It is a fact that the installation and set-up of solar thermal systems is no longer the realm of rare solar enthusiasts.
SIMPLE AND SAFE SOLAR HEATING
Stefan Thiesen | Wagner & Co Solartechnik GmbH
It is a fact that the installation and set-up of solar thermal systems is no longer the realm of rare solar enthusiasts. |
Stefan Thiesen, Ph.D. Wagner & Co Solartechnik GmbH |
The content & opinions in this article are the author’s and do not necessarily represent the views of AltEnergyMag
Comments (0)
This post does not have any comments. Be the first to leave a comment below.
Featured Product
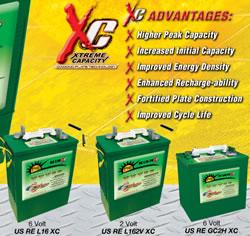
U.S. BATTERY RENEWABLE ENERGY SERIES DEEP CYCLE BATTERIES
Our RE Series batteries are designed to provide the highest peak capacity, longest cycle life, and greatest reliability for use in industrial or residential renewable energy applications. Renewable Energy Series batteries utilize the company's exclusive XC2™ formulation and Diamond Plate Technology® to create the industry's most efficient battery plates, delivering greater watt-hours per liter and watt-hours per kilogram than any other flooded lead-acid battery in the market. Our Deep Cycle batteries are engineered to work with solar panels as well as other renewable energy applications.