Natcore's Black Silicon Technology Projected to Slash Solar Cell Production Costs by 23.5%
"Making plans to take our technology to market": Provini
RED BANK, N.J., Oct. 30, 2013 -- An independent study has concluded that Natcore Technology's (NXT.V; NTCXF.PK; 8NT) black silicon technology could reduce silicon solar cell production costs by up to 23.5%.
The savings derive from a streamlining of the production process whereby a silicon wafer is processed into a black silicon solar cell.
To make solar cells, manufacturers typically acquire silicon wafers from an outside source. Since these wafers are cut from a large ingot, they usually have saw damage, which must be removed. To make a conventional solar cell, manufacturers must first remove the saw damage, then texturize the wafer surface, and then apply an antireflective coating.
To make a black silicon cell using Natcore's proprietary process, manufacturers would be able to replace the texture etch with a black silicon etch which in itself would create a highly effective antireflective coating.
Thus the most expensive part of the solar cell process – the equipment and material costs associated with high-temperature chemical vapor deposition of a silicon nitride antireflective coating – is completely eliminated.
Natcore asked analysts at the country's leading black silicon research facility to quantify the cost saving to be realized from omitting these steps. Using a "bottom up" manufacturing cost estimating methodology, the analysts calculate the production cost of a conventional silicon solar cell to be 17 cents per watt. In comparison, the study projected that cells made using Natcore's black silicon process would cost about 13 cents per watt.
The resulting savings of 3 cents/watt – 4 cents/watt represent a production cost reduction of up to 23.5%. "When solar companies are scrambling to save fractions of a cent, a saving of 3 cents – 4 cents per watt is momentous," says Dr. Dennis Flood, Natcore's co-founder and Chief Technology Officer.
In addition to the dramatic cost reduction, Natcore's test, which was conducted using monocrystalline silicon, had an important environmental benefit: it eliminated the need for silane, a highly toxic gas that combusts upon exposure to air. Natcore may plan a similar test using polycrystalline silicon at a later date.
"We knew there would be a cost saving," says Chuck Provini, Natcore's president and CEO. "We were surprised that it was so large. In fact, production-cost savings of this magnitude will likely overshadow any power gains of black silicon and will make Natcore's technology a must-have for the world's solar cell manufacturers.
"To put it into perspective," he notes, "a recent article by Shyam Mehta, senior solar analyst of GTM Research ('Technology not materials to drive down Chinese solar costs,' August 2013), predicts that Chinese manufacturers will be able to cut prices by only one cent in the next year or so. We could quadruple those savings in one fell swoop. We feel so optimistic about this development that we've begun making plans to take our technology to market."
"The full cost of a solar cell is the sum of two parts: the cost of the silicon wafer and the cost of the processing steps required to turn the wafer into a working solar cell," says Flood. "Cell manufacturers have no control over the cost of the silicon wafers they buy. As a result they are always looking for ways to control their production costs, but with a very important caveat: cost cutting must not lower cell performance in any way. Natcore's black silicon processing technology results in solar cells that meet or exceed the industry's requirement and at the same time provide a spectacular reduction in finished cell cost. Natcore's technology can easily be retrofitted into existing solar cell production lines and can just as easily be incorporated into a new line. Black silicon seems poised to become the industry's standard approach."
Featured Product
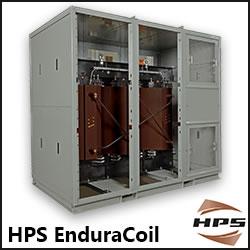
HPS EnduraCoilTM Cast Resin Medium Voltage Transformer
HPS EnduraCoil is a high-performance cast resin transformer designed for many demanding and diverse applications while minimizing both installation and maintenance costs. Coils are formed with mineral-filled epoxy, reinforced with fiberglass and cast to provide complete void-free resin impregnation throughout the entire insulation system. HPS EnduraCoil complies with the new NRCan 2019 and DOE 2016 efficiency regulations and is approved by both UL and CSA standards. It is also seismic qualified per IBC 2012/ASCE 7-10/CBC 2013. Cast resin transformers are self-extinguishing in the unlikely event of fire, environmentally friendly and offer greater resistance to short circuits. HPS also offers wide range of accessories for transformer protection and monitoring requirements.