Morgan Advanced Materials announces expanded capabilities for producing ceramic pockets
Morgan Advanced Materials has expanded its capabilities for designing and manufacturing ceramic pockets, ideal for housing medical device electronics. Morgan's enhanced CNC machining capabilities allow the company to manufacture alumina ceramic pockets to higher tolerances and with reduced delivery
Morgan Advanced Materials has expanded its capabilities for designing and manufacturing ceramic pockets, ideal for housing medical device electronics. Morgan's enhanced CNC machining capabilities allow the company to manufacture alumina ceramic pockets to higher tolerances and with reduced delivery times. For extremely small medical devices that require thinner walls, Morgan produces higher strength yttria stabilized zirconia pockets using a ceramic injection molding process.
Successfully used in applications such as cochlear implants and other cranially implanted devices; Morgan's ceramic pockets feature excellent strength and radio frequency (RF) transparency, not possible with alternatives such as titanium. In addition, Morgan has invested in new machining technology that produces pockets with higher tolerances and reduced lead times.
The RF transparency found in these components is critical for device operations. RF transparency allows for more efficient recharging of implantable device batteries verses titanium casings. Devices with a titanium casing also need a larger device external antenna, requiring the device footprint to be larger. In addition, titanium can heat up during magnetic resonance imaging (MRI) scans, resulting in a risk of burning or the potential for device to malfunction.
Morgan can provide design services for both alumina and zirconia pockets, and work collaboratively with clients and component suppliers. The business has extensive in-house testing capabilities to ensure the required geometries and tolerances have been met.
Featured Product
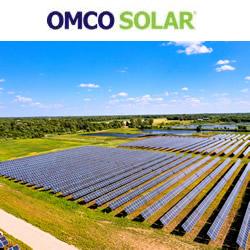