Among the different types of fuel cells, the PEMFC is more advantageous because of its operation condition. To satisfy the world energy thirst an integrated hydrogen production system and utilization unit must be developed.
Studies on Ideal and Actual Efficiency of Solar Polymer Electrolyte Fuel Cell
Rishabh Jain, Biswajit Mandal | Haldia Institute of Technology
Among the different types of fuel cells, the PEMFC is more advantageous because of its operation condition. To satisfy the world energy thirst an integrated hydrogen production system and utilization unit must be developed. |
Studies on Ideal and Actual Efficiency of
Solar Polymer Electrolyte Fuel Cell |
Rishabh Jain, Biswajit Mandal Haldia Institute of Technology, Department of Chemical Engineering |
Abstract The advance building of solar PEM fuel cell system project is focused on developing a fully integrated solar hydrogen production system and fuel cell operation. Hydrogen was produced by splitting of water using renewable solar energy, is the fuel for PEMFC. The feasibility of this project depends on the hydrogen production efficiency and fuel cell performance. Splitting of water using electricity from solar cell is a promising avenue and improvement of splitting efficiency using membrane is also shows positive steps. An atomistic modeling effort was added to this project in order to establish a frame work between predicted morphology and observed PEM morphology in order to relate it to fuel cell performance. Significant progress was made in the area PEM material design; development in this project. The purpose of this project was to initiate the fundamental research necessary for development of an integrated hydrogen production system and fuel cell to overcome the material and performance limitations of the 'state of the art' Nafion that is used in hydrogen fuel cell.
Key words: solar hydrogen, water splitting, PEMFCIntroduction Fuel cells are electrochemical devices that convert chemical energy in fuels into electrical energy directly, promising power generation with high efficiency and low environmental impact [1]. Because the intermediate steps of producing heat and mechanical work typical of most conventional power generation methods are avoided, fuel cells are not limited by thermodynamic limitations of heat engines such as the Carnot efficiency. In addition, because combustion is avoided, fuel cells produce power with minimal pollutant. However, unlike batteries the reductant and oxidant in fuel cells must be continuously replenished to allow continuous operation. Fuel cells bear significant resemblance to electrolyzers. In fact, some fuel cells operate in reverse as electrolyzers, yielding a reversible fuel cell that can be used for energy storage. Though fuel cells could, in principle, process a wide variety of fuels and oxidants, of most interest today are those fuel cells that use common fuels (or their derivatives) or hydrogen as a reductant, and ambient air as the oxidant. Most fuel cell power systems comprise a number of components:
In the following, an overview of fuel cell technology is given according to each of these categories, followed by a brief review of key potential applications of fuel cells. Unit cells Unit cells form the core of a fuel cell. These devices convert the chemical energy contained in a fuel electrochemically into electrical energy. The basic physical structure, or building block, of a fuel cell consists of an electrolyte layer in contact with an anode and a cathode on either side. A schematic representation of a unit cell with the reactant/product gases and the ion conduction flow directions through the cell is shown in Figure 1. Fig.1. Schematic of an individual fuel cell In a typical fuel cell, fuel is fed continuously to the anode (negative electrode) and an oxidant (often oxygen from air) is fed continuously to the cathode (positive electrode). The electrochemical reactions take place at the electrodes to produce an electric current through the electrolyte, while driving a complementary electric current that performs work on the load. Although a fuel cell is similar to a typical battery in many ways, it differs in several respects. The battery is an energy storage device in which all the energy available is stored within the battery itself (at least the reductant). The battery will cease to produce electrical energy when the chemical reactants are consumed (i.e., discharged). A fuel cell, on the other hand, is an energy conversion device to which fuel and oxidant are supplied continuously. In principle, the fuel cell produces power for as long as fuel is supplied. Fuel cells are classified according to the choice of electrolyte