AFC Cable Systems® Liquid Tight Conduit Designed to Withstand Extreme Temperatures
Hi-Low Temperature LFMC properties ensure the protection of the conductors
New Bedford, MA -The performance of conduit depends on its application and operating temperature. When used in an environment of extreme temperature, conduit not suited for these conditions may have shortened service life due to degradation of the material. Thorough testing—including low temperature flexibility, cold bend, cold impact, sunlight resistance, and other physical property testing—should be done to determine the appropriate operating temperature range for the conduit to ensure product integrity.
AFC Cable Systems® Hi-Low Temperature LFMC have been tested to withstand temperatures from -55°C/-67°F to 105°C/221°F in dry conditions, and 60°C/140°F in wet conditions, and up to 70°C/158°F oil resistance. The following Hi-Low Temperature LFMC properties ensure the protection of the conductors:
PVC Jacket
A moisture-, oil-, and sunlight-resistant polyvinyl chloride (PVC) jacket is applied directly over a zinc-coated galvanized low carbon steel core and allows the conduit to be rated for wet locations, which is essential if the conduit is intended for outdoor use and exposed to the elements. Additional wet locations may include warehouses or environments with exposure to condensation, sprinkler systems, and more.
Grounding
LFMC is permitted to serve as an equipment ground by NEC 250.118(6)
Industry Compliant
AFC Cable's LFMC is Listed to Underwriters Laboratories Standard for Safety UL 360 and is compliant with all construction and performance requirements. LFMC complies with and is permitted for use in accordance with the National Electrical Code NEC.
Size Range
Available in trade sizes ranging from 3/8" to 4" and comes in standard gray, however, additional color options are available upon request. AFC marks the surface of the outer jacket with a legend in compliance with UL 360.
Featured Product
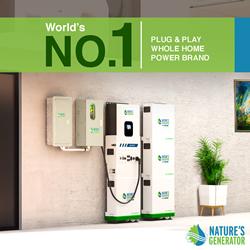