CASE STUDY: Venair-Ballard collaboration for marine fuel cell hoses
Silicone hose manufacturer Venair has teamed up with Ballard Power Systems to help the marine industry implement fuel cell systems to decarbonise shipping. As part of a recent development project, Venair supplied Ballard with custom hoses to allow the transportation of hydrogen from the fuel tank to the fuel cell engine. The hoses had to be adapted to the location and position of the engine, the opening in multiple hoses for the engine inlets, the operating temperature, the specific pressure, pressure control, product control etc. In order to deliver the requirements, Venair worked together with Ballard to find the best solution and used its Vitosil product to meet the needs in the hydrogen passage. "For the conduction of any gas, an extremely low permeability hose is needed so that the gas does not pass through the hose wall and escape. In this case, we use our product Vitosil." Venair explained in a statement. "Our Vitosil product is composed of Fluorocarbon (FKM) inner layer. FKM inner layer presents a high chemical compatibility with the conducted products, as well as its extremely low permeability which allows the passage of gases without leakage loss through the material."
CASE STUDY: Venair-Ballard collaboration for marine fuel cell hoses
Executive Summary
For the development of the project, Ballard relied on Venair to ensure the best transfer solutions. Ballard needed custom hoses that adapt to their systems that present maximum purity to achieve the highest efficiency.
In this case study we explain the following solutions provided:
• Anode side hoses that comply with the most demanding hydrogen transfer requirements.
• Cathode side hoses to provide the highest purity.
• Custom solutions to provide maximum efficiency and project optimization.
The project
In this project, Ballard needed to provide fuel cell systems for marine vessels. Fuel cells generate DC power compatible with modern ship electric and hybrid architectures and may be deployed in parallel, dispatchable configurations to meet variable power requirements of vessels.
The technology
Ballard fuel cells are a zero-emission, high efficiency, low maintenance, scalable source of electric power, and it is expected that they will be an important solution for achieving the emissions reduction required by the marine industry. Ballard fuel cells have already demonstrated the operation of, without replacement or rebuild of the stack, more than 30,000 hours in heavy-duty transit applications, and are deployed in difficult environments from desert to coldest regions.
The challenge
Fuel Cell technology uses electrochemical energy instead of combustion energy (as current engines do). To do so, Fuel Cell engines need by one hand Hydrogen and by the other hand Air. The fuel cells provide energy to power any transport, and the only waste is water vapor and some heat.
However, this technology requires maximum purity to ensure the highest efficiency in the Fuel Cells engines. As lower the Hydrogen and air pureness, as lower the efficiency.
These, very specific needs, imply very demanding technical requirements to ensure the most optimized solution.
The requirements
To consider the needs of hoses, there are three basic but important questions to ask:
1. What product is to be conveyed?
2. At what temperature? Internal and external?
3. At what pressure is the product-driven?
At the first stage, we analyze the project and we validate that all the basic requirements were effectively fulfilled as our standard products already met these technical specifications.
Solutions
1. Product to convey: Vena Fuel Cells specifically developed for extremely low permeability for the passage of hydrogen gas and a maximum purity of the material so that it does not contaminate the cell.
Vitosil: FKM inner layer to minimize permeability and ensure the lowest possible volatiles.
2. Temperature resistance: PEMFCs are low-temperature Fuel Cells, so they usually operate at temperatures between 40ºC and 110ºC. Our hoses perfectly comply with these temperatures and up to 220ºC.
3. Pressure resistance: Pressure requirements are not usually very high in PEMFC, but even if necessary, our products can withstand high pressures by adding reinforcements and braided fabrics, as well as stainless steel or plastic spirals if necessary.
Then, we met with Ballard engineers to discuss the exceptional specifications to meet this customized fuel cell project requirements:
• Convey hydrogen in gaseous state (Critic gas)
• Fuel cells are extremely low tolerant to contaminant volatiles.
• Comply with the DNV-GL certifications for fuel cells for marine use.
Hydrogen hoses for Fuel Cells
Hoses for Anode side
Ballard needed to be provided with specific hoses to transport the hydrogen from the fuel tank to the Fuel Cell engine.
These hoses must be adapted to the location and position of the engine, the opening in multiple hoses for the engine inlets, the operating temperature, the specific pressure, pressure control, product control...
To solve all the aspects Venair worked together with Ballard to find the best solution to the specific requirements of this Fuel Cells technology.
We used our Vitosil product to meet the requirements in the hydrogen passage. To conduct the hydrogen, in its gaseous state, is required:
Assuring the lowest Permeability
For the conduction of any gas, an extremely low permeability hose is needed so that the gas does not pass through the hose wall and escape.
In this case, we use our product Vitosil. Our Vitosil product is composed of
Fluorocarbon (FKM) inner layer. FKM inner layer presents a high chemical compatibility with the conducted products, as well as its extremely low permeability which allows the passage of gases without leakage loss through the material.
As an alternative, it is also possible to use material Vena Fuel Cells: an elastomer composite especially designed for use in Fuel Cells that allows lower permeability than the moderate permeability of silicone, but without losing the high flexibility and high purity of silicone.
The lowest possible contamination
Both the FKM used as inner material and our specific hoses for Fuel Cells are specifically designed to expel few volatiles as possible so that they do not contaminate the fuel cell membranes and therefore do not affect the efficiency of the Fuel Cell at all.
The use of high purity and quality in raw materials in Vena Fuel Cells and Vitosil ensures the ultra-low content of leachable substances and component inertness in the fuel Cell environment.
Air hoses for Fuel Cells
Hoses for Cathode side
To achieve the electrochemical reaction of the fuel cell, air must enter from the other side of the membrane (Cathode Side hoses).
As with the hydrogen hoses, the tubes for the air conduction had to meet different requirements specific to the situation and working characteristics. To meet these requirements, we used Sil 200/USP.
High level of cleanliness and purity
Vena sil 200 USP is a product manufactured with an inner layer of Platinum cured silicone (FDA, USP, BfR compliance) and an outer layer of VMQ silicone together with braided polyester.
The high purity of the inner layer allows the entry of oxygen with the minimum possible leachables so that the proton exchange membrane of the PEMFC (Proton Exchange Membrane Fuel Cell) is not contaminated.
In parallel, as Ballard works with PEMFC, the fuel cell membranes need to be regularly humidified to maintain good performance. On the other hand, hoses are also needed for the passage of DI Water for the cooling functions of the engine. For that, they needed a DI Water feed system to supply water to the Fuel Cells engine.
For the DI Water supply to the PEMFCs, high purity hoses is required, so we solved the problem with the product Sil 200/USP (USP, FDA, BfR compliance). This product provided them with a high purity solution that also allowed them to use it in situations of high flexibility and high temperatures.
Results and plans
We can conclude that as a company it has been an excellent opportunity and challenge to work with one of the leading companies in the transition to clean energy.
Ballard, with its cutting-edge fuel cell technology, is increasingly positioning itself as one of the companies that will have the greatest impact on the global ecological transition.
At Venair, we've already worked on several Ballard projects and we continue an ongoing relationship to improve and work to solve their challenges to make the world a greener place.
Today we are working together with the major players in the industry to be part of the development of this new technology. Certifying our products to achieve the highest standards and accredit the high quality of our products.
Featured Product
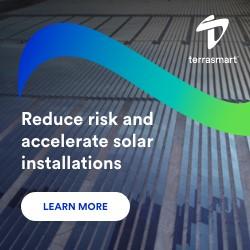