SolarBOS Now Offering Wire Harness Solutions
All wire harness assemblies are custom manufactured to client specifications, making any installation effective and cost efficient.
LIVERMORE, California (March 4, 2015) – SolarBOS is pleased to announce it has begun shipping wire harnesses and cable assemblies from its Grand Rapids, Michigan, facility, utilizing automated Schleuniger wire cutting, stripping, and labeling equipment. All wire harness assemblies are custom manufactured to client specifications, making any installation effective and cost efficient. Customers can choose from various American Wire Gauges (AWG) and jacket colors for the conductors, industry standard connectors, as well as custom labels at each connection point.
"We're pleased to have added this capability to our plant," said Ron Skorich, Production Manager, Grand Rapids, MI. "We believe this will help our customers to further streamline their projects and by tooling up we can help keep manufacturing jobs in the US."
SolarBOS Wire Harness solutions include over-molded "Y" harnesses with inline fuses, homerun cable assemblies, and combiner box whips, all of which can be customized in lengths, machine-labeled and/or bundled per customer wire schedules.
For more information about SolarBOS' Wire Harness Solutions, please visit http://www.solarbos.com/products/wire-harness-solutions.
To learn more about our products, please visit www.solarbos.com/products or contact sales@solarbos.com.
About SolarBOS
SolarBOS is a leading developer and manufacturer for balance of system products. The company's deep understanding of PV systems and experience in design and manufacturing help develop reliable and cost-effective solutions for their customers. In addition to providing a wide array of standard products, SolarBOS excels in providing custom solutions for integrators and designers alike. Founded in 2004, SolarBOS' headquarters are located in Livermore, California, with manufacturing locations in Livermore, CA, and Grand Rapids, MI.
Featured Product
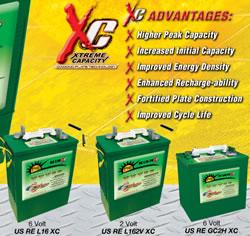