and fuel, which in turn determine the electrode reactions and the type of ions that carry the current across the electrolyte. Appleby and Foulkes [2] have noted that, in theory, any substance capable of chemical oxidation that can be supplied continuously (as a fluid) can be burned galvanically as fuel at the anode of a fuel cell. Similarly, the oxidant can be any fluid that can be reduced at a sufficient rate. Though the direct use of conventional fuels in fuel cells would be desirable, most fuel cells under development today use gaseous hydrogen, or a synthesis gas rich in hydrogen, as a fuel. Hydrogen has a high reactivity for anode reactions, and can be produced chemically from a wide range of fossil and renewable fuels, as well as via electrolysis. For similar practical reasons, the most common oxidant is gaseous oxygen, which is readily available from air. For space applications, both hydrogen and oxygen can be stored compactly in cryogenic form, while the reaction product is only water. Fuel cell stacking For most practical fuel cell applications, unit cells must be combined in a modular fashion into a cell stack to achieve the voltage and power output level required for the application. Generally, the stacking involves connecting multiple unit cells in series via electrically conductive interconnects. Different stacking arrangements have been developed, which are described below. Fuel cell systems In addition to the stack, practical fuel cell systems require several other sub-systems and components; the so-called balance of plant (BoP). Together with the stack, the BoP forms the fuel cell system. The precise arrangement of the BoP depends heavily on the fuel cell type, the fuel choice, and the application. In addition, specific operating conditions and requirements of individual cell and stack designs determine the characteristics of the BoP. Still, most fuel cell systems contain:
Fuel cell types A variety of fuel cells are in different stages of development. The most common classification of fuel cells is by the type of electrolyte used in the cells and includes 1) polymer electrolyte fuel cell (PEFC), 2) alkaline fuel cell (AFC), 3) phosphoric acid fuel cell (PAFC), 4) molten carbonate fuel cell (MCFC), and 5) solid oxide fuel cell (SOFC). Broadly, the choice of electrolyte dictates the operating temperature range of the fuel cell. The operating temperature and useful life of a fuel cell dictate the physicochemical and thermomechanical properties of materials used in the cell components (i.e., electrodes, electrolyte, interconnect, current collector, etc.). Aqueous electrolytes are limited to temperatures of about 200 °C or lower because of their high vapor pressure and rapid degradation at higher temperatures. The operating temperature also plays an important role in dictating the degree of fuel processing required. In low-temperature fuel cells, all the fuel must be converted to hydrogen prior to entering the fuel cell. In addition, the anode catalyst in low temperature fuel cells (mainly platinum) is strongly poisoned by CO. In high-temperature fuel cells, CO and even CH4 can be internally converted to hydrogen or even directly oxidized electrochemically. Table1 provides an overview of the key characteristics of the main fuel cell types. Table 1. Summary of major fuel cell types. The electrolyte in this fuel cell is an ion exchange membrane (fluorinated sulfonic acid polymer or other similar polymer) that is an excellent proton conductor. The only liquid in this fuel cell is water; thus, corrosion problems are minimal. Typically, carbon electrodes with platinum electrocatalyst are used for both anode and cathode and with either carbon or metal interconnects. Water management in the membrane is critical for efficient performance; the fuel cell must operate under conditions where the by-product water does not evaporate faster than it is produced because the membrane must be hydrated. Because of the limitation on the operating temperature imposed by the polymer, usually less than 100 °C, but more typically around 60 to 80 °C. , and because of problems with water balance, a H2-rich gas with minimal or no CO (a poison at low temperature) is used. Higher catalyst loading (Pt in most cases) than that used in PAFCs is required for both the anode and cathode. Extensive fuel processing is required with other fuels, as the anode is easily poisoned by even trace levels of CO, sulfur species, and halogens. PEFCs are being pursued for a wide variety of applications, especially for prime power for fuel cell vehicles (FCVs). As a consequence of the high interest in FCVs and hydrogen, the investment in PEFC over the past decade