Although they invested a little more capital in the installed system, the annual energy cost savings will finance the extra capital and the system will pay itself back in the next 6-8 years. In addition, they have become one of the most environmentally responsible owners in the area with an annual emissions offset equal to planting an acre of trees.
Case Study - Geothermal Energy System
GeoSmart Energy | GeoSmart Energy
Although they invested a little more capital in the installed system, the annual energy cost savings will finance the extra capital and the system will pay itself back in the next 6-8 years. In addition, they have become one of the most environmentally responsible owners in the area with an annual emissions offset equal to planting an acre of trees. |
Case Study - Geothermal Energy System |
GeoSmart Energy |
When Scott & Vi began planning an interior renovation to their raised bungalow near Milton Ontario, they knew they wanted a heating and cooling system that was quiet, comfortable and energy efficient. They also wanted to enjoy the panoramic views of the escarpment from their beautiful new deck without the rattling noise of an outdoor air conditioner. Like many other homeowners in the area, they had a few choices available for heating and cooling their home. They had previously been using propane but the heating costs were becoming astronomical. Oil was an option but the estimated operating costs with that fuel were not that much better. This was an opportunity to make a change and Geothermal was the answer. Both Scott and Vi understood the concept of geothermal heating and cooling and knew it made economic sense. Benefits included low operating costs, little or no maintenance, virtually no noise and a system that provided 100% of their heating and cooling needs. In Ontario, the benefits of the system also include a significant reduction in greenhouse gas emissions which was also a driving factor behind their decision as they wanted to become more environmentally responsible. Ultimately, the system design incorporated about 2500’ of green vertical closed loop piping in the form of 7 holes that were drilled about 180’ deep each. All 7 holes were then filled with bentonite grout to enhance the thermal conductivity and increase heat transfer. Inside a GeoSmart EW020 water to water ground source heat pump provides 100% of the hot water for infloor heating in the foyer/entry area and ensuite as well as to the towel warmer racks located in the lower level bathroom. A separate E072 two-stage geothermal unit distributes forced air to all other areas of the home that are not heated using infloor tubing.
Highlights Type of Home: Raised Bungalow with Large Addition. |
|
The content & opinions in this article are the author’s and do not necessarily represent the views of AltEnergyMag
Comments (0)
This post does not have any comments. Be the first to leave a comment below.
Featured Product
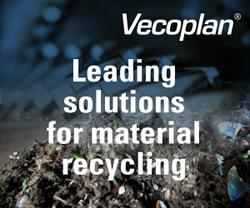