This paper will review recent advancements in wind energy over the last two to three years, with specific focuses on improving wind energy harvesting, offshore wind turbine foundation designs, and decreasing turbine fatigue.
Latest Technical Breakthroughs in Wind Energy
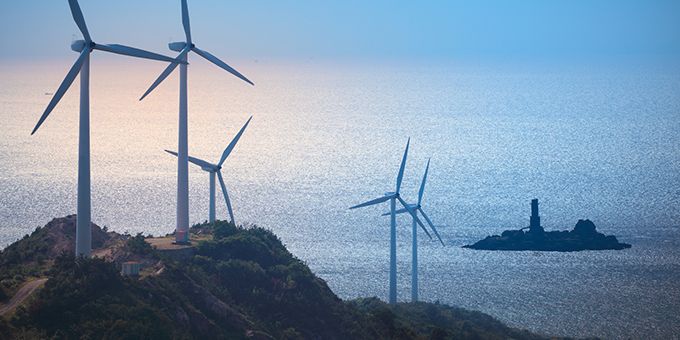
Dr. Raj Shah and Ms. Amanda Loo | Koehler Instrument Company
Introduction
CO2 emissions were 31.5GT in 2016, causing a need for more eco-friendly energy systems to be used [1]. In 2018, there were more than 11 million jobs for renewable energy in the solar energy, bioenergy, hydropower, wind power, and geothermal sectors. Around 90% of renewable energy is in the form of solar and wind energy, with wind energy predicted to produce around 20% of global electricity in 2050 [2]. The wind energy industry is expected to grow from approximately USD 100 billion to USD 1 trillion per annum by 2050 [3]. This paper will review recent advancements in wind energy over the last two to three years, with specific focuses on improving wind energy harvesting, offshore wind turbine foundation designs, and decreasing turbine fatigue.
Wind Energy Harvesting
Electromagnetic generators (EMGs) convert wind energy to electric energy but typically have low voltage values and high costs. Triboelectric nanogenerators (TENGs) convert mechanical energy into electric power and have high voltage values and low costs compared to EMGs [4]. Many different energy harvesting applications, like wind, water flow, and acoustic waves, use TENG. Developing improvements for these existing conversion techniques or combining EMG and TENG to create hybrid generators has been done to improve harvesting wind energy.
Gravity triboelectric nanogenerator (G-TENG) demonstrates steadier wind harvesting than regular TENGs and is a better way to convert wind energy to electric energy [5]. G-TENG focuses on more constant TENG output by converting wind energy to gravitational potential energy to electric energy. It was found that the G-TENG is sufficient for energy conversion in natural wind environments. Furthermore, ball-shell structured TENG (BS-TENG) have been studied and are designed with two shells with two electrodes and dielectric layers surrounding a ball [6]. The ball moving and touching the shells creates a current through the ball becoming tribo-electrified, allowing for an irregular motion to generate energy. These BS-TENG networks are sensitive to small agitations, and it was found that flexible connections had higher charge outputs than rigid connections when faced with water waves of 1 and 2Hz frequencies. BS-TENG is a practical design for wave energy harvesting as connections with coupling effects are very efficient in collecting energy.
Aside from the low voltage values and high costs, another shortcoming of EMGs of current wind turbines is that the minimum threshold speed is 3m/s for energy conversion. An important goal to improve wind energy harvesting is to create TENG devices that can harvest energy at low wind speeds [7]. Gentle wind-driven TENG (GW-TENG) has been developed, and it can produce high output power density at wind speeds of 0.7-6m/s from objects such as laptop fans and airflow from moving cars. A 7.8% conversion efficiency was observed at gentle wind speeds of 2.5m/s and a 20mW/m3 power output was observed at wind speeds of 0.7m/s.
Figure 1. GW-TENG output signals of wind induced from moving cars.
Figure 1 demonstrates how GW-TENG can generate electricity after interacting with air traveling from a car moving 40km/h, with the output signals increasing as car speed increases. This study shows the possibility of incorporating GW-TENG into future wind turbine designs to enhance the wind threshold speed of these turbines.
Offshore Wind Turbines and Energy
Offshore wind technology is exposed to consistent and fast wind speeds in deeper water. There is currently offshore floating wind technology installed in Western Europe with potential projects in the U.S. East and West coasts as well as Japan [2]. Offshore wind energy is more efficient than onshore wind energy as the electric output can be up to 1.7 times greater [1]. Furthermore, offshore wind technology has lower noise levels compared to onshore technology, and its location selection is not as significant [8]. Onshore wind installments must consider aesthetics and the public’s opinions before building, while offshore wind installments do not require these precautions.
Table 1. 2019 onshore and offshore European wind energy in megawatts (MW) [2].