easily surpasses all other types of fuel cells combined. Although significant development of PEFC for stationary applications has taken place, many developers now focus on automotive and portable applications. Advantages: The PEFC has a solid electrolyte which provides excellent resistance to gas crossover. The PEFC's low operating temperature allows rapid start-up and, with the absence of corrosive cell constituents, the use of the exotic materials required in other fuel cell types, both in stack construction and in the BoP is not required. Test results have demonstrated that PEFCs are capable of high current densities of over 2 kW/l and 2 W/cm2. The PEFC lends itself particularly to situations where pure hydrogen can be used as a fuel. Disadvantages: The low and narrow operating temperature range makes thermal management difficult, especially at very high current densities, and makes it difficult to use the rejected heat for cogeneration or in bottoming cycles. Water management is another significant challenge in PEFC design, as engineers must balance ensuring sufficient hydration of the electrolyte against flooding the electrolyte. In addition, PEFCs are quite sensitive to poisoning by trace levels of contaminants including CO, sulfur species, and ammonia. To some extent, some of these disadvantages can be counteracted by lowering operating current density and increasing electrode catalyst loading, but both increase cost of the system. If hydrocarbon fuels are used, the extensive fuel processing required negatively impacts system size, complexity, efficiency (typically in the mid thirties), and system cost. Finally, for hydrogen PEFC the need for a hydrogen infrastructure to be developed poses a barrier to commercialization. Cell efficiency The thermal efficiency of a fuel conversion device is defined as the amount of useful energy produced relative to the change in enthalpy, ∆H, between the product and feed streams. η = Useful Energy/ ∆H Conventionally, chemical (fuel) energy is first converted to heat, which is then converted to mechanical energy, which can then be converted to electrical energy. For the thermal to mechanical conversion, a heat engine is conventionally used. Carnot showed that the maximum efficiency of such an engine is limited by the ratio of the absolute temperatures at which heat is rejected and absorbed, respectively [3]. Fuel cells convert chemical energy directly into electrical energy. In the ideal case of an electrochemical converter, such as a fuel cell, the change in Gibbs free energy, ∆G, of the reaction is available as useful electric energy at the temperature of the conversion. The ideal efficiency of a fuel cell, operating reversibly, is then ηideal = ∆G/ ∆H The most widely used efficiency of a fuel cell is based on the change in the standard free energy for the cell reaction: H2 + ˝O2 → H2O (l) given by: ∆Gor = GoH2O(l) - GoH2 - (0.5) GoO2 Where the product water is in liquid form. At standard conditions of 25°C (298°K) and 1 atmosphere, the thermal energy (∆ H) in the hydrogen/oxygen reaction is 285.8 kJ/mole, and the free energy available for useful work is 237.1 kJ/mole. Thus, the thermal efficiency of an ideal fuel cell operating reversibly on pure hydrogen and oxygen at standard conditions is: ηideal = 237.1/285.8 =0.83 For other electrochemical reactions, different ideal efficiencies apply. Curiously, for direct electrochemical oxidation of carbon ∆ G is larger than ∆ H, and consequently the ideal efficiency is slightly greater than 100% when using this definition of ideal efficiency. For convenience, the efficiency of an actual fuel cell is often expressed in terms of the ratio of the operating cell voltage to the ideal cell voltage. As will be described in greater detail in the sections following, the actual cell voltage is less than the ideal cell voltage because of losses associated with cell polarization and ohmic losses. The thermal efficiency of a hydrogen/oxygen fuel cell can then be written in terms of the actual cell voltage:
η = Useful Energy = Useful
