BLADE QUALITY, INDUSTRY 4.0 AND LEADING EDGE EROSION DISCUSSED AT AMI’S WIND TURBINE BLADE MANUFACTURE 2019 CONFERENCE
The conference will take place in Düsseldorf from 9th-11th December 2019
AMI, BRISTOL 4th September 2019 - The wind turbine blade industry continues to change as it grows. Top manufacturers and turbine makers will be discussing and presenting their latest developments at the 10th annual conference on Wind Turbine Blade Manufacture 2019, which will take place from 9th to 11th December 2019 at the Maritim Hotel in Düsseldorf, Germany. The conference will kick off as usual with a market analysis by Cristina de Santos, Energy & Infrastructure Unit Manager with AMI Consulting. Cost of energy is more important than ever, and Pontis Engineering will identify the main challenges in cost and CAPEX reduction in rotor blade design and manufacturing.
China continues to be the largest blade manufacturing country in the world and AMI is honoured to host again Sinoma Wind Power Blade the leading blade manufacturer in China, after the success of its first presentation in Europe at AMI's 2018 conference. This year, Sinoma's CTO Bart Roorda will share with delegates an overview of the main market trends in the Chinese market together with an introduction to next generation blade developments.
AMI is also proud to have the Sany Group, one of the leading global manufacturers of heavy equipment, as part of its conference programme. The wind energy arm of the Chinese giant set up in 2018 an innovation centre in Pamplona (Spain) and Marlon Rens will share with AMI's delegates an alternative to the design safety factors used on IEC standards and DNV GL guidelines.
Blade manufacturing and potential production efficiencies, the core focus of the conference, are fundamental when analyzing the cost of energy. The world's second-largest independent blade producer, TPI Composites, will share its latest developments in two very important processes within blade production; infusion and bonding. The longer the blade are, the more complex the manufacturing challenge, and therefore the more important the benefits of process optimisation. The challenges of manufacturing very long blades will be covered by Siemens Gamesa Renewable Energy (SGRE) using a 94m blade case.
The wind turbine blades industry has gone through an intense market consolidation process in recent years with a significant number of mergers and acquisitions involving key players. Revenue optimisation, greater supply control, complementing technologies, or regional expansion are some of the main drivers behind M&A activity in this market. However, such operations do not come without operational challenges. Nordex went through this process after merging with Acciona in 2016 and will share the company's approach to guarantee blade quality across the newly formed company across the globe.
Dr. Povl Brøndsted, a well-known expert in the wind blades composites market will again be one of the chairs of the conference. His commentary and questions will undoubtedly bring additional value to the Q&A time after technical presentations as that of Textechno Herbert Stein during which interfacial shear strength testing will be introduced as a key quality parameter in the control and R&D of GFRP.
Fraunhofer IFAM (Institute for Manufacturing Technology and Advanced Materials) will present an innovative technology intended to reduce the efforts required to ensure the undamaged demoulding of turbine blade half shells. In addition to the identification of the main benefits of this novel release film (e.g. clean surface of the cured blade), calculations on the potential of saved working and mould occupancy time will be presented.
Automation and Industry 4.0 have played a significant role in the development of other industries, and the wind turbine blade manufacturing market is not an exception with more and more progress being made on this front. Mr. Kenneth Lee Kaser, Head of Offshore Operations at Siemens Gamesa Renewable Energy will chair this conference session. Vestas, the global blade producer well-known for its continued focus on innovation, introduced the concept of blade design digitization on AMI's 2018 conference, which will be followed up this year. The German Aerospace Center (DLR) will share with delegates how live data analysis can increase process efficiency, reduce manufacturing defects and rework actions. This is possible thanks to the use of equipment such as thermographic cameras, thermocouples or infrared and laser systems that allow for online quality assurance through fibre angle detection, construction thickness measurement or leakage detection. Synthesites will also share with the audience how the implementation of industry 4.0 technologies can improve quality by avoiding over-curing while reducing energy consumption and production cycles.
However, leading edge erosion continues to be the most important challenge the wind energy industry still needs to overcome. Hence, it continues to be the focus of R&D efforts across the supply chain. AMI is proud to have key industry players such as DTU, LM Wind Power and Eire Composites covering such an important topic. Technical University of Denmark will introduce potential solutions to reduce erosion while Eire Composites will investigate protection measures. LM Wind Power's presentation will be focused on offshore wind turbines, where the risk of costs derived from leading edge erosion are the highest. This is one of the sessions that will be chaired by Sandro Di Noi, from Suzlon Energy.
Material innovation is another topic covered in this conference and there is no doubt adhesives are critical for blade performance. Gurit will cover, among other things, how requirements are changing in the industry and how is adhesive selection affected by an increased focus on HSE. ACT Blade will introduce a novel material which according to the company could not only reduce the weight and manufacturing costs of the blade but also reduce blade erosion and improve recyclability. Not only will adhesives and reinforcements be covered in AMI conference's "Materials" session but also resin, with Scott Bader introducing urethane acrylate as a potential alternative in pultruded spar caps. Innovation is also happening in materials used in prevailing fibreglass blades and Owens Corning will introduce its hybrid glass-carbon unidirectional fibres. Hybrid blades have indeed proven to be a solution for the industry to manufacture longer blades while keeping cost and weight down and material developments such as this one are expected to further enhance their benefits.
The final session will mirror that of previous events, with blades' life in service and their posterior recycling dominating the discussion. Fraunhofer IWES (Institute for Wind Energy Systems), will introduce the digital twin concept in the blades market, which helps predict the future state of each blade individually during its entire life cycle based on automated condition monitoring, multiscale modelling and virtual testing. Conenor will identify added-value re-manufacturing opportunities using GFRP waste. Not only will test results be shared with the audience but also market size information for those alternatives.
The full programme can be found on AMI's website: www.amiconferences.com.
Featured Product
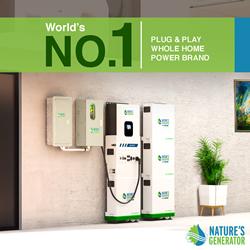