According to Table 1, although onshore wind energy was produced in more countries as of 2019, the value of offshore wind energy that was produced by the four countries of the UK, Denmark, Belgium, and Germany are individually quite high. The WindEurope’s Central Scenario projects by 2030 aim to instill a total of 323GW of wind energy capacity, with 253GW for onshore installations and 70GW for offshore installations [9]. A significant inclusion of offshore instillations can be seen by the EU as it has been determined that these installations can generate a greater amount of electricity than onshore installations.
Offshore wind turbines (OWTs) require a foundation structure during installation, which can account for their higher costs than onshore wind turbines. Figure 2 represents four common types of foundation structures. Gravity foundations are typically used at depths less than 10m [8]. The monopile foundation has low costs, and both gravity and monopile foundations have a limited water depth. The tripod and jacket foundations have limited water depths as well, with the tripod being used at depths up to 50m and the jacket being used at up to 80m. However, both structures are costly [1].
Figure 2. Illustrated designs of four foundations for offshore wind turbines [8].
There have been many previous studies on hybrid monopile foundations to increase efficiency and operating time over the last 50 years [10]. Yet many of these studies did not focus on cyclic behaviors of the foundations, which are mattering as OWTs experience cyclic external loads from nature during their course of use. Therefore, studying cyclic behaviors acting on foundations allows for more realistic and reliable research. In a 2019 study, the cyclic behaviors of the hybrid monopile foundation were studied and it was found that the hybrid model had larger bearing capacities and smaller lateral deformations in cyclic behaviors compared to the standard monopile foundation [11]. The hybrid model’s design incorporates a wheel at the mudline of the foundation, which resists lateral displacement and helps to stabilize the foundation.
Determining the efficiency of hybrid monopile foundations can be done by using calculations looking at soil interactions and deformations. The Spang method of Germany in 1970s, Bakulina method of Russia, and Mathus method of Ukraine are few examples of the hybrid monopile foundation designing methods. These methods include many assumptions and result in unreliable conclusions, meaning that a more accurate model is desired to increase OWT efficiency [10]. The measuring stability of hybrid foundations is desired with these methods, and it was recently found in 2021 that using an iterative algorithm can result in more accurate calculations for designing hybrid monopile foundations. Finding ways to increase accuracy within designing methods can reduce errors and increase the efficiency and lifetime of the hybrid foundations.
Turbine Fatigue
Offshore wind turbines can experience fatigue from exposure to constant wind and marine conditions [12]. One 1.5MW wind turbine can generate a year’s energy supply for 332 homes, and a 10GW wind farm can generate a year’s energy supply for 7.5 million homes in the UK. These numbers show how valuable wind turbines are to generating energy and reducing turbine fatigue is crucial to maintaining these values.
Loading events from the operation or extreme loading, such as severe weather conditions, cause turbine fatigue. A typical wind turbine for 20 years of use incorporates 109 fatigue loading cycles in its design [13]. High strength steel and fracture toughness is desired for WT design material.
Figure 3. Environmental interactions with offshore wind turbines and their respective load type [14].
Figure 3 shows OWT interactions with wind, waves, and soil and the parts of the turbine that these environmental concerns affect. In a 2014 experiment, dual linear tuned mass dampers (TMDs) were used to reduce side-side wind motion fatigue up to 40% but only bi-directional wind motion fatigue up to 5% [15]. In place of this, a three-dimensional pendulum tuned mass damper (3d-PTMD) to reduce turbine fatigue in marine conditions was used as TMDs are expensive, large, and challenging to install. It is already known that 3d-PTMD reduces bi-directional wind motion fatigue better than dual linear TMDs, and this study demonstrated 3d-PTMD’s superiority in real marine conditions to reduce fatigue [12].
It is known that the rotor module of a wind energy conversion system (WECS) considerably contributes to downtime, where the system is halted and is unable to perform until it can resume after a certain amount of time. Marine conditions can affect rotor modules and lead to turbine downtime. In a 2019 study, a damage evaluation model was incorporated into the main control loop, and this reduced turbine damage during simulation periods of wind speeds up to 22m/s [16]. Damage was reduced by up to 40%, demonstrating that using a damage evaluation model acting as a control strategy extended the lifetime of WECS under wind conditions.
Conclusion
There have been many recent technical advancements for wind energy. The process of harvesting wind energy has been improved through modifications in triboelectric nanogenerators and expanding the range of wind speeds that can be captured through gentle wind-driven TENG. Furthermore, offshore wind turbine foundation design has changed with hybrid monopile foundations that can resist lateral wind displacement. Reducing turbine fatigue is also discussed because this can lessen the lifetime of wind turbines. Using a three-dimensional pendulum tuned mass damper has proven to decrease fatigue through limiting bi-directional wind motion damage. These advancements have supported the growth of wind energy as its popularity continues to rise globally.
