president and CEO, SV Solar spoke about his company's operations with CPVToday.com in one of the previous conducted interviews. He came up with this response:
SV Solar intends to establish and maintain leadership in the LCPV technology class. This product and technology class is fundamentally distinct from high concentration (HCPV), which has great potential for cost reduction but also has a significant level of technology and market risk.
HCPV systems require multi-junction PV cells that can achieve very high efficiencies, (40 percent or better), but may cost up to 100 times more than a standard silicon solar cell. HCPV require sophisticated, very precise tracking systems and typically can only be utilized in geographies with a very low percentage of diffuse solar radiation. In order to address more than 80 percent of the available market, a concentrator technology must demonstrate adequate diffuse light performance.
Industry sources project average crystalline silicon cell cost to be $1.72/Wp in 2009, representing 76 percent of the average Cz based module cost of $2.25. Even taking into account optical losses, the Sol-X technology can reduce cell area by over 50 percent for equivalent Wp output. Factoring in the incremental cost of the optic and additional processing, a net cost reduction of over 25 percent per watt peak can be achieved. Since the concentration simply acts as a "multiplier", this cost reduction has the ability to scale with technology developments related to increased cell efficiency. This level of cost reduction is significant in the market given that it represents approximately two years of "learning curve". Historically the installed base of PV has doubled every two years while the cost of modules had dropped 19 percent.
Compared to HCPV and standard module technology, Sol-X is well positioned both in cost and deployment: Sol-X can be used in a static application that performs in diffuse light environments and is suitable for rooftop applications. Our optical design translates in lower mounting angles (-10-12°), resulting in area density advantage. From a cost position, we gain efficiencies due to the reduced silicon use and to the continuous increase in solar cell efficiency, both of which translate into sustainable advantages. We have modelled the impact of lower silicon prices on our production cost target over the next three years and we are confident in our ability to sustain healthy margins over time and in varying supply conditions.
CPV Summit 2009, San Diego
CPV Summit 2009 is scheduled to take place in San Diego (February 3-4, 2009). For more information, click here:
http://www.cpvtoday.com/usa/programme.shtml
or Contact: Joshua Bull by email josh@cpvtoday.com
Featured Product
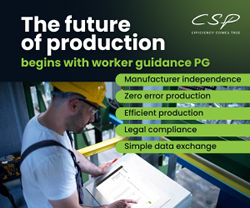
Quality assurance in the manufacturing industry
Efficiency and precision with CSP software. In the highly competitive world of manufacturing, quality assurance is a critical factor for success. CSP offers you state-of-the-art software solutions specifically designed to ensure the highest standards of quality assurance in the manufacturing industry.