PV connectors are part of a system, and how well they connect and disconnect along with the ease of assembly & installation is important to installers. Electrical standards for PV connectors have been established through the National Electric Code (NEC) and UL. However no design and/or contact standards exist. The ‘defacto' standard has not been uniformly accepted by manufacturers. The need for compatibility and interchangeability is clear.
A Catch-22 in the PV Connector Industry?
John Wilczura | Remke Energy
From 1970 to 1983, PV installations grew rapidly as a result of the ’73 oil embargo and the 1979 energy crisis which brought renewed attention to develop solar technologies. But throughout the rest of the 1980’s there was only moderate growth due to falling oil prices. The Gulf War in 1990 once again renewed interest in solar power as an alternative to oil & petroleum products. Although few tax credits or incentives existed at that time, approximately 1.2 million buildings in the United States became solar heated in the mid 1990’s and over 1 million homes had some form of solar power installed.
In 1996 the first PV connector system was introduced. Known as Type 3 connectors, the bodies were made from a thermoplastic elastomer and used a friction fit to maintain a physical connection. This product required special tools and techniques which were not considered to be field-installation friendly. So several years later, in 2002, the Type 4 PV solar plug connector system entered the market and was able to coin the phrase ‘plug and play’. This style used connector bodies made from a type of hard plastic and were designed for easy assembly & installation with no special techniques or multiple tools required. By 2007 there were 19 different Type 4 PV connectors – by 2010 there were 38 different models. (Each with its own crimping tool.)
Grid-connected solar PV continues to be the fastest growing power generation technology. Although solar currently represents less than 0.5% of global electricity generation, as renewable energy gains importance in the US electricity market many are forecasting that solar PV shipments will continue to rise at a compound annual growth rate of 50% for the next four years. And what of solar PV connectors? With this type of projected growth is now the time to address the “Catch-22” situation in our industry?
What would happen if standardization was considered and discussed? Would long lead times for PV connectors - which idle some projects and leave installers & owners wringing their hands – cease to be a problem? It is widely accepted that everyone benefits from standardization. For customers there is a single solution worldwide with lower costs and interchangeability that eliminates multiple tool & retrofit costs. For manufacturers there are economies of scale, quicker marker acceptance, improved delivery & availability. For everybody there is a broadening of the supply chain. The more people who use a standardized product the more people will want to use a similar product.
PV connectors are part of a system, and how well they connect and disconnect along with the ease of assembly & installation is important to installers. Electrical standards for PV connectors have been established through the National Electric Code (NEC) and UL. However no design and/or contact standards exist. The ‘defacto’ standard has not been uniformly accepted by manufacturers. The need for compatibility and interchangeability is clear. The question is whether installers are willing to continue to accept the status quo OR do they want a single standard? A decision needs to be made about the “Catch-22” in our market and we believe that must come from the customer, the installer. Their voices need to be heard.
The content & opinions in this article are the author’s and do not necessarily represent the views of AltEnergyMag
Comments (0)
This post does not have any comments. Be the first to leave a comment below.
Featured Product
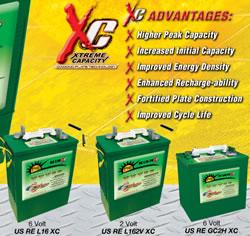
U.S. BATTERY RENEWABLE ENERGY SERIES DEEP CYCLE BATTERIES
Our RE Series batteries are designed to provide the highest peak capacity, longest cycle life, and greatest reliability for use in industrial or residential renewable energy applications. Renewable Energy Series batteries utilize the company's exclusive XC2â„¢ formulation and Diamond Plate Technology® to create the industry's most efficient battery plates, delivering greater watt-hours per liter and watt-hours per kilogram than any other flooded lead-acid battery in the market. Our Deep Cycle batteries are engineered to work with solar panels as well as other renewable energy applications.