Both on paper and in the field, civil engineering can quickly drain your project’s margins. From the intricacies of installation logistics to the added costs of non-standard products, margins become slimmer as development becomes more and more complex.
How Civil Work Erodes Project Economics
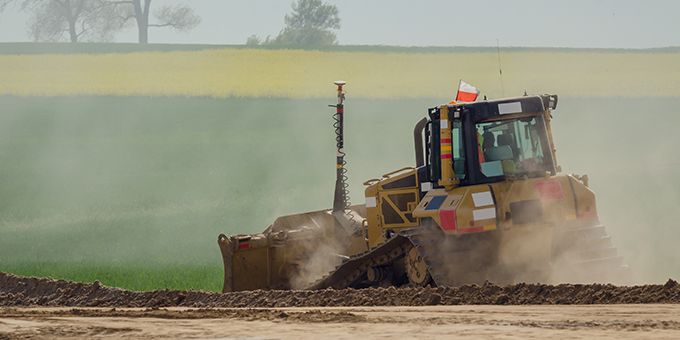
Bart Oegema | Sunfolding
Reprinted with permission from Sunfolding:
Both on paper and in the field, civil engineering can quickly drain your project’s margins. From the intricacies of installation logistics to the added costs of non-standard products, margins become slimmer as development becomes more and more complex.
Civil work and other site preparation might make for beautiful photographs of perfectly flat solar tracker arrays, but earthwork is expensive and can tip an otherwise great site into a geotechnical quagmire, and ultimately render a project financially unattractive.
Disturbing a site’s soil often requires rerouting wastewater and special accommodations to be made for native species, making engineering and installation lengthy and bureaucratically complex with the Authority Having Jurisdiction (AHJ), amongst other possible stakeholders.
Further complications can arise from challenging soil or variations in the site’s topography, which can cause unexpected changes to projected budgets.
The cost of adapting terrain to meet traditional solar tracker specifications — the flat-out expense of cut and fill, along with importing and exporting soil — combines with costs associated with additional steel for longer posts, detailed project engineering, and the complex installation logistics required for myriad post sizes.
You can quickly see the financial benefits of installing traditional solar trackers diminish as your project’s margins get squeezed.
Ditch the Motors and Stop the Squeeze
Choosing a motor-free solar tracker simplifies project engineering with an agile and site-responsive mechanical design that reduces the need to perform extensive earthwork. Motor-free trackers additionally open up development opportunities on sites that would otherwise be considered too challenging — with grades too steep or terrain undulations too large — for traditional tracker applications.
How? By eliminating motors, short tracker spans (down to or below a single string size) can adapt to the terrain with minimal disturbance. No additional, surprise cost for earthwork, and no additional cost for “partial rows”.
(Figure 1: Motor-free trackers, with short spans, can follow variations in the terrain)
Imagine developing a tracker project on a hill, where previously only a fixed-rack system could be economically installed. To do so requires a nimble tracker, that — as a standard product (read: without adding cost) — conforms and responds to a site’s topographic features with minimal site disturbance.
Or, let’s say you find a mostly flat parcel that has a sloped section with a 12.3% grade. Irradiance is ideal, and you still have capacity to fill. Why stop at the slope? Ideally, you would choose a tracking system that could handle that grade as a standard product, enabling you to fill the site completely.
(Figure 2: Higher slope tolerances on motor-free trackers allow the standard product to be installed on 12.3% grades)
What stops traditional trackers from being applicable or economical in these scenarios? Motors.
Motors, and the complex of equipment they come with — gearboxes, control boxes, self-power modules, torque tubes, driveshafts — require that you optimize their cost.
How do you optimize a motor’s cost? You need to add modules to a long tracker span to increase output, making long spans standard and preferred by traditional manufacturers.
The longer the span, the lower the slope tolerance, as traditional trackers become inflexible and unable to adapt to and follow varied terrain.
On slopes, the overall height of a tracker is important to ease installation of both the mechanical system and the modules. Even on low-grade slopes, traditional trackers require ladders during module installation, as the downhill posts grow in height. A 90-module long tracker at a 2% grade is 6 feet higher at one end than the other, whereas a 30-module long tracker is only 2 feet higher.
Module installation becomes cumbersome well before the 6-foot-mark and slows down the final phases of installation, which only gets magnified on large MW projects with hundreds of thousands of modules.
Trackers with short spans that are engineered to handle steeper slopes provide a more installation-friendly tracker height. Stair-stepping the trackers allows for significantly shorter post lengths on the downhill end while maintaining a low overall tracker height, which eliminates the need for ladders during module installation.
(Figure 3: Stair-stepping short spans lowers overall tracker height and eases module installation)
Installing short spans allows trackers to follow terrain variations; the shorter the span, the more readily the tracker adapts to topographic changes.
Sure, you can shorten the spans on traditional trackers with motors — referred to as “partial rows” — but that comes at additional cost, because, again, motors are expensive.
Motor-free trackers with short span lengths work with the terrain, allowing the array design to accommodate your site’s features, from hills to swamps, or an endangered species’ right of way. Tracker rows are no longer partial, they are simply modular, site-specific spans.
Move Beyond Civil Work
(Figure 4: On undulating terrain, traditional trackers often require extensive earthwork to meet tight specifications)
Traditional trackers require a combination of earthwork — cut and fill — and expensive partial trackers to meet tight equipment specifications. Figure 4 shows the cut and fill required to flatten a site’s topographic variations to level ground. In addition, accommodating this kind of terrain with a traditional tracker would require longer posts, which come at additional cost.
(Figure 5: Motor -free trackers follow the median grade and don’t require earthwork)
An efficient system design accommodates undulating terrain with posts that can maintain both the median grade of the slope and minimum embedment requirements without cut and fill. In this way, motor-free solar trackers can be deployed on undulating terrain without extensive disruption to a site’s features or creatures.
Choose a tracker that simply and flexibly adapts to your site’s terrain and move beyond cut and fill. With the right tracker, new development opportunities arise as plots of land open up to the benefits of tracking, moving solar far beyond flat and perfectly shaped parcels and returning the full suite of yield benefits that solar tracking should bring.
The content & opinions in this article are the author’s and do not necessarily represent the views of AltEnergyMag
Comments (0)
This post does not have any comments. Be the first to leave a comment below.
Featured Product
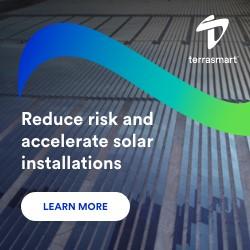