Konecranes' waste-to-energy technologies help unlock bioenergy potential
A broad range of lifting and materials handling technologies specifically designed for waste-to-energy (WTE) and biomass applications is being introduced to Australasia, India and China by Konecranes as the region develops its bioenergy potential.
The technologies - including unmanned full automation, remote operation stations, remote monitoring and maintenance reporting products - are focused on applications such as biomass, refuse and ash/slag.
Konecranes Australia National Industrial Equipment Manager, Mr Peter Monaghan says the WTE market has considerable growth potential because these technologies allow customers to save money and run their businesses in a more sustainable manner.
"Our WTE cranes can be equipped with Global Technical Support connection, remote monitoring and a computer interface capable of semi or fully unmanned automation or a remote for manual handling, as well as a range of features and benefits to maximise production and minimize running costs," said Mr Monaghan.
Konecranes waste handling cranes are designed with smart features, which manage critical crane functions to reduce structural stress, increase efficiency and prolong equipment life. For example, sway control minimises load sway from bridge and trolley motions, reducing collisions between the bucket and the pit walls or hopper, and preventing equipment damage. It increases operator confidence, reduces training time and allows the crane to operate to its full potential.
"As an industry leader in cranes and crane maintenance, with over 50 years experience in the waste and biomass handling applications, Konecranes is able to provide complete crane systems for the renewable energy industry," says Mr Monaghan. "Cranes play a crucial role in waste-to-energy as well as other modern incineration plants where tight environmental management guidelines are applied. A continuous material handling system with maximum safety and efficiency and minimum downtime is vital."
Remote Operation
Konecranes can replace entirely the crane operator pulpit chair and pulpit itself with a remote operators station or ROS which allows someone to operate the crane via cameras from a central operations room located in the facility. This ROS ensures all personnel are removed from harms way.
Konecranes Waste-to-Energy crane technology
Konecranes Biomass Handling Crane technologies recognise that many biomass energy plants today use cranes instead of front-end loaders or conveyors. Cranes need less energy, can operate unmanned in full automation, eliminate diesel fumes from inside your plant, and maximize your available floor space, just to name a few advantages.
Konecranes biomass handling cranes automatically start the working cycle to transfer the material from the reception pocket to the adjacent storage. Likewise, the crane automatically starts the working cycle to fill the hopper from the storage after the reception of the command "fill the hopper" from the sensor of the hopper.
The storage is managed by the crane. Every time crane deposits or picks up material, it updates the storage in that coordinate location. The same modular solutions used in Konecranes WTE cranes are applicable to Biomass Handling Cranes.
Konecranes refuse handling cranes are designed to meet the demanding loads of waste management plants, where minimal downtime is crucial. Important components like hoisting trolleys, drives and grapples have been engineered to reduce maintenance requirements.
Each crane features Konecranes advanced integrated rope/cable drum. The vertical power cable for the bucket is wound onto the rope drum and is driven by the hoisting machinery. With this unique solution, savings in maintenance costs are substantial.
Konecranes refuse plant cranes recognise the importance of a continuous material handling system, from the reception of the waste to mixing and feeding. If a waste handling crane stops, the whole process is in danger. Konecranes proprietary smart features manage critical crane functions to reduce structural stress, increase efficiency and prolong equipment life.
Sway Control minimizes load sway from bridge and trolley motions, reducing collisions between the grab and the pit walls or hopper, as well as preventing equipment damage. Sway Control increases operator confidence, reduces training time and allows the crane to operate to its full potential.
Konecranes ash (or slag) handling cranes are ruggedly designed for harsh environments. These cranes are used to distribute slag under the conveyor line to the other areas in the slag bunker 24 hours a day as well as loading trucks during the daytime. Sometimes the ferrous rejects have not been separated from the slag, causing higher requirements for the buckets.
To achieve better penetration into the slag, the edges of claws can be provided with special teeth.
The Konecranes Main User Interface, or MUI, is Konecranes new standard solution for programming waste-to-energy automation. Accessed from the MUI station, the MUI features a computer and 23-inch LED panel screen, keyboard and mouse. This computer is fully integrated with the cranes PLC system, while isolated from outside networks. It allows the operator to schedule and program a week-long agenda that includes up to 20 different work routines in full automation, giving plant managers enhanced flexibility to manage pit operations for receiving, mixing and burning waste.
In seasons where flexibility is not as important, facilities can repeat the Monday through Sunday agenda indefinitely without accessing the crane-except to take it out of automation for scheduled inspections and maintenance. In addition, the MUI monitors crane operations, including usage statistics, error messages and equipment condition. The system also generates summary reports to help managers optimize maintenance and alert them if more operator training is needed.
Konecranes waste-to-energy technologies include an extensive range of maintenance reducing software, electrical and mechanical products including TRUCONNECT® Remote Monitoring and Reporting.
Featured Product
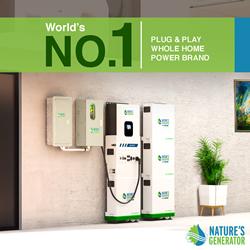
Nature's Generator MyGrid 10K
A 10,000W plug & play whole-home generator with a 10kWh LiFePO4 battery for reliable backup power. Features easy setup, flexible 120V/208-240V input, and solar/wind charging. Expandable with extra batteries or solar panels, and can pair two units for 20,000W for even larger energy needs. Powers your home during power outages, reduces electricity costs, and supports sustainable energy.