In PV systems, it is recommended to use copper core AC cables. If you need to use aluminum wires, pay attention to the transition method when connecting aluminum cables to copper wires or equipment with copper terminals.
Correct Use of Aluminum Core Cables in PV Systems
Article from | Solis Inverters
Grid transmission cables are usually aluminum core. Therefore, in the construction of PV plant projects in residential and commercial areas (especially household PV plant), many users will use aluminum core cables to directly interface with inverter output ports or circuit breakers ports. This can cause many safety problems. This Solis seminar will share with you the correct connection of copper and aluminum cables.
Figure1: In PV plant electrical connection problems, AC side faults account for 30%,
What happens when copper and aluminum conductor are directly connected?
-
Formation of galvanic cell reaction: When copper and aluminum conductors are directly connected, the contact surfaces of these two metals easily form galvanic cells in the air. This causes galvanic corrosion of aluminum and increases the contact resistance at the junction of copper and aluminum conductors.
-
Increase contact resistance: The elastic modulus and thermal expansion coefficient of copper and aluminum are very different. After multiple cooling and heating cycles (power-on and power-off) during operation, a larger contact gap will be generated at the contact point, which increases the contact resistance. The increase in contact resistance will cause the temperature of the contact point to rise, and finally lead to the burning of cables and equipment interfaces.
Why can't copper wire and aluminum wire be directly connected?
-
The resistivity of aluminum wire and copper wire are different.
Figure2: Resistivities of common metals
-
Aluminum wire is easily oxidized by air, and a layer of oxide is formed on its surface, which will increase the contact resistance of the contact point between the aluminum wire and the copper wire. When the current passes through this contact point, the heat will be increased at the connection point and could potentially result in a fire.
Figure3: Copper wire and aluminum wire cannot be directly connected
-
According to safety operation regulations, aluminum wires cannot be directly connected to copper wires or copper conductor terminals.
How to correctly connect copper and aluminum wires
-
To connect single strands of small cross-section copper and aluminum wires, a tin-plate on the copper wires should be done and then it can be connected to the aluminum wires.
Figure4: Soldering Cu-Al cable
-
When connecting multiple large cross-section aluminum wires with copper wires or circuit breakers containing copper conductor terminals, a Cu-Al Wire connector should be used.
Figure5: Cu-Al Wire Connector
Note
-
In a dry room, copper conductors should be tinned and then connect to Al wire. Outdoors or where the relative humidity of the air is close to 100%, a Cu-Al Wire connector should be used along with tin-plating the copper terminals.
-
For terminal crimping, always use professional equipment and crimp the wires tightly.
Summary
In PV systems, it is recommended to use copper core AC cables. If you need to use aluminum wires, pay attention to the transition method when connecting aluminum cables to copper wires or equipment with copper terminals. If the method is incorrect, the cables could cause a catastrophic event.
If you have any other questions, you can contact your local Solis support engineer: www.solisinverters.com/aftersales.html. Solis is one of the world's largest and most experienced string inverter manufacturers with a global network of service teams.
The content & opinions in this article are the author’s and do not necessarily represent the views of AltEnergyMag
Comments (0)
This post does not have any comments. Be the first to leave a comment below.
Featured Product
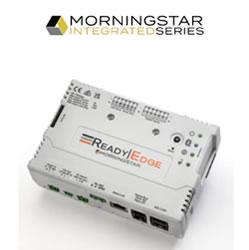