Trendforce: Wafer Manufacturers Plan to Raise Prices in Face of Growing Polysilicon Costs
As prices of China's polysilicon spot market continue its upward ascend, it triggered price hikes in Asia's polysilicon market that in turn caused cost increases for wafer manufacturers.
Continual raw material price upticks are compressing silicon wafer manufacturers' profits. Under operation pressure, wafer manufacturers are also considering raising silicon wafer prices.
According to TrendForce, pointed out Chinese polysilicon market's continual price surge, which has shown no signs of decline, indicates a beneficial exterior environment for manufacturers operations. Therefore, price increases are unlikely to stop anytime soon. Although, the Chinese government has imposed anti-dumping duties on polysilicon imports in an attempt to increase the use of domestically produced polysilicon, Chinese polysilicon manufacturers product quality, costs, and shipment capacity still lags behind large international brands. As a result, there were no significant decreases in China's imports and purchase of raw materials. The industry still relies heavily on raw material imports. However, since China's polysilicon anti-dumping duties came into effect, the custom process period for imported raw materials has been extended. In addition, uncertainties surrounding future market development have caused suppliers to be rather passive in preparing raw materials. As a result prices in the polysilicon spot market remain high.
Besides these factors, from a current cost perspective there is still room for minor price adjustments. After EU and China reached a new agreement recently, module prices were at about €0.56/watt (US$ 0.74/watt) and has nearly become the base price used to calculate costs in the industry. By deducting module and cell manufacturing costs from this price, silicon wafer prices can be maintained at about US$ 0.3/watt. From a cost perspective, silicon wafer manufacturers still believe there is room for price adjustments. In general wafer manufacturers psychology tends to orient towards making up with price upticks since they believe they had not raised prices in the last price wave.
Featured Product
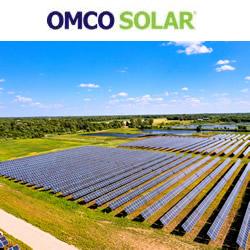
OMCO Origin® Factory-Direct Trackers
A One-In-Portrait (1P) solution that support a wide range of solar projects (utility scale, distributed generation (DG), & C&I markets). Manufactured and factory preassembled in the USA at one of OMCO Solar's 5 US plants (AZ, IN, AL, OH), OMCO makes all structural components with domestic steel and now can offer a 100% domestic tracker. OMCO Origin® Factory-Direct Trackers include universal module mounts with options for all commercially available modules, labor-saving bearings with 6 adjustable ways to compensate for posts and terrain issues, and foundation solutions for every terrain including OMCO C Piles.