BioConversion Solutions AFC2 MCG Units Selected for Daejeon, S. Korea Municipal Anaerobic Digester Retrofit
"The Daejeon project and several others in process represent major forward momentum for BCS and our technology,"
EXTON, Pa. — Daejeon, S. Korea is installing BioConversion Solutions' (BCS) Advanced Fluidized Co-Digestion and Co-Generation (AFC2) system to retrofit the City's anaerobic digester. The Daejeon system will utilize two BCS AFC2 MCG units to reduce a projected one billion pounds of sludge over three years, lower costs, and enhance overall performance. Biogas production at the Daejeon plant will be increased commensurate with increased solids destruction. Daejeon is the fifth largest city in S. Korea.
"The Daejeon project and several others in process represent major forward momentum for BCS and our technology," comments Dr. Alan Rozich, Chairman and CEO, BioConversion Solutions. "This solidifies BCS' leadership role in increasing affordable biomass conversion worldwide."
Representatives from the City of Daejeon, DOHWA Engineering (Seoul, S. Korea), and Pan Asia, BCS' Korean licensing partner, viewed the BCS MCG units last week prior to shipping. The equipment inspection, required by the City of Daejeon and DOHWA, took place at the factory of BCS' exclusive partner, Hockmeyer Equipment Company.
For more information visit http://www.bioconversionsolutions.com or call 610.524.6364.
About BioConversion Solutions, LLC
BioConversion Solutions, LLC (BCS) systems convert biomass to renewable energy and high-value byproducts including fertilizer and clean water using the industry's most advanced and efficient biotechnology processes. Led by Dr. Alan Rozich, the company's biokinetics-based systems approach delivers the highest profits in the industry and is scalable to customer specific needs across a variety of industries and applications. BCS is headquartered in Exton, Pennsylvania.
Featured Product
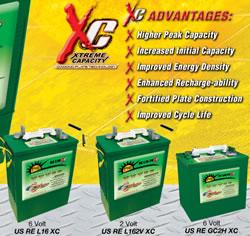