OFFSHORE WIND TURBINES: IMCA PUBLISHES STANDARDISED BOAT LANDING RESEARCH REPORT
The subject of developing a document on a standardised boat landing was identified by the International Marine Contractors Association's (IMCA) Renewable Energy Workgroup as one of the areas where there could be benefits, both in terms of cost reduction and safety improvement, for marine operations for renewable energy. The resulting publication ‘Standardised boat landing research report' (IMCA SEL 041/ M 232) has been released.
The subject of developing a document on a standardised boat landing was identified by the International Marine Contractors Associations (IMCA) Renewable Energy Workgroup as one of the areas where there could be benefits, both in terms of cost reduction and safety improvement, for marine operations for renewable energy.
Following this recommendation, IMCAs Renewable Energy Workgroup and the National Workboat Association (NWA) have been seeking a consensus on the optimum design and configuration of boat landings for accessing wind turbine foundations from crew transfer vessels (CTV). The resulting publication ‘Standardised boat landing research report (IMCA SEL 041/ M 232) has been released by IMCA
"In order to undertake this task, a questionnaire was issued to all the operators of European offshore wind farms to gather information on existing boat landing geometries. At the same time, feedback was sought on the experience of CTV operators, fender manufacturers and structure designers," explains IMCAs Technical Director, Richard Benzie.
"A significant volume of data and feedback was gathered. On analysis of the data it has been possible to develop a recommended geometry for a standard boat landing that is consistent with the G+ Global Offshore Wind Health & Safety Organisation (formerly G9) guidelines.
"One critical area where data was lacking was on the design impact forces for the boat landing This information was not as readily available as expected, with only two out of twenty-four projects originally being able to supply it. Looking in detail at how the design codes address impact loads, a number of areas of challenge and further research have been identified.
Based on the feedback, several other potential areas for research have been identified in our extensive document. It is now recommended that these are taken up by the relevant research bodies."
IMCA would particularly like to thank the following companies and groups for their support of this study and the information and feedback they have provided; Seaway Heavy Lifting and Subsea 7, and in particular Alan MacLeay, chairman of IMCAs Renewable Energy Workgroup.
The wide ranging document includes sections on crew transfer to offshore wind turbines; the questionnaire; data analysis; fender impact loading, safe clearances; as well as the executive summary, introduction, conclusion and recommendations.
IMCAs thanks
Industry associations and regulatory bodies: National Workboat Association, RenewableUK, WindEurope (formerly European Wind Energy Association); UK Health & Safety Executive; Carbon Trust; and G+ members, in particular Centrica Energy; DONG Energy; E.ON; SSE, Statoil, Statkraft, ScottishPower, RWE, Vattenfall and the Energy Institute.
Other offshore wind farm operators: ENBW, EWE, MindMW, Globaltechone, BARD, Belwind and Eneco; CTV operators: Windcat Workboats; Workships; Van Oord, Turbine Transfers; Maritime Craft Services (Clyde) Ltd; and James Fisher.
Siemens as an OEM; designers Atkins, LIC and OWEC Tower; and fender system suppliers RG Seasight and Fendercare.
Further information on IMCA
Further information on IMCA and its work on behalf of around 1,000 member companies in over 60 countries is available from www.imca-int.com and imca@imca-int.com. The association has LinkedIn and Facebook groups and its Twitter handle is @IMCAint
Featured Product
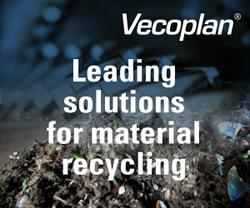