ProMedica Wildwood Campus to cut energy usage with advanced heat and power system from GEM Energy
ProMedica has contracted with GEM Energy, of Walbridge, OH, to install and integrate one of the most advanced combined heat and power systems in the marketplace, using Capstone MicroTurbines® at its Wildwood Campus. The onsite power system will use natural gas to provide electricity and heat.
Toledo, OH - ProMedica has contracted with GEM Energy, of Walbridge, OH, to install and integrate one of the most advanced combined heat and power systems in the marketplace, using Capstone MicroTurbines®, at its Wildwood Campus in Toledo.
The onsite power system will use natural gas to provide electricity and heat to the hospital. The system is being installed on the hospital campus now and will be commissioned this summer.
The combined heat and power system will:
> Reduce the hospital's energy usage.
> Decrease the hospital's greenhouse gas emissions.
> Increase the campus's Energy Star score.
"Because healthcare facilities and hospitals need electricity and heat 24/7/365, they benefit tremendously from the energy efficiency and reliability that combined heat and power (CHP) systems provide," says Glenn Powers, energy efficiency manager, GEM Energy. "This system's compact size and low sound level make it a nice fit for our customer."
Other local combined heat and power systems GEM Energy has installed and integrated are located at the Toledo Museum of Art, The Huntington Center, SeaGate Convention Centre and The University of Toledo.
GEM Energy provides comprehensive energy services and technologies including energy management programs, distributed power generation systems, energy management controls and energy procurement strategies for commercial, institutional, industrial and mission critical facilities.
Featured Product
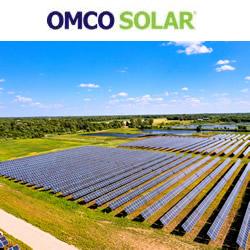
OMCO Origin® Factory-Direct Trackers
A One-In-Portrait (1P) solution for a wide range of solar projects within utility scale, distributed generation (DG), and community solar markets manufactured and factory preassembled in the USA at OMCO Solar with full-scale support, and design for quick, easy and safe installation, and fewer trackers per MW. OMCO makes all structural components with domestic steel and this balanced design allows for more accurate targeting and reduced energy consumption. OMCO Origin® Factory-Direct Trackers include universal module mounts with options for all commercially available modules, labor-saving bearings with 6 adjustable ways to compensate for posts and terrain issues, and foundation solutions for every terrain including OMCO C Piles.