Cooperation between Bonfiglioli and Schaeffler: Predictive Maintenance for yaw drive gearboxes in Wind Turbines cuts operating costs in half
On the Bonfiglioli dashboard the operator can perform continuous control of the geared motor based on the data and consult an estimation of the remaining service life of the drive. Abnormal behavior of the azimuth drive is reported as are critical conditions.
A compact Industry 4.0 solution for wind turbine azimuth drives is the result from a long-term development partnership between Bonfiglioli and Schaeffler. Schaeffler Torque Sense and SmartCheck sensors record torque, speed, vibration and temperature information. These data are transmitted through a gateway, combined and processed using algorithms developed by Bonfiglioli and based on more than 60 years' know-how in gearmotors and dedicated specifically for the application. Subsequently, the data will be made available for the users on the Bonfiglioli Cloud platform. The Bonfiglioli Dashboard provides a clear overview of the collected information for the operator. Maintenance measures can be carried out in a load-oriented manner, unplanned system downtime can be minimized and operating costs can be cut in half.
On the Bonfiglioli dashboard the operator can perform continuous control of the geared motor based on the data and consult an estimation of the remaining service life of the drive. Abnormal behavior of the azimuth drive is reported as are critical conditions. Thus, maintenance intervals can be optimized to critical needs and necessary repairs can be made at favorable times. Additionally, drive control can be optimized to avoid overloading. Valuable results are a drastic reduction of unplanned downtime and significant increase in the profitability of a plant.
Concrete figures based on the example of a 2.3 megawatt wind turbine make this clear, as Gaetano Ciaravella, Bonfiglioli's Mechatronics & IoT Manager reported at a conference: Currently, the availability of a wind turbine is falling from 95% in the first year to 82% in the 20th year of life with a median of 88.5%. At the same time, the yields of a wind turbine are falling by about 7% per year due to lower kWh prices. The operating costs account for approximately 75% of the total initial investment across 20 years. About 50% of the operating and maintenance costs are attributable to unplanned interventions. Specifically, this means that for a 2.3 megawatt wind generator in 20 years operating costs of approximately €1.6 million are estimated, of which up to €1.1 million are due to unscheduled repair and maintenance. With a relatively small investment in the system from Bonfiglioli and Schaeffler, operating costs can be reduced by up to 60%.
There are certainly other advantages that are difficult to quantify due to the available data. They result from the possibility of adapting the electronic drives to environmental and operating conditions (eg temperatures, wind hours per year, etc.), which has a direct and positive effect on the productivity of the wind generator.
www.bonfiglioli.com
About Bonfiglioli:
Bonfiglioli is a worldwide designer, manufacturer and distributor of a complete range of gearmotors, drive systems, planetary gearboxes and inverters, which satisfy the most challenging and demanding needs in industrial automation, mobile machinery and renewable energy. The Group serves more industries and applications than any other drive manufacturer and is a market leader in many sectors; our three business units - Discrete Manufacturing & Process Industries, Mechatronic & Motion Systems and Mobility & Wind Industries - embody over 60 years' expertise and experience in the respective industries. Established in 1956, Bonfiglioli operates worldwide with 21 branches, 14 production facilities, a network of 550 distributors and about 3,770 employees. Excellence, innovation and sustainability are the drivers behind our growth as a company and team, and represent the guarantee of the product and service quality we offer our clients. More information available at www.bonfiglioli.com.
Featured Product
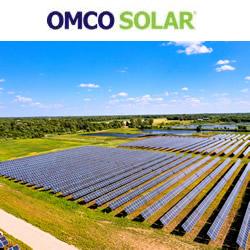