Worley awarded FEED for Queensland’s largest renewable hydrogen project
Commercial operations are expected to start in 2028. If successful, the project will ramp up in future phases to full-scale operation of approximately 2,240 MW electrolysers producing 800 tonnes per day of gaseous renewable hydrogen by 2031.
Worley, a global project delivery and asset services provider has been appointed by Stanwell Corporation Limited and its consortium members; Iwatani Corporation, Kansai Electric Power Company, Marubeni and Keppel Infrastructure, to undertake Front End Engineering Design (FEED) work for the Central Queensland Hydrogen (CQ-H2) Project.
The CQ-H2 Project represents the largest investment in an Australian renewable hydrogen project to date and also ranks in the global top 10 hydrogen projects at the pre-FID stage. The project initially plans to install up to 640 MW of electrolysers and produce up to 200 tonnes per day of gaseous renewable hydrogen, with offtakers purchasing the gas to convert to renewable ammonia or liquified hydrogen.
As Queensland's largest renewable hydrogen project, the project aims to deliver renewable hydrogen via its different carriers, to Japan and Singapore, as well as supplying large domestic customers in Central Queensland.
"We are proud to be supporting this world-scale project within the Gladstone region where Worley have remained invested through our local operation for the last 25 years. The Central Queensland Hydrogen Project is a landmark project, set to propel Stanwell's operations, the Gladstone region and Queensland as a whole into a leading exporter of green energy." Said Gillian Cagney, President Australia & New Zealand for Worley.
The project is backed by funding from all consortium members, the Australian Renewable Energy Agency (ARENA) and the Queensland Government's Queensland Renewable Energy and Hydrogen Jobs Fund. At its peak CQ-H2 is expected to support more than 8,900 new jobs, deliver $17.2 billion in hydrogen exports and add $12.4 billion to Queensland's Gross State Product over its 30-year life.
At the Front End Engineering and Design investment signing, Chief Executive Officer of Stanwell Corporation Michael O'Rourke said.
"The advancement of this important hydrogen project is great news for Central Queensland, where the project could create thousands of jobs and deliver billions of dollars in economic benefit".
Worley worked on the project in the role of technical advisor during the initial feasibility study and is now scoped to provide the FEED study for the Hydrogen Production Facility (HPF) and Hydrogen Transfer Facility (HTF), along with the pre-FEED study for the Hydrogen Liquefaction Facility (HLF).
Cagney further stated, "We will be bringing together our local and global hydrogen technical expertise along with our breadth of services, spanning multi-discipline engineering, ports and infrastructure capability, sustainability and environmental services and our in-house construction and commissioning expertise.
"Our work with Stanwell to date demonstrates our unique ability to support projects right from early concept studies into front end design, and we are looking to continue that support post-FID into the execution stage" says Cagney. "The project is aligned to our purpose of delivering a more sustainable world and is pivotal to the decarbonisation goals within our home region."
Featured Product
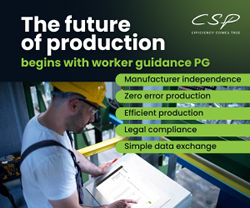