Ligno cellulose consists of accumulated solar energy, however recovery of this energy is possible only through combustion processes with considerable environmental disadvantages. The proposed technology offers a completely different approach: The input materials are dissolved in a concentrated salt solution.
Bernard Scharle | CONSULTING INTERNATIONAL
1 - Basic facts and Design Criteria
Municipal wastes consist about 90% of biomass and plastics, that means of highly caloric material. Most of the available technologies for waste disposal (incineration, anaerobic digestion, gasification) aim at recovery of this energy. But in any case the waste disposal and reduction is the primary target while energy efficiency comes only second.
Besides plastics the ligno cellulose fraction of the biomass has an important part in energy recovery.
Ligno cellulose constitutes the most abundant biomass on earth, and even after using it for various applications, considerable amounts are available as waste material.
Ligno cellulose consists of accumulated solar energy, however recovery of this energy is possible only through combustion processes with considerable environmental disadvantages such as:
- environmental contamination by smoke,
dioxines, toxic particles
- considerable investment costs
- energy losses through drying of wet input material
The proposed technology offers a completely different approach: The input materials are dissolved in a concentrated salt solution. This involves the following advantages:
- A considerably increased energetic efficiency; approx. 80% of the energy contained in the input materials will be recovered!
- No-burn, no-emission technology
- CO2 – neutral, eligible for CDM certificates
- Moderate process conditions (200 °C, 6 bar)
- Small decentralised low-cost units
- Entire process takes place in liquid phase, which allows easy automation and control
- Large variety of input materials, also wet!
-
Low preparation effort required; input materials may be moist, contaminated,
in relatively large sizes of up to 20 mm - Output in form of clean synthesis gases (CO + H2), free from tar, free from particles
- Solid residues (only 4 – 8%, depending on the input material) consisting of ash, sand and other mineral residues plus insoluble and accordingly non-toxic salts, which can be disposed without danger of environmental pollution on landfills.
The following input materials are suitable:
- Strictly waste materials (no competition with food plants)
- Any type of wood (trunks, branches, chips, saw dust, also treated wood like railway sleepers, furniture etc.)
- Municipal Wastes, also contaminated with up to 20% plastics residues
- Straw, stover, reed grass, rice straw
- Residues (compost) from anaerobic digestion processes
- Shells, stones, kernels, husks from nuts, fruit, grain
- Press cake from oil and fruit pressing
- Materials washed ashore, on dykes or on weirs
- Slaughter house waste (hides, carcasses, bone meal)
- Animal manure
- No limitation in respect to input moisture
-
No limitation in respect to dirt, contamination,
safe elimination of toxic input materials such as Cl, S, Br, Cr, Hg etc. is assured.
This project is designed to treat municipal solid waste. The specific advantage as against anaerobic digestion lies in the fact that also cellulose components as well as plastics are converted into electricity which increase the yield of electricity to about four times.
Various Input Materials
![]() |
![]() |
![]() |
![]() |
![]() |
![]() |
2 - Description of DLE – Waste Treatment Process
2.1 - Preparation of Waste Input Material
The waste is dumped into the receiving area and then picked up by a payloader and fed into a coarse shredder which reduces particle size to about 20 mm.
The material may contain up to 50% of moisture; no drying is required!
The actual conversion process takes place in three stages:
2.2 - Liquefaction
Pre-shredded input materials are filled into the reactor vessel and mixed into a saturated alkaline salt solution.
A chemical reaction at 200 °C / 6 bar loosens the bonding of ligno-cellulose molecular structures, causing disintegration and dissolving of the biomass into a variety of soluble organic salts.
Mineral (unsoluble) particles sediment at the bottom of the reactor vessel from where they are extracted.
If necessary special additives bind toxic elements such as Chlorine, Bromine, heavy metals etc. into unsoluble compounds which are also eliminated by sedimentation
The remaining solution consists of pure organic energy-rich salts.
2.3 - Gasification
The liquid solution is pumped to a gasifier. Since all cellulose/lignin containing compounds have been broken down, the resulting synthesis gas (H2 + CO) is absolutely clean and free from tar.
Alkaline salts from the solution precipitate in form of a smelter along the walls of the gasifier from where they will be recovered for reuse in the reactor.
2.4 - Energy Conversion
The generated synthesis gas is decompressed and cooled down and taken to a CHP motor-generator. Overall energy conversion efficiency is 80% of which 40% will be recovered inform of electricity.
Excess heat amounting to 60% of the recovered energy is available for the process itself, but also for external use with various options
Flow Sheet DLE
The proposed plant will require two units of the shown size
2.5 - Optional Technology Components
2.5.1 - Additional Electricity Generation
The process liberates about 50% of the inherent energy in form of heat. This heat has not been valued for the time being but may be used with moderate additional investment to be formed into
- additional electricity
- cooling energy
- heating energy for drying processes or similar
2.5.2 - Fertiliser Production
The process residue contains all the mineral elements which the biomass has absorbed during its growth phase. These mineral salts such as Phosphorous, Nitrogen, Sulphur may be used as fertiliser.
2.5.3 - Material Recycling
Again with moderate additional investment instead of putting the dissolved slurry to energy generation valuable chemical base materials may be recovered from the liquid solution.
This solution contains a variety of phenol derivates which may be converted into high quality resins and glues, which then again may be used to produce wear and weather resistant slabs from straw fibers and/or wood
The content & opinions in this article are the author’s and do not necessarily represent the views of AltEnergyMag
Comments (0)
This post does not have any comments. Be the first to leave a comment below.
Featured Product
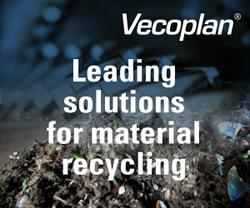