About Dr. Raj Shah
Dr. Raj Shah is a Director at Koehler Instrument Company in New York, where he has worked for the last 25 years. He is an elected Fellow by his peers at IChemE, CMI, STLE, AIC, NLGI, INSTMC, The Energy Institute and The Royal Society of Chemistry An ASTM Eagle award recipient, Dr. Shah recently coedited the bestseller, “Fuels and Lubricants handbook”, details of which are available at https://www.astm.org/DIGITAL_LIBRARY/MNL/SOURCE_PAGES/MNL37-2ND_foreword.pdf
A Ph.D in Chemical Engineering from The Penn State University and a Fellow from The Chartered Management Institute, London, Dr. Shah is also a Chartered Scientist with the Science Council, a Chartered Petroleum Engineer with the Energy Institute and a Chartered Engineer with the Engineering council, UK. An adjunct professor at the Dept. of Material Science and Chemical Engineering at State University of New York, Stony Brook, Raj has over 400 publications and has been active in the petroleum field for 3 decades. More information on Raj can be found at https://www.petro-online.com/news/fuel-for-thought/13/koehlerinstrument-company/dr-raj-shah-director-at-koehler-instrumentcompany-conferred-with-multifarious-accolades/53404
About Amanda Loo
Ms. Amanda Loo is a student of Chemical engineering at SUNY, Stony Brook University, where Dr. Shah is the current chair of the External Advisory board of directors for the department. She is currently an intern at Koehler Instrument Company.
References
[1] Wang, X., Zeng, X., Li, J., Yang, X., & Wang, H. (2018). A review on recent advancements of substructures for offshore wind turbines. Energy conversion and management, 158, 103-119.
[2] Darwish, A. S., & Al-Dabbagh, R. (2020). Wind energy state of the art: present and future technology advancements. Renewable Energy and Environmental Sustainability, 5, 7.
[3] Veers, Paul, et al. (2019). Grand challenges in the science of wind energy. Science, 366(6464).
[4] Guo, Y., Chen, Y., Ma, J., Zhu, H., Cao, X., Wang, N., & Wang, Z. L. (2019). Harvesting wind energy: A hybridized design of pinwheel by coupling triboelectrification and electromagnetic induction effects. Nano Energy, 60, 641-648.
[5] Wang, Yuqi, et al. (2021). Gravity triboelectric nanogenerator for the steady harvesting of natural wind energy. Nano Energy, 82, 105740.
[6] Xu, Liang, et al. (2018). Coupled triboelectric nanogenerator networks for efficient water wave energy harvesting. ACS nano, 12(2), 1849-1858.
[7] Ren, Zewei, et al. (2020). Energy Harvesting from Breeze Wind (0.7–6 m s− 1) Using Ultra‐Stretchable Triboelectric Nanogenerator. Advanced Energy Materials, 10(36), 2001770.
[8] Wu, Xiaoni, et al. (2019). Foundations of offshore wind turbines: A review. Renewable and Sustainable Energy Reviews, 104, 379-393.
[9] Bórawski, P., Bełdycka-Bórawska, A., Jankowski, K. J., Dubis, B., & Dunn, J. W. (2020). Development of wind energy market in the European Union. Renewable Energy, 161, 691-700.
[10] Trojnar, K. (2021). Simplified design of new hybrid monopile foundations for offshore wind turbines. Ocean Engineering, 219, 108046.
[11] Wang, X., Zeng, X., Li, X., & Li, J. (2019). Investigation on offshore wind turbine with an innovative hybrid monopile foundation: An experimental based study. Renewable Energy, 132, 129-141.
[12] Sun, C., & Jahangiri, V. (2019). Fatigue damage mitigation of offshore wind turbines under real wind and wave conditions. Engineering Structures, 178, 472-483.
[13] Igwemezie, V., Mehmanparast, A., & Kolios, A. (2019). Current trend in offshore wind energy sector and material requirements for fatigue resistance improvement in large wind turbine support structures–A review. Renewable and Sustainable Energy Reviews, 101, 181-196.
[14] Velarde, J., Kramhøft, C., & Sørensen, J. D. (2019). Global sensitivity analysis of offshore wind turbine foundation fatigue loads. Renewable energy, 140, 177-189.
[15] Stewart, G. M., & Lackner, M. A. (2014). The impact of passive tuned mass dampers and wind–wave misalignment on offshore wind turbine loads. Engineering Structures, 73, 54-61.
[16] Njiri, J. G., Beganovic, N., Do, M. H., & Söffker, D. (2019). Consideration of lifetime and fatigue load in wind turbine control. Renewable energy, 131, 818-828.
The content & opinions in this article are the author’s and do not necessarily represent the views of AltEnergyMag
Comments (0)
This post does not have any comments. Be the first to leave a comment below.
Featured Product
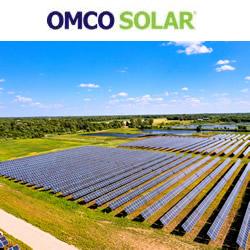