The greatest challenge for backsheet manufacturers is to develop product that meets strict performance requirements and industry standards, at a time when there is increasing pressure to reduce costs.
The Photovoltaic Backsheet Market
Michelle Ostiguy | FLEXcon
Please discuss the current soft market conditions of the photovoltaic backsheet market.
There are two issues facing the market: 1. Reduced government subsidies and 2. Oversupply. In regions such as North America and Europe, the government tax incentives and feed-in tariff programs have been significantly reduced. This lack of funding has reduced the amount of investment in photovoltaic. As well, there is an oversupply in the market. Module manufacturers are resorting to lower than average prices to move inventory. As such, solar projects are being quoted at lower than average pricing which, in turn, has pushed companies to lower or negative margins or, unfortunately, out of business.
What are the basic attributes of backsheets and what makes them so important?
The performance of the backsheet is a large contributor to the functionality and life of the panel. The backsheet, the multi-layer plastic laminate on the back side, serves to protect all of the componentry of the module. It protects against weather, moisture, humidity and serves as an electrical insulator. Failure of the backsheet is a safety risk - due to electrical leakage - and results in poor functionality or complete failure of the module.
Discuss the recent push in the market to reduce costs – what are the benefits and challenges for manufacturers?
The primary push in the marketplace to reduce costs is to continue to push solar energy to grid parity. This push ultimately benefits the consumer through a lower energy cost, greater adoption, of solar. The challenge for manufacturers and the supply chain, is that despite a push for reduced costs the same performance and quality standards of components and materials are required. High performance materials are costly, understandably, so driving costs down easily lends itself to erosion of profit.
Are there any specific challenges manufacturers have to deal with when developing backsheets?
The greatest challenge for backsheet manufacturers is to develop product that meets strict performance requirements and industry standards, at a time when there is increasing pressure to reduce costs. This challenges manufacturers to balance quality with cost through continued focus on cost down initiatives without compromising quality.
What is FLEXcon doing to address the need to develop new low-cost backsheets?
Given the push to reduce costs, and not compromise performance, FLEXcon continuously focuses on product development and manufacturing improvements. We look for ways to take cost out - through raw material, product and process changes. For example, our latest product launch - FLEXcon multiGUARD(R) KPE WW156 represents taking cost out of the product and not compromising performance. This product design is a thinner version of our standard KPE W12. By down gauging the Kynar(R) film slightly, we were able to pass on a savings while still meeting the quality standard for industry certifications.
Are we reaching the limits of lower cost and higher technology in backsheet manufacture or is there still lots of room for improvement?
FLEXcon continues to focus on product development and manufacturing improvements to continue to lower the cost of the backsheet. Beyond our KPE WW156, we have a line of sight for additional product design changes that we believe can yield savings. In conjunction with this, we continue to develop non-fluoropolymer products that also offer a savings.
How do you see the market for modules developing over the next few years and where do you expect the greatest growth to occur?
According to industry experts, the market is expected to improve in 2014 and beyond. In the meantime, to maintain survival, it will be key to balance reduced costs with a reasonable profit level.
FLEXcon is an ISO 9001:2008 certified manufacturer of pressure-sensitive films and adhesives, headquartered in Spencer, Massachusetts. We are an innovator in coating, laminating, and finishing of wide-web roll-to-roll polymeric materials, with expertise in graphics and label applications as well as bonding, barrier, optical, and electronics applications.
The content & opinions in this article are the author’s and do not necessarily represent the views of AltEnergyMag
Comments (0)
This post does not have any comments. Be the first to leave a comment below.
Featured Product
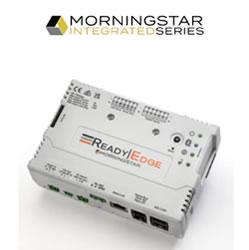