Power = Voltsactual x Current = (0.83) (Vactual) As mentioned previously, the ideal voltage of a cell operating reversibly on pure hydrogen and oxygen at 1 atm pressure and 25şC is 1.229 V. Thus, the thermal efficiency of an actual fuel cell operating at a voltage of Vcell, based on the higher heating value of hydrogen, is given by η = 0.83 x Vcell/Eideal = 0.83 x Vcell/1.229 = 0.675 x Vcell The foregoing has assumed that the fuel is completely converted in the fuel cell, as is common in most types of heat engines. This efficiency is also referred to as the voltage efficiency. However, in fuel cells, the fuel is typically not completely converted. To arrive at the net cell efficiency, the voltage efficiency must be multiplied by the fuel utilization. An excellent review of the impact of this phenomenon is provided by Winkler[4]. Because the reactant activities in gas-fueled fuel cells drop as the utilization rises, and because the cell voltage cannot be higher than the lowest local potential in the cell, utilization considerations further limit the efficiency. Figure 2-2 shows the impact of fuel utilization on the Nernst voltage, voltage efficiency, and maximum overall cell efficiency for operating conditions typical for an SOFC (800 °C, 50% initial hydrogen concentration). Figure 2 shows that to achieve 90% fuel utilization, the Nernst voltage drops by over 200 mV. As a consequence, the maximum cell efficiency (on a higher heating value basis) is not 62%, as predicted based on the ideal potential, but 54%. Of course, practical cell operating effects and cell non-idealities further reduce this efficiency in real life. These effects are somewhat less profound at lower operating temperatures, such as those found in lower temperature SOFC, MCFC, or in low-temperature fuel cells. Actual Performance The actual cell potential is decreased from its ideal potential because of several types of irreversible losses, as shown in Figure 3. These losses are often referred to as polarization, overpotential or overvoltage, though only the ohmic losses actually behave as a resistance. Multiple phenomena contribute to irreversible losses in an actual fuel cell arel:
In the V-I diagram, especially for low-temperature fuel cells, the effects of the three loss categories are often easy to distinguish, as illustrated in Figure 3. In high-temperature fuel cells, the activation-related losses are often much less significant, and hence the characteristic concave portion of the V-I curve is hard to distinguish. In addition, as transport-related losses play a more important role, the convex portion of the curve often extends further to the left. Although it is tempting to characterize all losses in the cell as an equivalent resistance, only the ohmic losses actually behave that way, by definition. The ohmic loss depends only on cell geometry, the materials used, and the operating temperature. The other losses depend strongly on reactant concentrations (and hence fuel utilization) and thus they change within cells operated at finite fuel utilization. Attempts to include these types of polarization into the cell resistance more often than not lead to confusion and misinterpretation. This consideration has several ramifications for fuel cell engineers attempting to utilize single-cell data for stack or system design.
Experimental procedure In the present investigation hydrogen used as the fuel for PEMFC produced from the solar water splitting. Though the water splitting is thermodynamically unfavorable process but it may be techno-economically viable if solar energy used instead of grid power. The hydrogen was passed through the purification section and channeled through the fuel cell. Fuel cell study is the part of an integrated hydrogen production and utilization system. Solar energy was collected through photo voltaic cell and store as the hydrogen energy; again hydrogen energy converts to the electrical energy by PEMFC. As there are no rotating parts involves in the system so the mechanical damage as well as friction losses are absent. Conclusion Among the different types of fuel cells, the PEMFC is more advantageous because of its operation condition. To satisfy the world energy thirst an integrated hydrogen production system and utilization unit must be developed. The extensive research and awareness can overcome the present barrier of the sustainable energy production and utilization system. References [1]: "Fuel cell handbook", EG&G Technical Services, Inc, U.S. Department of Energy Office of Fossil Energy, National Energy Technology Laboratory [2]: A.J. Appleby, F.R. Foulkes, Fuel Cell Handbook, Van Nostrand Reinhold, New York, NY, 1989. [3]: "Fuel Cell Handbook," J. Appleby and F. Foulkes, Texas A&M University, Van Nostrand Reinhold, New York (out of print), republished by Krieger Publishing Co., Melbourne, FL, 1989. [4]: Winkler, W., Thermodynamics, in High Temperature Solid Oxide Fuel Cells: Fundamentals, Design and Applications, S.C. Singhal and K. Kendall, Editors. 2003, Elsevier Ltd.: Oxford, UK. p. 53 - 82. |
|
The content & opinions in this article are the author’s and do not necessarily represent the views of AltEnergyMag
Comments (0)
This post does not have any comments. Be the first to leave a comment below.
Featured Product
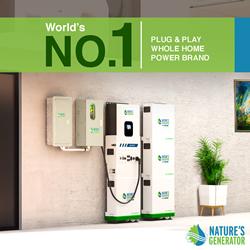